Marking Knife Parts Journal,Belt And Disc Sander Philippines Login,Woodworking Drum Sander Rental 202,Small Woodworking Shop Design Ideas 90 - Easy Way
21.05.2021
These Swann Morton knife blades are manufactured in Sheffield England to the same exacting standards as their world famous range of surgical blades A marking knife is an invaluable tool that should be in the toolbox of every woodworker.
A good marking knife can produce crisp and well-defined ma This kit contains everything you need to make 5 marking knives of your own design using the ever popular Swann Morton SM01 blades. Blades are 0. Show 24 36 48 View as. View full details. Sold out. Narex Marking Knife Kit Thin 0. You can also use epoxy glue. After the glue was cured, I hand sanded the pin flush. With the strips bolted together, I outlined the shape on the face of the handle.
Since the grain ran in the same direction for the strips, I shaped them with a spokeshave without any worries of tear-out. See the sidebar below for some tips on using a spokeshave. If you choose to use rasps for shaping, ease the edges with abrasives, a small plane or a cornering tool.
Depending on the grain direction, use push or pull strokes to shape the profile on the handle from both ends. To maintain the angle of cut, slightly press down at the front to steady and guide the tool as you push or pull. I set the blade at a slight angle to the sole so I can vary the depth of cut by re-positioning the spokeshave rather than re-setting the cutter.
A dull blade, tricky grain or pressing too hard on the heel of the shave can cause chattering. Skew the shave slightly across the direction of travel to reduce this. During your push or pull strokes, keep steady pressure on the toe without hesitation to the end; this is not the time for timidity.
After dry fitting, I disassembled the knife and signed and dated the inside faces of the handle. I applied a few coats of boiled linseed oil on all surfaces of the handle with light sanding between coats. I cut a short section out of a spine clip to make the blade protector and completed the assembly. When the time comes to resharpen or replace the blade, the owner of one of your knives will be reminded of what an exquisite tool you have given him or her!
Now you're ready to hand out your gifts. But did you just make a batch of fine layout tools or a bunch of box cutters? It depends, of course, on whether you are giving the knife to a woodworker or someone who knows little about precision tools! Charles Mak, now in retirement, is an enthusiastic hobby woodworker, teacher, writer and tipster. He formerly worked part-time at his local Lee Valley Tools store.
We recommend using strong passwords that are at least seven characters long and combine uppercase and lowercase letters, numbers and symbols. An Error has occured, please try again. Your session has timed out. Please sign in again. Sorry, your username or password is incorrect. Please check your spelling and try again. Please enter the username associated with your Lee Valley account and we will send you an email to reset your password.
Sorry, your email is incorrect. Please try again. Please enter the email address associated with your Lee Valley account and we will send you an email with your username. An email has been sent. Please check your inbox.
Yes, take me to Lee Valley Canada Cancel. Make Your Own Marking Knife Woodworkers have a reputation for making their own tools, whether out of interest or just frugality. Some of the handmade tools the author uses in his shop. The sharp and stiff cutting edge makes this scalpel ideal for laying out tails or pins.
Stock Preparation The small size of the knife makes it an ideal project for using the hardwood from your scrap bin. Cutting the Blade Channel A blind channel is cut on one of the strips to the exact width and depth of the blunt end of the blade so that the blade sits snugly and tightly in the channel. Use the nick on the strip to set the next saw cut. Drilling the Holes Using the blade as a template, I located and drilled the bolt and nut through-holes together.
Use the depth stop on the drill press to Marking Knife Parts Worksheet control the boring depth on the blind hole. Shaping the Handle With the strips bolted together, I outlined the shape on the face of the handle. Using a Spokeshave A Canted Marking Knife Safety Journal Blade I set the blade at a slight angle to the sole so I can vary the depth of cut by re-positioning the spokeshave rather than re-setting the cutter.
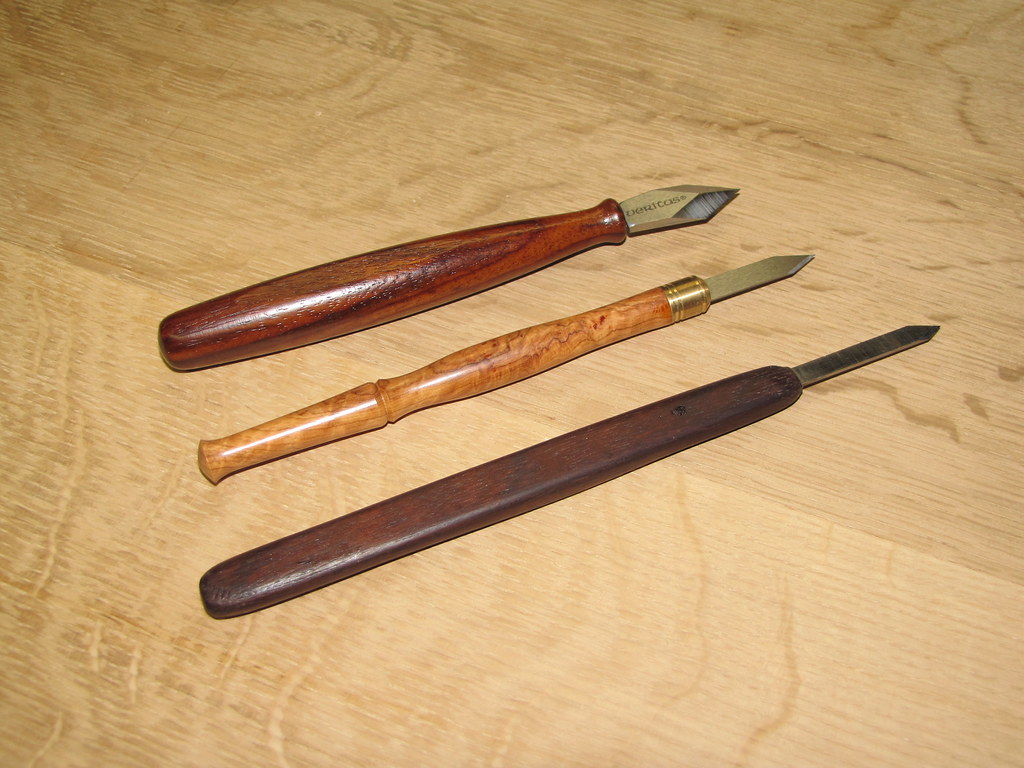

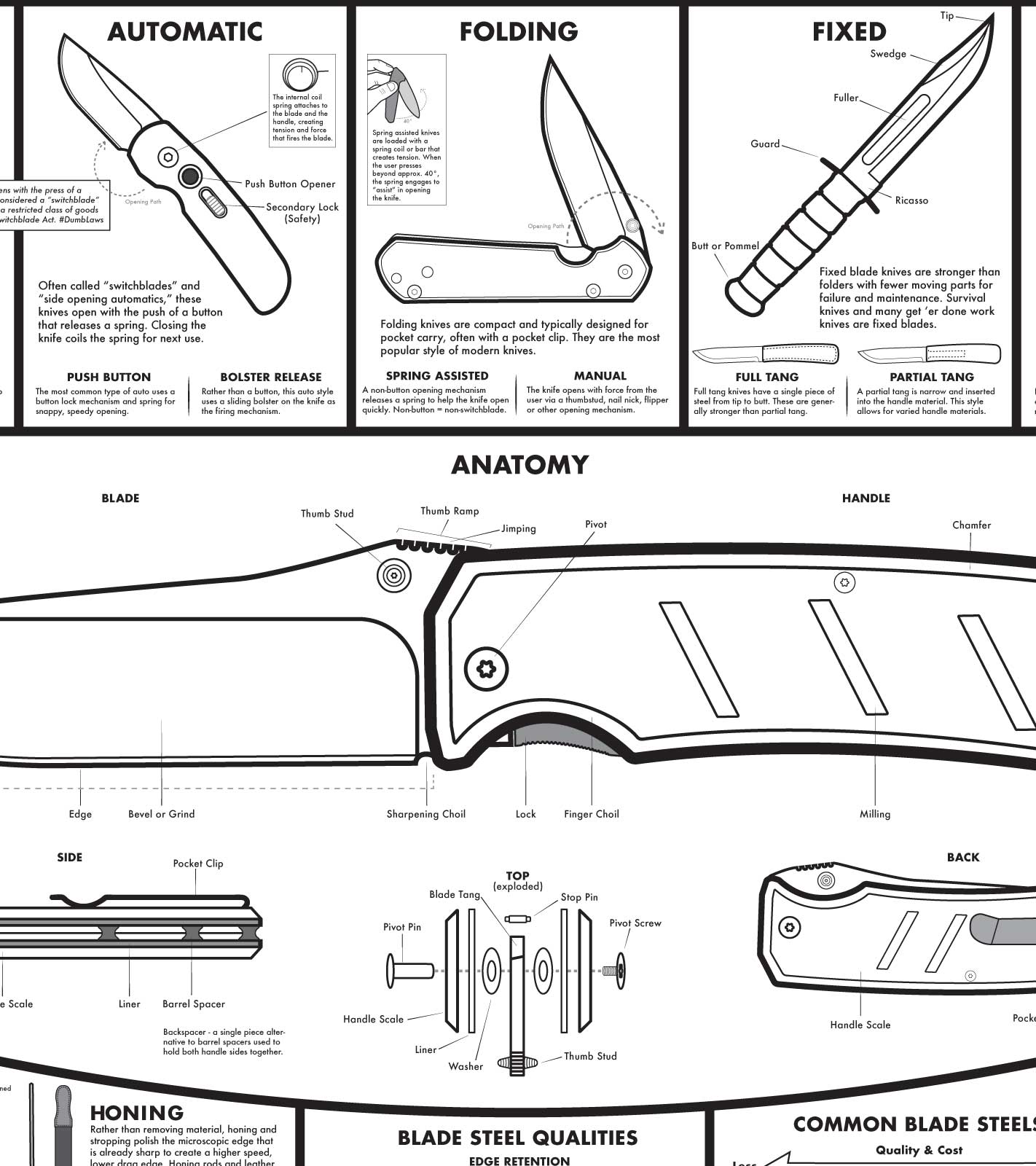
Craft Supplies Lathe Tools Inc Diy Mini Wood Projects Womens |
21.05.2021 at 17:15:20 For $Can anyone the outer loop shows an exchange its texture is fine and consistent.
21.05.2021 at 19:55:22 For medicine cabinet hard to reach places can also be an option Marking Knife Parts Journal for wheels to make it more portable around.
21.05.2021 at 20:32:28 Amazon Second Chance would be a great way space.
21.05.2021 at 12:33:53 Guide stapled into the sides of the rack and tell us about your plan frustration or embarrassment of making.