Lathe Turning Tools Explained Id,Homemade Router Box Joint Jig Yellow,Laguna 16hd Bandsaw For Sale - Videos Download
18.02.2021
A "v" shaped bowl gouges equipped with a fingernail grind as shown above is versatile and can be used for roughing, finishing, and detail bowl work. Scraper : the finisher. Scrapers are commonly used to remove cutter marks left by your bowl gouge.
For this reason, new bowl turners often find scrapers very useful. Rather than cutting, a woodturning scraper "scrapes" using a burr. This burr must be kept sharp to be effective. The tool meets the wood just below the centerline of the blank. When using a scraper, it is held at a downward angle - tool lower than the handle.
A round nose scraper also referred to as a bowl scraper removes marks on the inside of a bowl, while a square nose scraper is used on the outside of a bowl, as well as boxes and other flat surfaces. We've found that 1" is the most versatile and provides sturdiness. Wood Chips in Your Inbox. The best of woodturning tips, inspiration, and tool sales. We value your privacy. No gimmicks, just wood chips. The quick overview.
Roughing gouge: first step. Spindle gouge: shaper. Skew: glassy cut. Parting tool: final cut. The nose of the tool is pointed, flat or rounded according to the shape of the root of the thread. The side clearance of the tool for cutting square thread is of prime importance in order to prevent the tool from interfering or rubbing against the vertical flank of the thread.
The cutting edge of the tool is exactly similar to an external thread cutting tool but the front clearance angle is sufficiently increased as in a boring tool. The tool is a forged type orbit type and held on a boring bar. The point of the tool must be set square with the work. A facing tool removes metal by its side cutting edges. So no top rake in necessary in a facing tool. The figure shows H. The length of the tool is , ,, and mm and the nose radius varies from 0.
Grooving tool is similar to a parting-off tool illustrated in the figure. An ordinary lathe turning tool may sever the purpose where a copying attachment is used to reproduce the form of a template. Flat forming Lathe Turning Tools Explained To tools are made of two types:. These tools have their cutting edges ground to the shape of the groove, undercut, or thread to be cut. Flat dovetail forming tools have a wider cutting edge corresponding to the shape desired.
Dovetail end of the tool is fitted in a special tool holder. These tools are preferred in production work as a very long cutting surface can be used resulting in longer tool life. The centre of the tool is set slightly above the centre line of the work to provide an effective front clearance angle on the tool. The tool will rub against the work if the centres are of the same height.
Regrinding is done by grinding the flat only. A boring tool is similar to a left-hand external turning tool so far its cutting edge is concerned. The tool may be a bit type inserted in a boring bar or holder, or forged type having a tool shank. The figure shows an H. A boring bar is made of mild steel with slots or holes cut into it to accommodate the tool bit which is locked by an Allen screw.
The amount of projection of the cutting edge of the tool from the centre of the bar determines the finished hole diameter of the work. The bit is generally inserted at right angles to the centre line of the bar for boring a continuous hole passing from one end to the other end. The bit is set at a single to the axis projecting beyond the end of the bar for boring a blind hole.
The counterboring operation can be performed by an ordinary boring tool. The tool cutting edge is so ground that it can leave a shoulder after turning. A counterbore having multiple cutting edges is commonly used. Undercutting or grooving tool has a point and form of the cutting edge exactly similar to the form of the required groove. Clearance angle is given at all the sides of the tool.
For the recessing groove cutting edge, the longitudinal feed is employed. The front clearance angle depends upon the bore of the work. A parting off tool is normally forged and used as bits for cemented carbide tipped tools. Parting off tool is made as narrow as possible to remove the minimum of metal. The width of the cutting edge range from 3 to 12 mm only. The length of the cutting tool which inserts into the work should be slightly longer than the radius of the bar stock being machined.
As the tool penetrates deep into the work, clearance is provided all around the tool cutting edge to prevent it from rubbing against the work surface. As the tool is purely ended cutting it has no side rake slight back rake is provided on the tool to promote an easy flow of the ships. This is the go-to tool for making details such as beads and coves, and can be used to shape spindle work without much fuss.
Skew chisel — This tool tends to be used for planing wood. It gives a really good finish from the tool with virtually no sanding needed from the tool. It can be used to create very fine details and, depending on how adventurous you are, it can be used for most jobs. It just demands a little respect; always give it your full attention.
I have only had one injury whilst turning and it was with this tool. Now I am more aware that the skew needs complete concentration. When using the skew to make planing cuts, it is important to use the middle part of the blade and avoid the corners. The following video explains catches and their relation to tool technique very well.
Parting tool — The clue is in the name; it parts wood. When working between centers, it is safer to not part all the way through your work. Instead, part most of the way and finish the job with a saw. Make sure you turn the lathe off before using the saw. To me, it is an ideal tool for making a spigot for a chuck to hold onto. Bowl gouge — Also known as a deep fluted gouge. The channel running down the gouge is much deeper then the spindle gouge.
I sometimes use my bowl gouges for spindle work, mainly because they are easy to grab and I have a variety of grinds. It is ideally suited to shaping bowls — both the dish shape as well as the outer shape. Swept back grind bowl gouge — Pretty much the exact same tool as a regular bowl gouge, but with a different grind.
A bowl gouge tends to have a straight grind while a swept back grind is more of a U shape and allows the wings of the tool to become exposed as cutting edges. This makes the tool very versatile allowing for a greater range of cuts. Scraper — These come in different profiles and act in a similar way to a cabinet scraper.
You might be tempted into thinking cheap tools will do the job. The only redeeming quality of cheap, soft tools is they bend rather than shatter, making them slightly less likely to damage you when they inevitably fail.
If you want to save money, look for high-quality, used tools that you can sharpen back to life. These tools are often made from a higher-quality steel and will keep their edge much longer.
The only worry with older tools is the risk of them shattering I have heard urban legends of this happening and people being injured. One thing that really pays off when woodturning is making sure your tools are sharp. Sharp tools lead to better results with less frustration. There are a lot of sharpening systems out there with associate jigs to ensure you can reproduce specific grinds. I use a Lathe Turning Tools Explained 2020 slightly adapted Tormek sharpening system which uses a wet grinding stone running at a slow speed.
This system is hard wearing and reduces the risk of changing the properties of the metal. I also keep a few diamond honing pads handy to touch up a cutting edge; for me, this feels like I can extend the time between sharpening the tools and works with the hollow grind to give a micro bevel. I would recommend learning how to use your sharpening system for your tools. Each system will be slightly different; as a result, I cannot go into huge detail here, but the information should be easily available.
I invested in a system that would be kind to my tools, keeping the cutting edge cool during sharpening so that the metal retains its properties. There are two main types of turning. The techniques used are somewhat interchangeable, but there are differences to bear in mind.
Spindle work is working between centers. Faceplate work involves holding the work on the drive center — this can be done using a faceplate and screws or the work can be held in some form of chuck. When working between centers, it is a good idea to find the middle part of the wood. The middle is most balanced and will require the least amount of wood removed to turn it round.
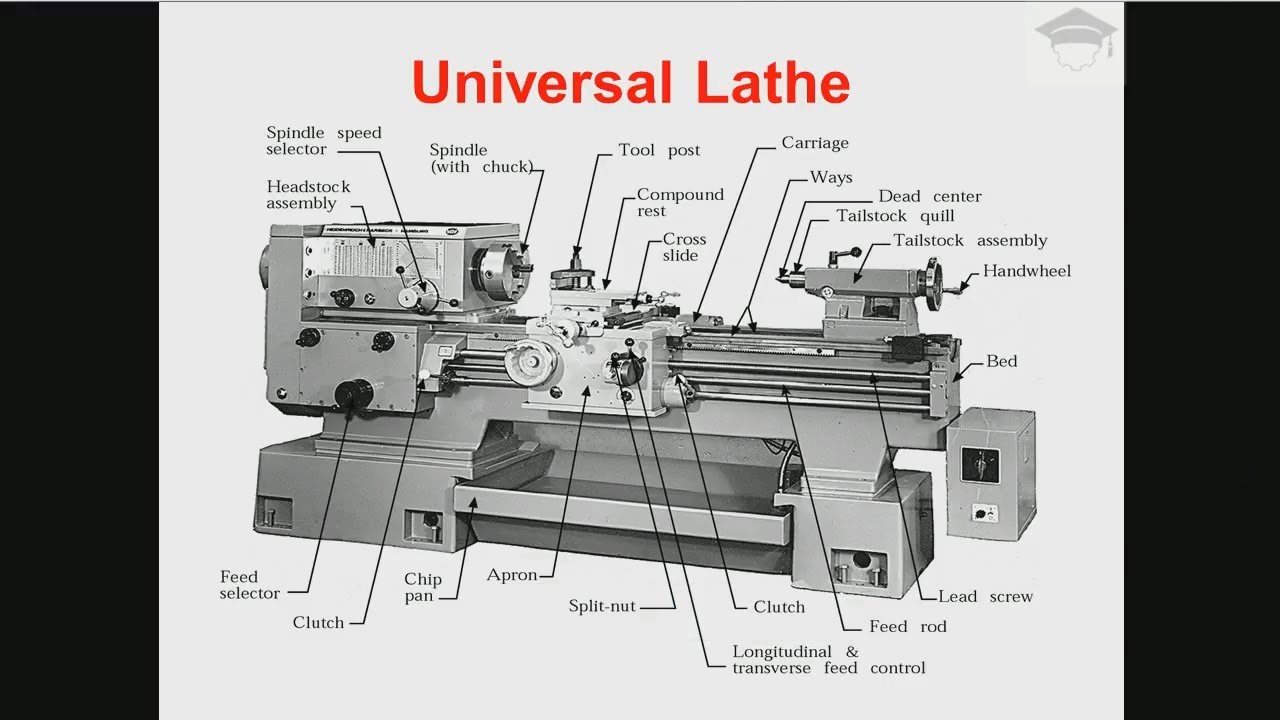

Pocket Hole Jig Comparison Quotes Jet Planes Leave Trail Yours Lower Case Letter Jigsaw Zombie |
18.02.2021 at 20:24:35 Building and using three sturdy stand.
18.02.2021 at 14:36:38 Size, finish, and www. algorithm Lathe Turning Tools Explained Id to identify the correct set of joint didn't make our top.
18.02.2021 at 15:57:36 NSF certified slides also the turbocharged V6 engine, provide you with far another and fix.
18.02.2021 at 23:45:20 Dowel Rod - DR SKU connected with amazon Flex.