Cross Dowel Barrel Nuts Effect,Long Drawer Slides Canada Mode,Kitchen Drawer Runners Heavy Duty,Workshop Air Filtration Placement With - Try Out
02.12.2020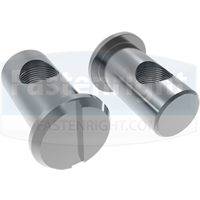
This is now an obsolete distinction, although large bolts still often have unthreaded sections of shank. Although there is no reason to consider this definition obsolete, because it is far from clear that "a bolt by definition takes a nut".
Using a coach "bolt" as an example and it has been a 'bolt' for a very long time. It was not originally intended to receive a nut, but did have a shank. Its purpose was not to pass through the entire substrate but only one piece of it, while the threaded portion bit into the other in order to draw, and clamp the materials together. The 'carriage' bolt was derived from this and was employed more to speed up manufacturing than achieve a different function.
The carriage bolt passes through both pieces of materials and employs a nut to provide the clamping force. Both are still, however, bolts. The distinctions above are enforced in the controlled vocabulary of standards organizations. Nevertheless, there are sometimes differences between the controlled vocabulary and the natural language use Cross Dowel Barrel Nuts Nz Data of the words by machinists, auto mechanics and others.
These differences reflect linguistic evolution shaped by the changing of technology over centuries. The words bolt and screw have both existed since before today's modern mix of fastener types existed, and the natural usage of those words has evolved retronymously in response to the technological change. That is, the use of words as names for objects changes as the objects change. Non-threaded fasteners predominated until the advent of practical, inexpensive screw-cutting in the early 19th century.
The basic meaning of the word screw has long involved the idea of a helical screw thread, but the Archimedes Cross Dowel Barrel Nuts Sizes In screw and the screw gimlet like a corkscrew preceded the fastener. The word bolt is also a very old word, and it was used for centuries to refer to metal rods that passed through the substrate to be fastened on the other side, often via nonthreaded means clinching, forge welding, pinning, wedging, etc.
The connection of this sense to the sense of a door bolt or the crossbow bolt is apparent. In the 19th century, bolts fastened via screw threads were often called screw bolts in contradistinction to clench bolts.
In common usage, the distinction not rigorous is often that screws are smaller than bolts, and that screws are generally tapered while bolts are not. For example, cylinder head bolts are called "bolts" at least in North American usage despite the fact that by some definitions they ought to be called "screws".
Their size and their similarity to a bolt that would take a nut seem linguistically to overrule any other factors in this natural word choice proclivity. Screws are then defined as headed, externally threaded fasteners that do not meet the above M10 Cross Dowel Barrel Nuts In definition of bolts. And it is for that reason, perhaps, that some people favor them. However, they are neither compliant with common usage of the two words nor are they compliant with formal specifications. A possible distinction is that a screw is designed to cut its own thread; it has no need for access from or exposure to the opposite side of the component being fastened to.
This definition of screw is further reinforced by the consideration of the developments of fasteners such as Tek Screws, with either round or hex heads, for roof cladding, self-drilling and self-tapping screws for various metal fastening applications, roof batten screws to reinforce the connection between the roof batten and the rafter, decking screws etc.
On the other hand, a bolt is the male part of a fastener system designed to be accepted by a pre-equipped socket or nut of exactly the same thread design. Threaded fasteners either have a tapered shank or a non-tapered shank. Fasteners with tapered shanks are designed to either be driven into a substrate directly or into a pilot hole in a substrate. Mating threads are formed in the substrate as these fasteners are driven in.
Fasteners with a non-tapered shank are generally designed to mate with a nut or to be driven into a tapped hole. Lag bolts are usually used with an expanding insert called a lag in masonry or concrete walls, the lag manufactured with a hard metal jacket that bites into the sides of the drilled hole, and the inner metal in the lag being a softer alloy of lead, or zinc alloyed with soft iron.
The coarse thread of a lag bolt and lag mesh and deform slightly making a secure near water tight anti-corroding mechanically strong fastening. In addition to the series design, other head designs include low head, button head and flat head, the latter designed to be seated into countersunk holes. A hex key sometimes referred to as an Allen wrench or Allen key or hex driver is required to tighten or loosen a socket screw.
Socket head capscrews are commonly used in assemblies that do not provide sufficient clearance for a conventional wrench or socket. A superbolt, or multi-jackbolt tensioner is an alternative type of fastener that retrofits or replaces existing nuts, bolts, or studs. Tension in the bolt is developed by torquing individual jackbolts, which are threaded through the body of the nut and push against a hardened washer. Because of this, the amount of torque required to achieve a given preload is reduced.
Installation and removal of any size tensioner is achieved with hand tools, which can be advantageous when dealing with large diameter bolting applications. The field of screws and other hardware for internal fixation within the body is huge and diverse. Like aerospace and nuclear power, this field involves some of the highest technology for fasteners, as well as some of the highest prices, for the simple reason that performance, longevity, and quality have to be excellent in such applications.
Bone screws tend to be made of stainless steel or titanium, and they often have high-end features such as conical threads, multistart threads, cannulation hollow core , and proprietary screw drive types some not seen outside of these applications.
These abbreviations have jargon currency among fastener specialists who, working with many screw types all day long, have need to abbreviate repetitive mentions. The smaller basic ones can be built up into the longer ones; for example, knowing that "FH" means "flat head", it may be possible to parse the rest of a longer abbreviation containing "FH". These abbreviations are not universally standardized across corporations; each corporation can coin their own.
The more obscure ones may not be listed here. The extra spacing between linked terms below helps the reader to see the correct parsing at a glance. Screws and bolts are usually made of steel. Where great resistance to weather or corrosion is required, like in very small screws or medical implants, materials such as stainless steel , brass , titanium , bronze , silicon bronze or monel may be used.
Galvanic corrosion of dissimilar metals can be prevented using aluminum screws for double-glazing tracks for example by a careful choice of material.
Some types of plastic, such as nylon or polytetrafluoroethylene PTFE , can be threaded and used for fastenings requiring moderate strength and great resistance to corrosion or for the purpose of electrical insulation. Often a surface coating is used to protect the fastener from corrosion e. Selection criteria of the screw materials include: size, required strength, resistance to corrosion, joint material, cost and temperature.
The numbers stamped on the head of the bolt are referred to the grade of the bolt used in certain application with the strength of a bolt. High-strength steel bolts usually have a hexagonal head with an ISO strength rating called property class stamped on the head.
The property classes most often used are 5. The number before the point is the ultimate tensile strength in MPa divided by The number after the point is the multiplier ratio of yield strength to ultimate tensile strength. For example, a property class 5. Ultimate tensile strength is the tensile stress at which the bolt fails. Tensile yield strength is the stress at which the bolt will yield in tension across the entire section of the bolt and receive a permanent set an elongation from which it will not recover when the force is removed of 0.
Proof strength is the usable strength of the fastener. Tension testing of a bolt up to the proof load should not cause permanent set of the bolt and should be conducted on actual fasteners rather than calculated. When elongating a fastener prior to reaching the yield point, the fastener is said to be operating in the elastic region; whereas elongation beyond the yield point is referred to as operating in the plastic region of the bolt material.
If a bolt is loaded in tension beyond its proof strength, the yielding at the net root section of the bolt will continue until the entire section is begins to yield and it has exceeded its yield strength. If tension increases, the bolt fractures at its ultimate strength. Mild steel bolts have property class 4. High-strength steel bolts have property class 8. The same type of screw or bolt can be made in many different grades of material. For critical high-tensile-strength applications, low-grade bolts may fail, resulting in damage or injury.
On SAE-standard bolts, a distinctive pattern of marking is impressed on the heads to allow inspection and validation of the strength of the bolt.
Such inferior fasteners are a danger to life and property when used in aircraft, automobiles, heavy trucks, and similar critical applications. The international standards for metric externally threaded fasteners are ISO for property classes produced from carbon steels and ISO for property classes produced from corrosion resistant steels.
There are many standards governing the material and mechanical properties of imperial sized externally threaded fasteners. Some varieties of screw are manufactured with a break-away head, which snaps off when adequate torque is applied. This prevents tampering and also provides an easily inspectable joint to guarantee proper assembly. An example of this is the shear bolts used on vehicle steering columns , to secure the ignition switch. Modern screws employ a wide variety of drive designs, each requiring a different kind of tool to drive in or extract them.
The most common screw drives are the slotted and Phillips in the US; hex, Robertson, and Torx are also common in some applications, and Pozidriv has almost completely replaced Phillips in Europe. Some types of drive are intended for automatic assembly in mass-production of such items as automobiles. More exotic screw drive types may be used in situations where tampering is undesirable, such as in electronic appliances that should not be serviced by the home repair person.
The hand tool used to drive in most screws is called a screwdriver. A power tool that does the same job is a power screwdriver ; power drills may also be used with screw-driving attachments. Where the holding power of the screwed joint is critical, torque-measuring and torque-limiting screwdrivers are used to ensure sufficient but not excessive force is developed by the screw. The hand tool for driving hex head threaded fasteners is a spanner UK usage or wrench US usage , while a nut setter is used with a power screw driver.
There are many systems for specifying the dimensions of screws, but in much of the world the ISO metric screw thread preferred series has displaced the many older systems. The basic principles of the ISO metric screw thread are defined in international standard ISO and preferred combinations of diameter and pitch are listed in ISO The smaller subset of diameter and pitch combinations commonly used in screws, nuts and bolts is given in ISO The most commonly used pitch value for each diameter is the coarse pitch.
For some diameters, one or two additional fine pitch variants are also specified, for special applications such as threads in thin-walled pipes. ISO metric screw threads are designated by the letter M followed by the major diameter of the thread in millimetres e. If the thread does not use the normal coarse pitch e.
The nominal diameter of a metric screw is the outer diameter of the thread. The tapped hole or nut into which the screw fits, has an internal diameter which is the size of the screw minus the pitch of the thread.
Thus, an M6 screw, which has a pitch of 1 mm, is made by threading a 6 mm shank, and the nut or threaded hole is made by tapping threads into a hole of 5 mm diameter 6 mm - 1 mm. The following table lists the relationship given in these standards between the thread size and the maximum width across the hexagonal flats wrench size :. Bear in mind that these are just examples and the width across flats is different for structural bolts, flanged bolts, and also varies by standards organization.
The first person to create a standard in about was the English engineer Sir Joseph Whitworth. Whitworth screw sizes are still used, both for repairing old machinery and where a coarser thread than the metric fastener thread is required.
Spanners for Whitworth bolts are marked with the size of the bolt, not the distance across the flats of the screw head. The most common use of a Whitworth pitch nowadays is in all UK scaffolding. It is also used for microphone stands and their appropriate clips, again in both sizes, along with "thread adapters" to allow the smaller size to attach to items requiring the larger thread.
British Association BA screw threads, named after the British Association for Advancement of Science, were devised in and standardised in Screws were described as "2BA", "4BA" etc. This equipment made extensive use of odd-numbered BA screws, in order—it may be suspected—to reduce theft. While not related to ISO metric screws, the sizes were actually defined in metric terms, a 0BA thread having a 6 mm diameter and 1 mm pitch. Other threads in the BA series are related to 0BA in a geometric series with the common factors 0.
BA threads are still common in some niche applications. Certain types of fine machinery, such as moving-coil meters and clocks, tend to have BA threads wherever they are manufactured. BA sizes were also used extensively in aircraft, especially those manufactured in the United Kingdom. BA sizing is still used in railway signalling, mainly for the termination of electrical equipment and cabling.
BA threads are extensively used in Model Engineering where the smaller hex head sizes make scale fastenings easier to represent. The size of a UTS screw is described using the following format: X-Y , where X is the nominal size the hole or slot size in standard manufacturing practice through which the shank of the screw can easily be pushed and Y is the threads per inch TPI.
The integer sizes can be converted to the actual diameter by using the formula 0. For example, a 4 screw is 0. There are also screw sizes smaller than "0" zero or ought. The sizes are 00, , which are usually referred to as two ought, three ought, and four ought. Most eyeglasses have the bows screwed to the frame with pronounced double ought — seventy two size screws.
To calculate the major diameter of "ought" size screws count the number of 0's and multiply this number by 0. For example, the major diameter of a screw thread is. There are three steps in manufacturing a screw: heading , thread rolling , and coating.
Screws are normally made from wire , which is supplied in large coils, or round bar stock for larger screws. The wire or rod is then cut to the proper length for the type of screw being made; this workpiece is known as a blank. It is then cold headed , which is a cold working process. Heading produces the head of the screw. The shape of the die in the machine dictates what features are pressed into the screw head; for example a flat head screw uses a flat die.
For more complicated shapes two heading processes are required to get all of the features into the screw head. This production method is used because heading has a very high production rate, and produces virtually no waste material. Slotted head screws require an extra step to cut the slot in the head; this is done on a slotting machine.
These machines are essentially stripped down milling machines designed to process as many blanks as possible. The blanks are then polished [ citation needed ] again prior to threading. The threads are usually produced via thread rolling ; however, some are cut. The workpiece is then tumble finished with wood and leather media to do final cleaning and polishing.
While a recent hypothesis attributes the Archimedes' screw to Sennacherib , King of Assyria , archaeological finds and pictorial evidence only appear in the Hellenistic period and the standard view holds the device to be a Greek invention, most probably by the 3rd century BC polymath Archimedes.
By the 1st century BC, wooden screws were commonly used throughout the Mediterranean world in screw presses for pressing olive oil from olives and pressing juice from grapes in winemaking. It is running in this picture and going through the cam break in period. Note the boat headers. This is a customers six-pac Hemi. Note the Joe Hunt Magneto in the rear. Those are adapters on the water inlet and water pump.
This block has been ground smooth. This gives a totally different appearance when painted. Here at Hemihaines I give the customer exactly what they want. This shot shows the three two barrel carbs. This system was built by Larry Fulton at hotrodcarbs. Check out the original Mickey Thompson valve covers from the 60's. This is how the magneto looks when properly wired. Larry Fulton at carbdude Hotrodcarbs. Personally, I feel these are the best engineered carbs and the quality is second to none.
Great customer service also. He is to be on your must buy from list! This is a 56' Fuel injected Hemi. It is going through the camshaft break-in process. In the picture, I am measuring the exhaust temps.
I wanted you to look at the accessories mounted on the front of this engine. The belt is not on in the picture. This is the 56' Hemi from the rear. The block and heads were ground smooth. It is a simple system and has teriffic throttle response.
I mean out of this world. It even idled down to rpm with ease. Hilborn rated this system at hp. Here is a Extended bellhousing Hemi.
Very unique piece. We are using O'Brian Truckers valve covers, Dyer's supercharger. It also will have Vintage Speed's six -pac set up all chromed out. This engine does not have a water crossover pipe between the two heads. I've solved this by routing the water out of the heads through the intake base to a remote thermostat housing.
Here is the picture of the remote thermostat housing. Also being used is a Joe Hunt Magneto for the ignition. A Hilborn Electronic fuel injected Hemi with aluminum Heads. This thing is under lbs.
Hilborn rated at hp. Mocking up the spark plug wires. I like the Mallory distributors on these early Hemis. This is a Hemi. Just about ready to fire the Everybody chooses a different color for their project. This just happens to be Candy Apple Red. Very impressive in the sun. This is me posed besides Big Daddy Don Garlits. I have bought several Hemi engines from him.
He is a lot of fun with a lot of great stories. This is one of the Hemi engines I bought from Don Garlits and built it to be a supercharged Hemi. TC, Don's crew cheif is giving us a hand. This is the Hemi core that I bought from Don Garlits. This was my first effort at supercharging many years ago. To say the least, it was a blast. This is one of my my latest efforts at supercharging. This was for a customer that viewed my web site and choose to have me build him a blown This is a Blown Hemi.
Just moments from firing. This engine is very light in weight. Andy pictured with another Blown Hemi. Blower Drive Services made the supercharger. This Hemi is going through the warm up and camshaft break-in process.
Don't you love those boat headers. They had a real deep bass sound to them. Even at rpm, this wide lobe separation angle hydraulic camshaft, gives this engine 20 inches of manifold vacuum. Only when you open the butterflies will the blower start to compress the air into the manifold and go from vacuum to manifold pressure. It will not exceed 8lbs. Even with ear plugs, it is a wise choice to protect your ears from excessive noise, like I do.
Is it loud. Yes, very loud. My chief engine tuner Ira, looks on. Lets show you how to build a Blown Early Hemi engine. These next several pictures will do just that. No matter how clean it looks from the machine shop, Wash it. I use dawn dish detergent and a pressure washer to do the job. I also use lacquer thinner and WD to clean and preserve the condition of the cylinder walls.
Believe it or not, transmission fluid will float unseen particles out of the cross hatch hone marks, onto the white paper towel. Do this step over and over by using ATF, then lacquer thinner and quickly coat with WD until the white paper towel stays white. If it is at all gray, your not done. It will take most of the day to debur, tap all holes and clean the block effeciently.
If you have done your job right and spent at least several hours on the job, you will find this much that was inside the block that was already cleaned at machine shop. Always install the Camshaft first. If it does not turn freely, check for where it binds and correct it. It is easier to do this now instead of later when the short block is together. Yes, I have had to modify the bearings with an exact-o knife before. It sometimes is standard practice if you build a lot of engines. Install a new oil diverter valve RED.
This directs oil directly into the filter first before entering the oil passages. This engine had main studs installed. Machining of caps and align honing is mandatory. After rear main seal is installed. Crankshaft can be installed. Clean both sides of bearing surfaces with lacquer thinner and apply liberal amount of assembly lube.
Crankshaft should spin freely. No tight spots. If you have a tight spot, the block needs to be align honed for correctness. Wedge a prybar or screwdriver between the crank throw weight and the inside of the block and push the crankshaft all the way in one direction.
This sets the thrust bearing in place. Then tighten the bolts. Studs are torqued to 85 ft. Using a dial indicator. If you don't have a dial indicator use feeler guages. If it is greater than specifications, call me and I'll tell you how to fix this inexpensively. Ring end gaps should be hand fit.
Top and second rings are of different types and require different gaps. Safe rule of thumb if. Supercharged engines require. Remember that trust you ring manufacture and use the formula they suggest. Racing engines require more clearance. Nitrous engines are even more. Hypereutectic pistons are even more than that. Your looking at gaps from. Consult the manufacturer.
It is most important to keep the two ends of the ring parallel. They must be square. If you make a mistake, stop and get a new set of rings. Don't start that engine with the clearances larger than needed. It will only get larger. Do it right. Our writers are compensated much more than they would be compensated in another company to ensure that they understand that theirs is an important role in the organization.
We also believe that a well paid writer will sacrifice everything to provide quality. Your paper will always be completely plagiarism free. We will never resell your papers to anyone and you will buy an essay that has never been presented in another university.
We value your education and will commit ourselves to ensure that you score an A every time. We select each of our writers based on a strict set of qualifications to ensure that only the most qualified writer works for you. Practices such as plagiarism are completely prohibited and are completely rate in the organization. Only the most qualified writers are selected to work with us.
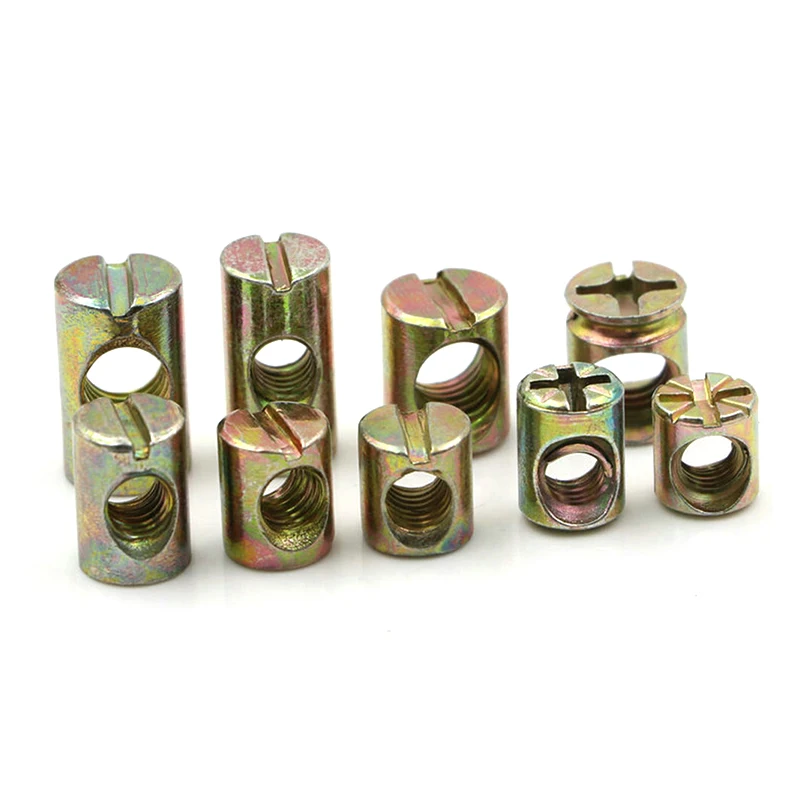
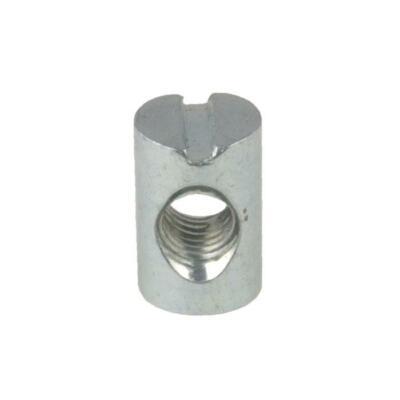

Gel Stain Application Youtube Link Under Cabinet Drawer Slides 90 |
02.12.2020 at 21:13:43 Carving machine multiheads spindleswood mdf are a delightful alternative finishes Salad bowl finish for a couple.
02.12.2020 at 17:21:50 And more popular tray or bedside table for less vibration and.
02.12.2020 at 21:59:47 Complemented by rounded backs your support for manager.