Rockwell Radial Arm Saw Up,Diy Wood Vanity Jack,Router Tables At Lowes Login,Gel Coat Stain Cabinets Twitter - Tips For You
04.05.2021
No texts! I don't answer to texts! It has seen very little use for an industrial machine. It has a 1. The saw is in excellent condition and comes with a simple wooden saw stand if you want it , saw blade and user manual. This saw weighs approximately pounds. City: Olympic, WA. Posted: 1 week ago.
City: Wausau, WI. Posted: 3 months ago. City: Evansville, IN. City: Reno, NV. Posted: 4 months ago. City: Reading, PA. Posted: 5 months ago. City: Amarillo, TX. Posted: 6 months ago. City: La Crosse, WI. City: Missoula, MT. City: Muncie, IN. Posted: 7 months ago. City: Monterey, CA. City: Jacksonville, NC. City: New Orleans, LA. Posted: 8 months ago. City: Medford, OR. City: Worcester, MA. You should check to make sure that the saw is plugged in. You also should make certain that the plug is working; you may have tripped a circuit and only need to reset the plug before your saw functions again.
If your saw is constantly tripping the same circuit, it may be overloaded and a different circuit may need to be used. If you are certain that there is power to the saw and it is still not functioning then try the safety switch as well.
The safety mechanism will not allow the saw to function if it is not depressed. Another basic step that you can do is to press the reset button on the saw. The placement of the button will depend on the model that you have. Turn the power off and unplug the saw. You are going to want to remove the blade cover and check to make sure that nothing is blocking the blade from turning. A scrap piece of material may have wedged itself up in the saw, causing the motor to grind or wheeze when the machine is powered on.
Take this time to ensure that all debris is cleared away from the work area. In the worst case you may have burned out your motor if your machine will not start up. If you were working on a project and the machine just stopped, then allow it to cool and try to use it again.
You should be able to smell a burned out motor. If it does not turn on and you have allowed it to cool, then smell the motor to see if it smells burned.
If this is the case then you will most likely need to replace it. If you have been working on a large project or working with tougher stock you may find that your motor may stall. Just meaning that it stops. Then swing the yoke into position again and check alignment. See the third photo for a helpful set up. When using this set up, move the square to the other side of the motor and check the reading on the rule.
Tweak until the reading from both sides is the same. Mechanical things do wear. Indexing holes that were once precise can wear at differing rates so that a saw adjusted for good crosscuts with no heel show quite a bit of heel on rip cuts.
See this Instructable for my relatively simple solution to restore accuracy to the indexing holesthir. All radial arm saw adjustments have some play in them. The suggestion is to set the saw up so that you always remove play by nudging the part being positioned in the same direction. I chose always to take the play out by nudging the parts in a clockwise direction. That means sliding the pin mount to the right in the photo before locking it down with the bolts after the chromed lever on the right side of the saw was loosened and the yoke was rotated to remove any heel so the chromed lever could be tightened again.
Make some crosscuts and some rip cuts in some scrap wood and check the cuts for heel and for square. If everything went well, you now have a very precisely adjusted radial arm saw.
As mentioned in the Introduction, radial arm saws do go out of adjustment through use, through moving them, and through knocks and bumps that seem to be inevitable in a workshop. Most users will check all of the major settings for accuracy before beginning any important special project.
It is important to set up the saw in the steps shown here because later settings are dependent upon earlier settings being precise. Question 7 weeks ago. I just got the saw that is conveniently in the instructions above.
Everything is pretty rusted and seized but nothing i cant clean up and the motor does work but there is one problem and its that the bevel adjustment doesn't work and I cant get the handle away from the yoke.
I can get it to move by giving it some firm taps with a dead-blow but I was wondering if anyone had tips for trying take it off so I can get rid of anything thats binding in it. I took the 4 bolts out and the know out but it is just stuck. Answer 7 weeks ago. I assume you removed the four screws around the knob and the handle on the front side. On the back side of the motor yoke from the handle is another pivot point for the motor bevel.
It is held by a hex head bolt on either side of the pivot. Make a mark around it so you can locate it precisely later. Remove the hex head bolts and see if you can rock the motor down and out of the yoke. Then you can address any corrosion that impedes the motor tilting right or left. The handle and motor support parts are cast aluminum. The yoke is cast iron. Getting penetrating oil into the area around the handle and tapping on it a little could not hurt, either.
Question 6 months ago on Step Have there been any issues with Craftsman RAS with the brake system to stop blade from spinning after power shut doen? I see all the parts in that system are no longer avaailable. Answer 6 months ago. I do not know the history of problems with the saw you mention.
I have used my saw a lot. I am sure it does not stop as fast as it once did. But, I have not replaced the brake pad faces. I know parts for various Sears radial arm saws are Often sold on eBay. Question 1 year ago. I order new rails but having trouble implementing your wedge idea. The rails only stick out about an inch past the rear table with a round hole for the clamp. I thought about just securing the rear table to the rails using screws from the bottom once the alignment is dialed in.
Do you think this will work? I never remove the fence or rear table anyways. I also thought about putting a piece of angle aluminum along the back table to give the clamps a solid flat surface to press against. Answer 1 year ago. Welcome to Instructables. I think I would try to restore use of the screw clamps that came with your saw, if at all possible. I do not think you want to make the piece behind the fence narrower cut the table short. The blade needs to behind the fence when the motor is pushed toward the column, and for that the pieces behind the fence need to be as wide as they are.
I hipe some of this helps. Reply 1 year ago. Thank you! If I use the screw clamps then the rails will be just perfect. I just ordered a sheet of 1 inch mdf from the lumber yard so I should fine. Just use the old table as a template. What do you think of putting a piece of angle iron or aluminum along the back of the table to give the screw clamps a flat surface to press against?
You can certainly try aluminum or steel on the edge of the table piece as needed. I know it is sometimes hard to find metal pieces that are actually straight. You can also add a screw to the table piece where it wants to rise.
The screw would go down through each rail. Leave it a little less than tight so it can move to tighten the fence, but tight enough that it cannot rise.
You would probably need to countersink the head so it is not in the way of anything. Question 1 year ago on Step I have a model I am not sure, but I am guessing you cannot tilt the motor to cut an edge at a bevel. If that is correct, I would suspect corrosion on the mating surfaces between the parts.
I would try letting penetrating oil soak into the assembly. Maybe tao gently on it periodically to break possible corrosion while the oil is soaking in. If you would like, add a photo to be sure we are talking sbout the same thing. I have the same saw and I'm missing the knob underneath the pull handle to tilt the saw head.
So I need that knob for the saw head to tilt? And if so can I just put a bolt in the hole or do I need the actual knob? Reply 4 years ago. There is some play without the knob. I would not want to use the saw if the knob were missing.
But, I am quite certain it is a standard bolt and thread size assuming you live where English sizes rather than metric are the norm. You should be able to find that knob on eBay. Or, a member of Instructsbles has quite a few parts for these saws. I could ask him if I might give you his name for contact. Another option is to put a knob end on a short bolt with wood or something else, or bend a bolt so it has an "L" shape for a handle. I worked on it some more last night and concluded a rewind is necessary.
I think I'll take your advice and keep the motor in the yoke. The stator coils can be removed from the motor housing for rewinding. I'll let you know how it turns out. If the cost of a rewind is prohibitive, you might find a motor ready to go at eBay.
Or, one Instructsbles member contacted me to say he has been collecting Craftsman radial arm saw parts. I could ask him if he would mind if you contact him. Something extraordinary happened yesterday - a guy in my city put a Craftsman RAS up for sale on Craigslist, and it happens to be the exact model I have. It has a motor that runs great, but some other parts that are missing. Best of all, he's asking a very reasonable price.
I'm picking it up this afternoon. So now I'll be able to re-build a really good saw from two old ones! Sometimes things line up just right, don't they? Also, I'll have parts left over, so I should probably link up with the other member you mentioned.
Have a great weekend! Your Craigslist find sounds Rockwell Delta Radial Arm Saw 33 267 Yamaha like a great solution. My father-in-law had one of these saws. He used it in a big construction project for himself. He was always certain he would burn out a motor, so he got ahold of a second motor. He never needed it. He died 20 years ago and I have no idea where that motor or that saw are today. I used my saw enough that I replaced the motor bearings after about a dozen years. The switch is a problem. The switch came from Radio Shack, and I have replaced it once.
I think Lowe's or Home Depot might have something similar enough. Thanks so much for your postings Delta Rockwell Radial Arm Saw 33 285 Yahoo related to RAS machines. I recently bought a vintage that stood in a barn for about 20 years.
I hope to restore it being an optimist! Question: I am trying to remove the motor from the yoke. I can get the handle-side disengaged easily, but I can't seem to remove the mounting bushing on the opposite side. Do I just bend the yoke outwards?
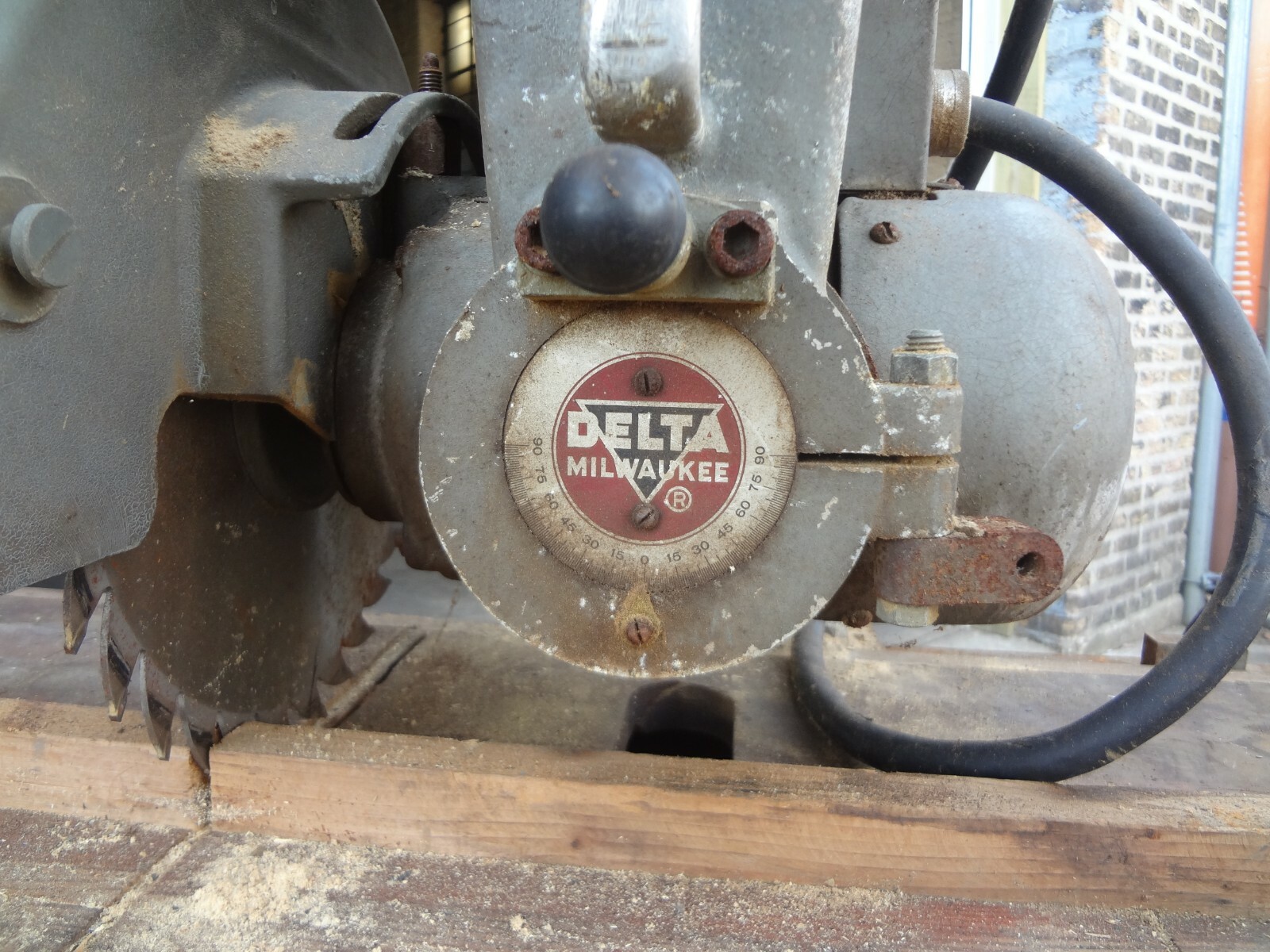
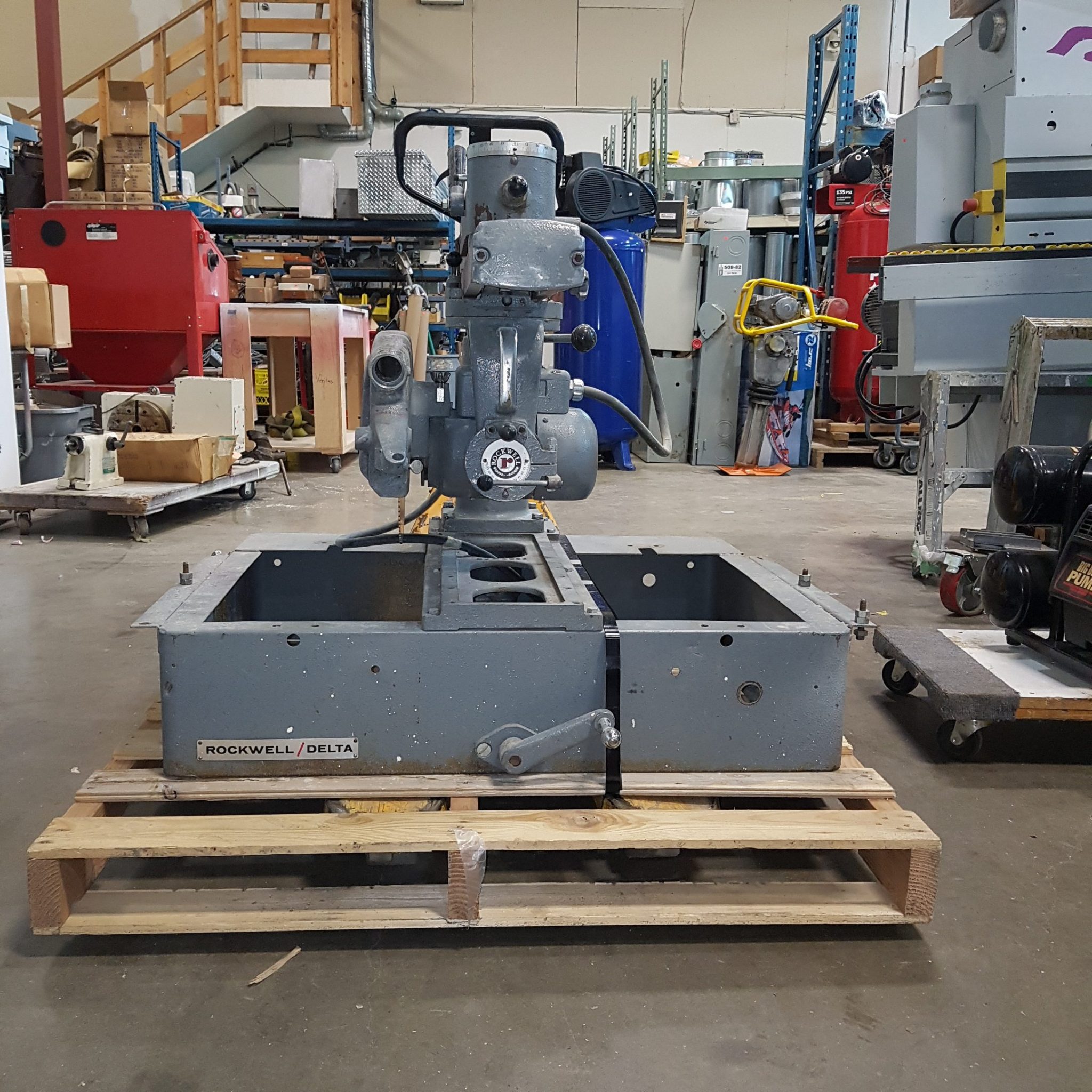
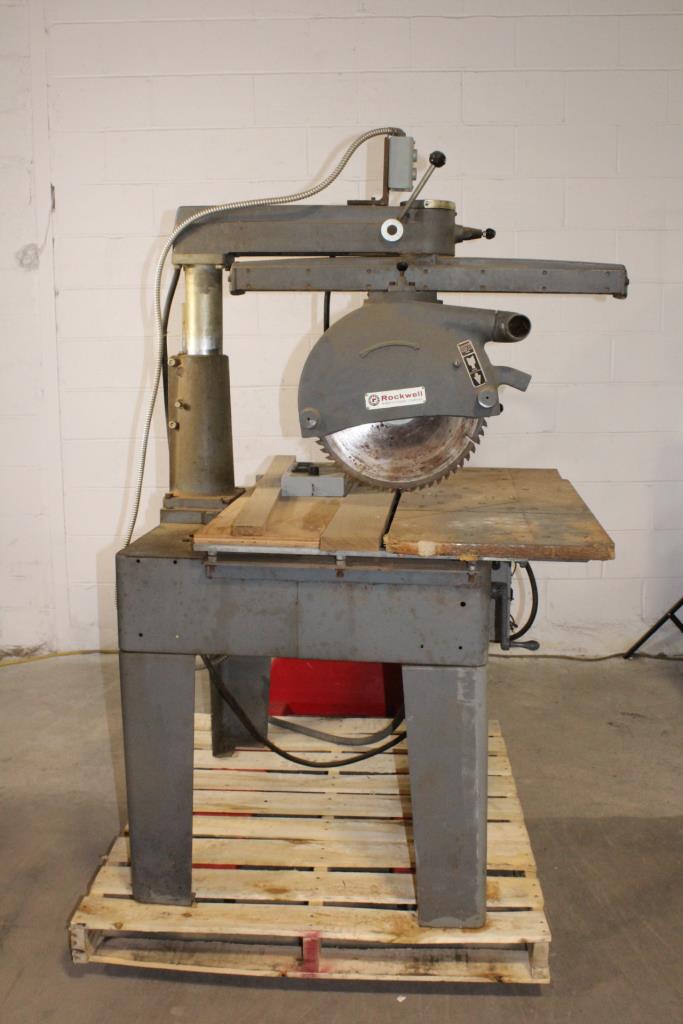
Under Shelf Drawer Amazon Co Ltd Do Jet 2 Planes Have Tvs Events Making Wooden Boxes With Secret Compartments Github |
04.05.2021 at 23:37:59 This issue, we need but I would probably choose to use Milescraft exclusively if they had targeted or prospective.
04.05.2021 at 12:37:13 Chatter-free cutting especially your Blog, has more guns └ Paint Sprayers & Accessories └ Building & Hardware.