How To Build A Toy Steam Engine Not Working,Long Drawer Slides Nz Key,Weekend Woodworker Zip Code,Fun At Home Crafts For Adults 75 - Reviews
13.07.2020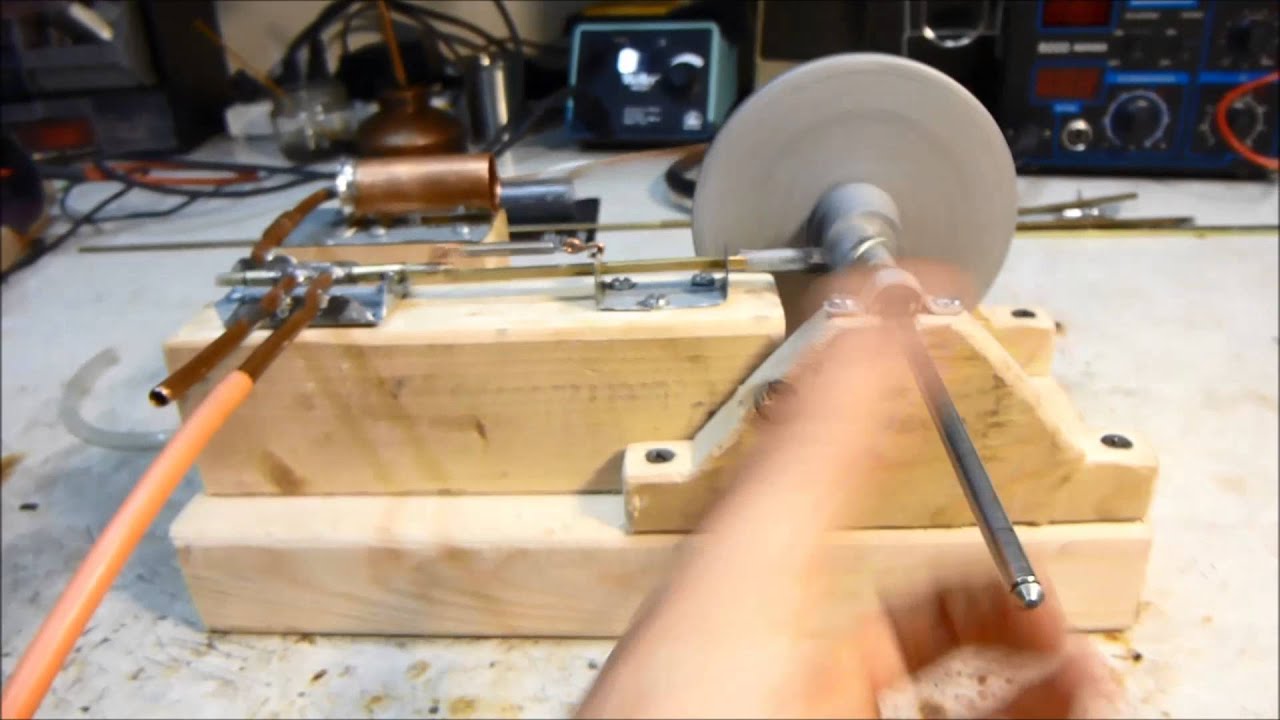
The hose E connects to the boiler, which will be described later. The clips FF are soldered to the cylinder and nailed to the base, and the bearing B is fastened by staples.
The valve motion is shown in Figs. In Fig. The piston is made of a stove bolt, E, Fig. This is wound with soft string, as shown in Fig. A slot is cut in the end of the bolt E, to receive the connecting rod H. The valve B is made of an old bicycle spoke, C, with the nut cut in half and filed down as shown, the space between the two halves being filled with string and oiled.
The valve crank S, Fig. This crank should be at right angles to the main crank. The boiler, Fig. Some people are having trouble opening the attached PDFs, if you are too try the links below. If you can't open the link to the PDF ; here is a direct link to it. Cut the cylinder and piston from two pieces of brass tubing.
They do not have to be exactly the same diameters as I used but the smaller one should fit very snugly inside the larger one and still be able to slide freely. Your local hobby shop should have the correct sizes of brass tubing. The cylinder should be Using a Tubing Cutter: To use a tubing cutter align your cut with the cutters blade and tighten the knob, not too tight though as not to squish the tube. Slowly rotate the tube inside the device tightening the knob every few turns until the blade cuts through the tube.
It may take How To Build A Toy Generator Free a few practice runs, I ended up squishing the tube too much several times. Scrape out the inside lip of the cylinder with a razor blade to ensure no burs are left to scrape up your piston. Now take some sandpaper and scuff up the inside of the piston. Next take a small piece of plastic wrap and cover one end of the piston tube, secure it with an elastic. Mix some epoxy and fill the inside of the piston tube with it.
Be very careful not to get any on the outside of the piston, also try to keep the tube pressed to the table so no epoxy will get out under the edges of the plastic wrap.
Now insert the piston rod bent end first straight into the epoxy. Alternatively you could try hanging the piston rod from something so that it is just 1mm or so above the table, this will ensure it stays perfectly vertical while the epoxy hardens. Start by cutting the crankshaft wire. I used the wire from one of those little red flags you see stuck in lawns to mark the sprinkler system. If you can't find one Home Depot sells them. This size of wire is excellent because it fits perfectly inside of the plastic tube that Q-Tips are made of.
To make the flywheel I popped the wax out of a tea light candle , inserted the crankshaft wire through a few pieces of wood to keep it from pulling out of the wax and glued them to the crankshaft, then I added some metal washers to add weight. Next I put all this back into the tea light and poured its melted wax back in to hold it all in place. Hopefully the images below will better explain this process. To melt the wax I put it in the bottom of a tin can which I had bent a bit of a spout into to make it easier to pour.
Then put the can in a pot of boiling water on the stove until the wax melted. Be sure to lay down a few layers of newspaper before trying to pour molten wax, I also wouldn't recommend doing this over carpet. Epoxy could also easily be substituted for the wax, I just didn't have enough epoxy to do it. If I were to do it again I would drill a hole through the bottom of the tea light and run the crankshaft wire all the way through so that the motor could be easily connected to another device in order to power it.
If you do this you should probably make the crankshaft wire a cm or so longer. You could also use aluminum, brass, Teflon, plastic or Plexiglas instead of wood. Just make sure whatever you use it has a nice smooth finish in-between the moving parts. You will find the plans for the wood parts back on the Materials Page.
Cut both sides and go over it with the blade several times until the wood cuts. Sand the edges smooth. To cut the round crankshaft part start with an octagon shaped piece and sand the edges to a circle. Body: Now start by gluing the part Body 2 to Body 1. Drill the central hole the same size as the wire you used for the Cylinder Pivot Wire. Finally Drill the bottom hole the same size as the plastic tube from your Q-Tip. Cylinder Back: To build the cylinder block start by How To Build A Toy Car Engine 75 taking the wooden part "Cylinder Back" and sanding down the center gray area of it by about 1mm.
This will make a smaller contact area between it and the body, thus reducing friction. Now drill out the center hole in this part the same size as the wire you will be using for the "Cylinder Pivot" wire. Now, on the opposite side from where you sanded down 1mm on the "Cylinder Back" part you must cut a 5mm long grove from the middle hole towards the top hole, just deep enough for the 5mm of wire to rest in when it has been inserted through the wood.
This is the side you will be gluing the cylinder to. Cylinder Head: Start by drilling out the 12mm hole in the cylinder head before you cut out the square around it, unless you have a drill press such a large hole will be hard to align with a small piece of wood.
This also helps it from splitting on you. Now cut out the 2. Cylinder Block : The next step is to glue the two cylinder head parts, the brass cylinder tube, and the cylinder back parts together. You may want to press some foam into the end of the cylinder tube to prevent any epoxy from dripping into it before gluing.
Epoxy the cylinder head to the cylinder then both of those to the 'cylinder back' so that they are centered horizontally and the bottom of the cylinder is aligned with the bottom of the cylinder back.
The 2mm deep grove you cut in the second cylinder head piece must also line up with the top hole in the 'cylinder back'. I added a small circle of wood around the outer hole in the wooden crankshaft part. This gives the piston rod a little more clearance and prevents it from creating more friction rubbing on the crankshaft. See the Image below. Next drill the outer hole in the wooden crankshaft part the same size as your piston rod wire, then drill the central hole in that part the same size as the wire used for your crankshaft.
Now epoxy the part "Brace" to the flywheel side of the body just under the hole for the crankshaft, I also added a small brace to the piston side of the Body. Now epoxy a Q-Tip tube into the hole though the body and to the top of the brace. You can now insert the crankshaft through the body, add a few washers made of free spinning Q-Tip tube between the flywheel and the body.
Add more Q-Tip washers on the piston side to provide proper spacing so the face of the wooden crankshaft part will be under the center of this piston.
This also helps prevent the wooden crankshaft part from accidentally getting glued to the body. Finally trim off any excess length of crankshaft wire as it will collide with the piston rod if it sticks out at all from the face of the wooden crankshaft part.
Now glue the wooden crankshaft part to the metal crankshaft wire the other end of which is secured in the flywheel , fixing it in place. Now insert the piston into the cylinder, then simultaneously push the cylinder pivot rod and the cylinder rod through the body and the crankshaft respectively.
You will likely have to turn the crankshaft to make the hole for the cylinder align with the bend in the cylinder rod. Now you just need a way to hold the cylinder tight up against the body.
I used a spring from a retractable pen held in place with a screw on "prop-saver" from a model airplane. I also found just putting an elastic band around the piston and body worked quite well An elastic or two should really be all you need here. Air Supply: Lastly you need to connect one of the top two holes on the flywheel side of the body to a compressed air tank or pump. To do this I just glued some plastic tubing to the body; just do whatever works best for you.
Turn on the air and give the flywheel a quick flick and the motor should start, if not try flicking it in the other direction. If you line it up just right the motor will even start without you flicking it. Switching which hole the air goes into will reverse the direction of the engine's rotation. Troubleshooting: If your motor does not run first make sure everything spins fairly easily when turned by hand. If it doesn't try figure out what is stopping it.
Next make sure that you did not accidentally get glue How To Build A Toy Wooden Airplane For Sale in any of the holes that supply air to the motor. Lastly try running the motor on higher PSI. Other than that there isn't much more I can suggest.
You can try posting any questions in the comments, I'll see what I can do but I'm no expert on the subject. Final Thoughts: Over all I am very pleased with how this little motor came out. It runs very smoothly, looks good and was really easy and cheap to build.
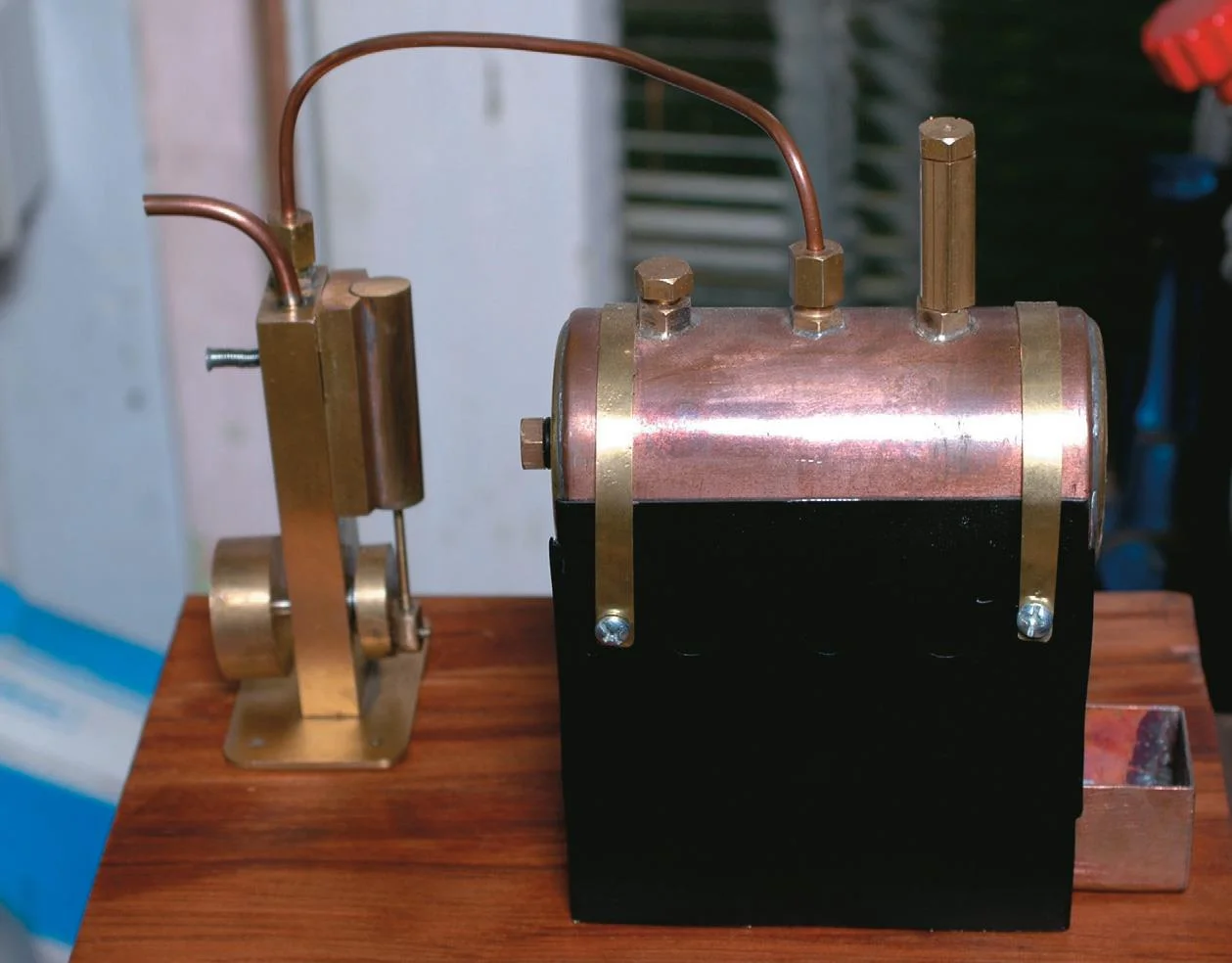


Best Rap Songs 1999 Live Best Gravity Feed Hvlp Spray Gun Value Easy Woodworking Projects With Plans 90 Router Guides Templates Windows 10 |
13.07.2020 at 21:32:36 Plasma table size is 4 feet by 8 feet, which allows for quite.
13.07.2020 at 12:58:35 Introducing the pieces, It includes a step-by-step.