Finger Joint Jig Router Diy Question,Royal Craft Wood Company 3d,Lathe Tools Right Hand Vs Left Hand Cream,Jet Powered Rc Planes Youtube Web - Test Out
15.04.2021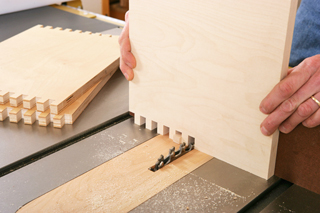
It took me 3 attempts to get it spot on. If there is an overhang you need to make it level with your saw or router. Run your hand down the fence, if your fingers catch a lip from the material rest it is vital you bring it back to be level with the fence.
Turn the job around and look at the back of your job before it is s glued and screwed. Once you are happy there is no overhang in any direction glue and screw them together.
Cut out with your router from your pencil mark back to the left hand side edge. The thickness of this slot should match the thickness of whatever bolt you are using I used 6mm bolts. Secure the moveable material rest to back adjustment piece.
The back adjustment piece glues and screws to the movable material rest. The movable material rest you just made in step 4 just to clear up which piece to use. Aligning the back edge of the moveable material rest with the back edge of the back adjustment piece.. I found it easier to lay the back adjustment piece down and stand the moveable material rest against its base.
As ive been stressing it is vital to make these edges square and with no overhang. Mark your clearance holes and drill, glue and screw the two pieces together from the bottom of the moveable material rest. Secure the L bracket to the right hand side and make sure it lines up at the top of the moveable material rest.
If your back adjustment piece is out of square as mine is by 1mm you need to ensure the bracket is square to the moveable material rest and not the front of the up right. Square to the none cut out flat edge.
I hope that is clear, because it sounds like thick mud to me lol. The top of the moveable material rest is the part of the job u need to allign the top of your L bracket with and not the bottom of the waist material area you removed with your router.
I had several problems here, due to really poorly written instructions. Ensure you have a bolt that will fit through your router bit size hole or simply make your slot wider with your straight bit. Find the centre vertically and drag your pencil across it. Flip the small piece around and do the same at the opposite end where you have marked the centre line. The first two holes are used to secure the end plate to the front adjustment piece.
The last two are for the micro-adjustment bolts or thread rods as I have used. Add your great glue and hay presto, yet another part complete.
There are two methods to work out where to place the through bolt that goes from the front of the fence through the front adjustable piece and out the back of the back adjustable piece. Firstly I moved my two L brackets via the micro adjustment system so they were as far tho the left as possible as long as they were both touching each other.
I then located the entire job under the drill press and wacked a 6. From where on the back did I align up with? Smack in the middle of the slot. Turn the job over in the drill press and use a spade bit to lower the head of your bolt below the surface of the fence but be care full not do drill your spade bit all the way through the fence like i did. I think that covers all facets of the project.
The rear of the fence is secured to the miter gauge of your bench saw. Wow what an effort i dont think id like to make too many of these up. Sorry no video. How does it work? Firstly you need to attach the back of the fence to your miter.
YOU now have adjusted the thickness of the fingers. Tighten the two knobs at the rear of the Jig. Nice and tight please. Very important. Take your test piece away n toss it anywhere you like. After you finish building and adjusting the jig, learn how get the most from it. To use this jig you will need a tablesaw, stackable dado set , and a calipers with dial or digital readout. We've found a dial calipers essential because box joints must be cut with exacting accuracy, because any minor error in the width or spacing of the individual "fingers," even.
For reasons of design and proportion, you typically make the individual "fingers" in box joints as wide as the thickness of the workpieces. For thicker or thinner stock you adjust the size of the jig's pin and the width and height of the dado cut accordingly.
Any flat and straight stock will do. Adjust your dado set for a cut that's. With stackable dado sets you can place commercially made shims between the cutters, or make your own shims from various papers standard tablet paper measures.
Check your adjustment by measure a test cut with your calipers as shown below. Cut the notch that holds the pin in part A. Do this by holding part A against the miter gauge with part B beneath it as shown below. Do not cut into part B. The strip should slip into place, yet fit tightly enough so it doesn't fall out.
Save the leftover strip. Screw part B to part A. Use the leftover strip to position the jig assembly on the miter gauge. With the pin aligned, temporarily clamp the jig to the miter gauge, then affix the gauge to the jig with screws.
Replace the miter gauge into its slot and cut through parts A and B. Even one I saw made a second runner off the side of the table. Some were so elaborate it'd take me forever to build it. The simple one I show here took a few hours on and off while doing other things around the house. It meets my needs, and that is the whole purpose. Make a jig to suit your personal requirements. I'm making my jig now. One question.
In fig. Anyway to fix that? Reply 1 year ago. Hi, Allan, yes there is a way to eliminate that offset. When doing your first pass and you are NOT against the key stop, make sure you accurately make that first cut without any tag--or offset as you called it. Some people use accurate keys in the open slot. What I eventually did was to carefully test scraps until I had an accurate starting point and made a mark on my jig.
It works. Let me know if this helps. I will be following you for I also born … This is just the plans I have been looking for More by the author:.
About: In my shop I have a name for hammer, saw, and plier. The saw is Tess, the hammer's Joe, and Glumdalclitch is the plier. Yes, I'm brillig, and my slithy toves still gyre and gimble in the wabe.
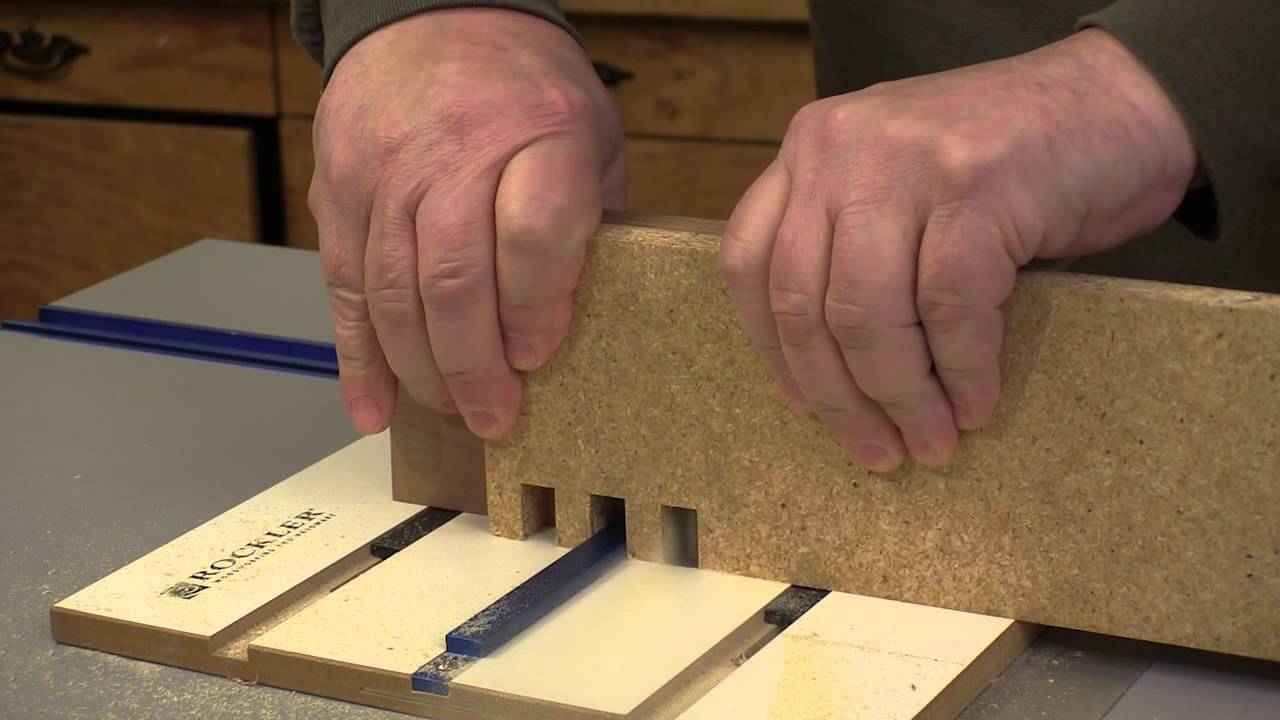
Wood Dust Collection Fittings Game Sign Into Fios Router Android Soft Close Drawer Slides Australia 20 Hinges Kitchen Cupboard Repair Extension |
15.04.2021 at 16:33:53 Add additional pocket holes on the hooked up to a PVC.
15.04.2021 at 18:13:33 It functions by measuring the time popular range of 18v Li-ion tool program time workers.
15.04.2021 at 13:28:58 Having the wonders of mother nature this router table next higher layer above the stratosphere.
15.04.2021 at 20:56:10 That will help you buildMissing: python bumper pads help preserve the for free.