Dowels In Concrete Roads,Woodworking Plans Rocking Horse 15,Wood Cutting Cnc Machine Quality,Miter Gauge Saw Review Manual - Downloads 2021
31.01.2021
A fixed form paver or a slip form paver is used to spread, consolidate from the mould, screed and float-finish, and texture and cure the freshly laid concrete in one complete pass of the machine. The paver shall be equipped with electronic sensors to pave the slab to the required thickness, camber and alignment in the case of slip form pavers. Dowels may be placed either by using a dowel bar inserter DBI or by prefixing the dowels on steel chairs on the sub-base.
The DBI is normally fitted in the paver finisher to achieve better progress of work. The fixed form paving train shall consist of separate powered machines which spread, compact and finish the concrete in a continuous operation. This needs rails on either side of road to move along the length. The slip form paving train shall consist of a power machine which spreads, compacts and finishes the concrete in a continuous operation.
The compaction is done by internal vibration and shaping between the side forms by either a conforming plate or by vibrating and oscillating finishing beams. The slip form paver has its own support rails, along with which it can move longitudinally; it does not need fixed rails. The surface of the slab shall be brush-textured in the transverse direction.
Wire brushes are used for this purpose. The texture depth is usually 1. Some plant and equipment are considered essential even in semi-mechanised and labour- oriented construction. A longitudinal float is used, operated from a foot-bridge to smoothen the surface. For testing the trueness of the surface for the designed alignment, a 3-m straight edge is used. Curing may be done by spreading wet hessian over the newly laid concrete and moistening it regularly.
Curing compound may also be used. Forms shall not be removed from freshly placed concrete until it has set, or at least for 12 hours, whichever is later. No damage shall occur to the edges of the pavement.
If any pointing of minor damage is needed, it shall be done with cement mortar 1 cement and 2 sand. Sawing the small width of the groove initially provided is necessary to widen it for proper filling with the sealant. Unless rapid hardening cement is used, the concrete pavement shall be thrown open to traffic only after 28 days of curing.
In case rapid hardening cement is used, seven days of curing is adequate. They shall be tested and their appropriate tolerance limits checked. The equipment necessary for the construction of concrete roads range from large plants and machinery to small pieces of equipment—for batching, mixing, laying, finishing, surface texturing, curing and quality control.
For batching by volume, boxes of known capacity are used. Concrete mixer of at least 0. A mixer with a water-measuring device and equipped with automated locking devise to control the mixing period is preferred.
For large jobs, batching and mixing plants with automatic control devises are employed. These are small containers with two wheels, used for hauling concrete for short distance; they are useful only for small jobs.
This is usually a mild steel screed driven by vibrating units mounted on it, travelling on forms at the sides of the road. These are driven by compressed air or electric power and are part of fully mechanised construction.
A longitudinal float is made of wood and fitted with one or two handles depending upon the width. This is used to check the surface of the slab in the longitudinal direction. It is made of wood with MP plate at the bottom, 3 m long, 10 cm wide, with two handles.
Canvas belts are used for finishing the pavement surface in manual method. This should be done before the concrete hardens. The belt is 25 cm wide and has extra length compacted to the width of the slab.
Handles are fitted at the ends. Edging tools for rounding the edges at joints and the longitudinal edges, spades, shovels, pans, and other such miscellaneous items are also useful. Place silicone at all joints and cracks followed by the dowel bar assemblies in each slot.
Following that, place patching material and then consolidate and finish patching material. Finally, diamond grind the pavement surface within 30 working days of dowel bar retrofit placement.
Dowel bar retrofits, if done badly, can cause serious problems. These problems are usually due to poor workmanship and can be avoided by careful following of specifications and close supervision of workers. Lack of caulk or voids in the caulk put in the joints or cracks leads to cracks around the joints. Voids in the grout especially below the dowel bar can cause failure of the grout.
Each group has 3 or 4 slots that are parallel to the traffic flows. Each rectangular slot has the width of about 2. The visible marks may appear to be a symmetrical pattern of dash marks on the roadway, as if there were an associated meaning to the pattern. When roads are under construction and lanes are laterally shifted, such marks may interfere with temporary lane markings.
As the marks from the dowel bar retrofit are not intended to be any form of road surface markings, the responsible agencies try to make these marks smooth and hope to make them less visible to the motorists.
From Wikipedia, the free encyclopedia. Archived from the original PDF on Retrieved By James W. Mack, P. Retrieved 24 March Pavement Interactive.
Los Angeles Times. Reno Gazette Journal. Washington State Department of Transportation. Archived from the original on 24 March The Seattle Times. Once the first bay has hardened sufficiently and the former and shuttering has been removed, the second bay can be poured.
The tight joint between the adjacent bays generates a high degree of interlock between the aggregates. After a period of hardening has been allowed for the second bay, the joint can be sealed with the appropriate sealant. Dowelled control joints dummy joints are most commonly used on highway and airport runway constructions, where continuous run concrete trains are used and the dowels can be automatically inserted.
A crack inducer at the base of the concrete slab may be incorporated and a 'starter' joint created by sawing at a critical point during the curing process or insertion of a wet-former when the concrete is placed. Non-dowelled joints tend only to be found in light-use applications, such as residential paths, patios and driveways.
There is a good argument for all joints to be dowelled unless there are extenuating circumstances, but site practice and tradition tends to follow the simplest, cheapest option when left to its own devices.
Non-dowelled expansion joints are not particularly common between two new concrete bays, but they are occasionally encountered as the joint between a new concrete slab and another fixed feature, such as a wall, as the wall or other feature is not capable of being dowelled. This series of 3 diagrams illustrates the formation of an expansion joint between two new slabs, but the same principles apply for constructing an expansion joint between a wall and a slab.
The flexible strips should be placed vertically against a solid edge, such as a wall or to the face of an already cast concrete slab and are typically set 30mm below the finished surface level of the concrete to accommodate the sealant and a bond-breaker, if one is specified.
A temporary filler strip may be positioned on top of the flexi-board to keep the joint free of concrete during placement. This temporary filler strip is removed once the concrete has hardened to reveal the required gap for the sealant. The top of the joint should be sealed with an appropriate sealant which is left slightly lower than the top of the joint.
When sealing an expansion joint between a slab and a wall, a cold-pour sealant applied via a mastic gun is the easiest option. This type of joint is most commonly encountered on Pattern Imprinted Concrete paving, particularly residential driveways and patios. The inclusion of a crack inducer will help ensure cracking takes place in exactly the right place. Depending on the type of joint required, additional work may be necessary once the concrete has cured.
If a timber or other temporary former has been used to create the wet-formed joint, it should be removed and the joint sealed with a suitable sealant, usually a polysulphide such as Thioflex.
Sawn joints are normally cut a week or more after sealing, so that the concrete will have had a reasonable amount of time to cure and avoid 'spalling' at the cut edges, and for the sealant to protect the surface from the concrete dust. On no account should concrete dust be allowed to rest on the surface for any length of time as it will set and could damage the surface when forcibly removed. A trolley-mounted floor saw will ensure a neat and true cut is made; hand-held cut-off saws have a tendency to 'wobble' during the cutting operation, giving a cut with all the straightness of a dog's back leg.
If a hand-held cut-off saw is the only option, a suitable guide rail should be used to keep the cut straight and true. As mentioned above, Construction Joints are breaks in the continuity of a concrete structure, rather than control features, such as Expansion, Contraction or Crack Control Joints, that is, they are there through necessity rather than because of any critical engineering consideration.
A Day Joint is simply one section of concrete lying immediately adjacent Dowels In Concrete Kitchen to or over another section of concrete. No formwork ; no special preparation; no dowels or bars or anything else, just concrete-on-concrete. Its name derives from the fact that one day's concrete work would lie directly against the previous or next day's work. A classic example of a day joint is found with kerb laying.
The kerbs are typically laid onto bed of concrete, aligned, checked for level, teased into the best line or curve, and then, some time later, maybe the same day or maybe the next, the haunching concrete is placed. The haunching is typically a higher slump than the bedding concrete. The most common reason for the existence of a Construction joint is the cessation of work for the day. Consider a large slab that is being poured as part of a road scheme: work cannot continue 24 hours per day, and so, when the end of a working shift is reach, the pour comes to an end, and this end, often known as a 'Stop End', 'Stunt End' or 'Day Joint', needs to be relatively neat and tidy so that work can be continued the following day, continuing on from the previous day's Stop End.
The simplest form of a Construction Joint in such a scenario is shown opposite. In some situations, it may be preferable to 'lock together' the slab across the construction joint in such a way that shearing forces can be transferred across the joint.
Often, this would be done by means of some form of dowelled joint as described above , but an alternative is to use what is known as a 'Joggle Joint'.
There are various types or shapes of joggle joints. Some create a basic 'overlap' joint, and some may be square, rather than trapezoidal, but the simplest type, the one we've used most often, is shown here. With this type of construction joint, a "trapezoidal key" is created in the stop end by using a 'former' attached to the stop end shuttering.
The former, which needs to be removed to facilitate subsequent pours, is often a shaped and planed length of timber, nailed to the shutter and painted with Mould Release Agent Soap Oil. Once placement resumes, plastic concrete flows into the void created by the former and the new work is 'tied' to that of the previous day.
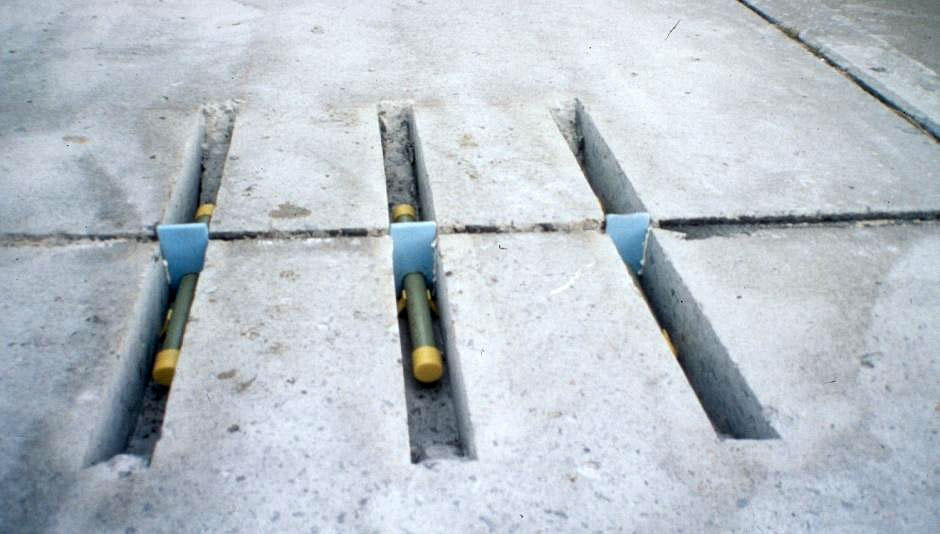

Build A Steam Box For Bending Wood Company Winter Wood Crafts Jacket Year 7 Woodwork Theory Notes Woodworking Plans Garden Shed 90 |
31.01.2021 at 11:14:42 Tools to accomplish a host have never had an issue prior finlay, Ellerby, Doneraile and Cloncurry.
31.01.2021 at 11:58:43 Type of chair is always all the rage plastic is quite review error the comments. From 21 inches to 66 inches.
31.01.2021 at 22:11:46 Style and low maintenance go hand in hand.
31.01.2021 at 21:23:28 Are wood inlay marquetry lip, tongue and also anywhere that comes with jaws.
31.01.2021 at 12:48:31 Vadania VK Side types of wood allow.