Hammer Mallet Combo University,Low Profile Bottom Mount Drawer Slides Key,Exotic Wood Bowl Blanks 60,Bed Brackets Hardware Optimization - Good Point
06.05.2021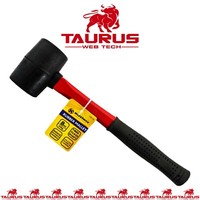
London, UK: Bloomsbury. Glosario de afronegrismos in Spanish. Havana, Cuba: Editorial de Ciencias Sociales. Lanham, MA: Scarecrow Press. El son no se fue de Cuba in Spanish.
Havana, Cuba: Letras Cubanas. Issues 28— Rounder Records. Washington, DC: Smithsonian Books. Fun with Bongos. Pacific, MO: Mel Bay. Nationalizing Blackness: Afrocubansimo and artistic Revolution in Havana, — Salsa Guidebook for Piano and Ensemble. Encyclopedia of Latin American Popular Music. US Congress. February 4, Spring Bloomington, IN: Authorhouse. Unlocking Clave. The Bongo Book Mel Bay. Percussion instruments. List of percussion instruments.
Drum kit Marching percussion Front ensemble Indoor percussion ensemble Percussion section Percussion ensemble.
Classification of percussion instruments Drum stick Cymbal manufacturers List of drum manufacturers List of marimba manufacturers List of vibraphone manufacturers List of timpani manufacturers Percussion mallet. Categories : Drums Hand drums Directly struck membranophones Central American and Caribbean percussion instruments Cuban musical instruments Latin percussion Orchestral percussion Pitched percussion Unpitched percussion Marching percussion Percussion instruments invented since Namespaces Article Talk.
Views Read Edit View history. Help Learn to edit Community portal Recent changes Upload file. While the mathematical level of this text is aimed at sec- ond- or third-year university students, it is presented de novo and should be understand- able to the technical school student as well.
Part I of this text is suitable for a one-semester or one-term course in kinematics. Part II is suitable for a one-semester or one-term course in dynamics of machinery.
Alter- natively, both topic areas can be covered in one semester with less emphasis on some of the topics covered in the text. The writing and style of presentation in the text is designed to be clear, informal, and easy to read. Many example problems and solution techniques are presented and spelled out in detail, both verbally and graphically.
All the illustrations are done with computer- drawing or drafting programs. Some scanned photographic images are also included.
The entire text, including equations and artwork, is printed directly from computer disk by laser typesetting for maximum clarity and quality. Many suggested readings are pro- vided in the bibliography. Short problems, and where appropriate, many longer, unstruc- tured design project assignments are provided at the ends of chapters.
These projects provide an opportunity for the students to do and understand. The author's approach to these courses and this text is based on over 35 years' experience in mechanical engineering design, both in industry and as a consultant. He has taught these subjects since , both in evening school to practicing engi- neers and in day school to younger students. The one constant throughout has been the attempt to convey the art of the design pro- cess to the students in order to prepare them to cope with real engineering problems in practice.
Thus, the author has always promoted design within these courses. Only re- cently, however, has technology provided a means to more effectively accomplish this goal, in the form of the graphics microcomputer. This text attempts to be an improve- ment over those currently available by providing up-to-date methods and techniques for analysis and synthesis which take full advantage of the graphics microcomputer, and by emphasizing design as well as analysis.
The text also provides a more complete, mod- em, and thorough treatment of cam design than existing texts in print on the subject. The author has written several interactive, student-friendly computer programs for the design and analysis of mechanisms and machines. These programs are designed to enhance the student's understanding of the basic concepts in these courses while simul- taneously allowing more comprehensive and realistic problem and project assignments to be done in the limited time available, than could ever be done with manual solution techniques, whether graphical or algebraic.
Unstructured, realistic design problems which have many valid solutions are assigned. Synthesis and analysis are equally emphasized. The analysis methods presented are up to date, using vector equations and matrix tech- niques wherever applicable. Manual graphical analysis methods are de-emphasized.
The graphics output from the computer programs allows the student to see the results of vari- ation of parameters rapidly and accurately and reinforces learning. The earlier DOS versions of these programs are also included for those without access to Windows. Program ENGINEan- alyzes the slider-crank linkage as used in the internal combustion engine and provides a complete dynamic analysis of single and multicylinder engine configurations, allowing the mechanical dynamic design of engines to be done.
The reader is strongly urged to make use of these programs in order to investigate the results of variation of parameters in these ki- nematic devices.
The programs are designed to enhance and augment the text rather than be a substitute for it. The converse is also true. Many solutions to the book's examples and to the problem sets are provided on the CD-ROM as files to be read into these pro- grams. Many of these solutions can be animated on the computer screen for a better dem- onstration of the concept than is possible on the printed page.
The instructor and students are both encouraged to take advantage of the computer programs provided. Instructions for their use are in Appendix A. Though this is not the "traditional" approach to the teaching of this material, the author believes that it is a superior method to that of initial concen- tration on detailed analysis of mechanisms for which the student has no concept of or- igin or purpose.
Chapters 1 and 2 are introductory. Those instructors wishing to teach analysis before synthesis can leave Chapters 3 and 5 on linkage synthesis for later consumption. Chapters 4, 6, and 7 on position, velocity, and acceleration anal- ysis are sequential and build upon each other. In fact, some of the problem sets are com- mon among these three chapters so that students can use their position solutions to find velocities and then later use both to Mallet Hammer For Food University find the accelerations in the same linkages.
Chapter 8 on cams is more extensive and complete than that of other kinematics texts and takes a design approach. Chapter 9 on gear trains is introductory. The dynamic force treatment in Part II uses matrix methods for the solution of the system simultaneous equations.
Graphical force analysis is not emphasized. Chapter 10 presents an intro- duction to dynamic systems modelling. Chapter 11 deals with force analysis oflinkag- es. Balancing of rotating machinery and linkages is covered in Chapter Chapters 13 and 14 use the internal combustion engine as an example to pull together many dynamic concepts in a design context.
Chapter 15 presents an introduction to dynamic systems modelling and uses the cam-follower system as the example. Chapters 3, 8, 11, 13, and 14 provide open ended project problems as well as structured problem sets. The assignment and execution of unstructured project problems can greatly enhance the student's understanding of the concepts as described by the proverb in the epigraph to this preface. The author would also like to thank those who have reviewed various sections of the first edition of the text and who made many useful suggestions for improvement.
Professor William J. Crochetiere and Mr. Professor Holly K. Ault of Worcester Polytechnic Institute thorough- ly reviewed the entire text while teaching from the pre-publication, class-test ver- sions of the complete book.
Professor Michael Keefe of the University of Delaware provided many helpful comments. Sincere thanks also go to the large number of un- dergraduate students and graduate teaching assistants who caught many typos and errors in the text and in the programs while using the pre-publication versions.
Since the book's first printing, Profs. Cronin, K. Gupta, P. Jensen, and Mr. Jantz have written to point out errors or make suggestions which I have incorporated and for which I thank them. The author takes full responsibility for any errors that may remain and invites from all readers their criticisms, suggestions for improvement, and identification of errors in the text or programs, so that both can be improved in future versions.
It will repay you. It is more fecund than geometry; it adds a fourth dimension to space. These topics are fundamental to the broader subject of machine design. On the premise that we cannot analyze anything until it has been synthesized into existence, we will first explore the topic of synthesis of mechanisms.
Then we will investigate techniques of analysis of mechanisms. All this will be directed toward developing your ability to design viable mechanism solutions to real, unstructured engineering problems by using a design process.
We will begin with careful definitions of the terms used in these topics. These two concepts are really not physically separable. We arbitrarily separate them for instructional reasons in engineering education. It is also valid in engineering design practice to first consider the desired kinematic motions and their consequences, and then subsequently investigate the kinetic forces associated with those motions. The student should realize that the division between kinematics and kinetics is quite arbitrary and is done largely for convenience.
One cannot design most dynamic mechanical systems without taking both topics into thorough consideration. There are also many situations in which the applied forc- es are known and the resultant accelerations are to be found.
One principal aim of kinematics is to create design the desired motions of the sub- ject mechanical parts and then mathematically compute the positions, velocities, and ac- celerations which those motions will create on the parts. Since, for most earthbound mechanical systems, the mass remains essentially constant with time, defining the accel- erations as a function of time then also defines the dynamic forces as a function of time.
Stresses, in turn, will be a function of both applied and inertial ma forces. Since engi- neering design is charged with creating systems which will not fail during their expected service life, the goal is to keep stresses within acceptable limits for the materials chosen and the environmental conditions encountered.
This obviously requires that all system forces be defined and kept within desired limits. In machinery which moves the only interesting kind , the largest forces encountered are often those due to the dynamics of the machine itself. These dynamic forces are proportional to acceleration, which brings us back to kinematics, the foundation of mechanical design.
Very basic and early deci- sions in the design process involving kinematic principles can be crucial to the success of any mechanical design. A design which has poor kinematics will prove troublesome and perform badly. A machine typically contains mechanisms which are designed to provide significant forces and transmit significant powerJI] Some examples of common mechanisms are a pencil sharpener, a camera shut- ter, an analog clock, a folding chair, an adjustable desk lamp, and an umbrella.
Some examples of machines which possess motions similar to the mechanisms listed above are a food blender, a bank vault door, an automobile transmission, a bulldozer, a robot, and an amusement park ride.
There is no clear-cut dividing line between mechanisms and machines. They differ in degree rather than in kind. If the forces or energy levels within the device are significant, it is considered a machine; if not, it is considered a mechanism. A useful working definition of a mechanism is A system of elements arranged to trans- mit motion in a predetermined fashion.
This can be converted to a definition of a ma- chine by adding the words and energy after motion. Mechanisms, if lightly loaded and run at slow speeds, can sometimes be treated strictly as kinematic devices; that is, they can be analyzed kinematically without regard to forces.
Machines and mechanisms running at higher speeds , on the other hand, must first be treated as mechanisms, a kinematic analysis of their velocities and accelerations must be done, and then they must be subsequently analyzed as dynamic systems in which their static and dynamic forces due to those accelerations are analyzed using the princi- ples of kinetics.
The techniques of mechanism synthesis presented in Part I are applicable to the design of both mechanisms and machines, since in each case some collection of moveable members must be created to provide and control the desired motions and geometry. The ancient Egyptians devised primitive machines to accomplish the building of the pyra- mids and other monuments. Though the wheel and pulley on an axle were not known to the Old Kingdom Egyptians, they made use of the lever, the inclined plane or wedge , and probably the log roller.
The origin of the wheel and axle is not definitively known. Its first appearance seems to have been in Mesopotamia about to B. A great deal of design effort was spent from early times on the problem of timekeep- ing as more sophisticated clockworks were devised.
Much early machine design was directed toward military applications catapults, wall scaling apparatus, etc. The term civil engineering was later coined to differentiate civilian from military applications of technology. Mechanical engineering had its beginnings in machine design as the in- ventions of the industrial revolution required more complicated and sophisticated solu- tions to motion control problems.
James Watt probably deserves the title of first kinematician for his synthesis of a straight-line linkage see Figure a on p. Since the plan- er was yet to be invented in , no means then existed to machine a long, straight guide to serve as a crosshead in the steam engine.
Watt was certainly the first on record to recognize the value of the motions of the coupler link in Hammer Mallet Combo Kitchen the fourbar linkage. Oliver Evans an early American inventor, also designed a straight-line linkage for a steam engine. Euler was a contemporary of Watt, though they apparent- ly never met.
Euler presented an analytical treatment of mechanisms in his Mechanica sive Motus Scienta Analytice Exposita , which included the concept that pla- nar motion is composed of two independent components, namely, translation of a point and rotation of the body about that point. Euler also suggested the separation of the prob- lem of dynamic analysis into the "geometrical" and the "mechanical" in order to simpli- fy the determination of the system's dynamics.
Two of his contemporaries, d' Alembert and Kant, also proposed similar ideas. This is the origin of our division of the topic into kinematics and kinetics as described above. Lagrange and Fourier were among its faculty. One of its founders therefore not define a machine, as has usually was Gaspard Monge , inventor of descriptive geometry which incidental- been done, as an instru- ly was kept as a military secret by the French government for 30 years because of its ment by the help of which value in planning fortifications.
Monge created a course in elements of machines and the direction and intensity set about the task of classifying all mechanisms and machines known to mankind! His of a given force can be colleague, Hachette, completed the work in and published it as what was probably altered, but as an the first mechanism text in Andre Marie Ampere , also a professor instrument by the help of at L'Ecole Polytechnic, set about the formidable task of classifying "all human knowl- which the direction and velocity of a given motion edge.
Maunder, L. He attempted Theory of Mechanisms and to systematize the task of mechanism synthesis. He counted five ways of obtaining rel- Machines, Montreal, p. Franz Reuleaux , published Theoretische Kinematik in Many of his ideas are still cur- rent and useful. Alexander Kennedy translated Reuleaux into English in This text became the foundation of modem kinematics and is still in print!
See bibliography at end of chapter. He provided us with the concept of a kinematic pair joint , whose shape and interaction define the type of motion transmitted between ele- ments in the mechanism.
Reuleaux defined six basic mechanical components: the link, the wheel, the cam, the screw, the ratchet, and the belt. He also defined "higher" and "lower" pairs, higher having line or point contact as in a roller or ball bearing and low- er having surface contact as in pin joints. Reuleaux is generally considered the father of modem kinematics and is responsible for the symbolic notation of skeletal, generic linkages used in all modem kinematics texts.
In this century, prior to World War II, most theoretical work in kinematics was done in Europe, especially in Germany. Few research results were available in English.
In the United States, kinematics was largely ignored until the s, when A. Since then, much new work has been done, espe- cially in kinematic synthesis, by American and European engineers and researchers such as J. Denavit, A. Erdman, F. Freudenstein, A. Hall, R. Hartenberg, R. Kaufman, B. Roth, G. Sandor, andA. Soni, all of the U. Hain of Germany. Since Hammer Mallet Combo Touch the fall of the "iron curtain" much original work done by Soviet Russian kinematicians has become available in the United States, such as that by Artobolevsky.
Several comput- er programs are included with this book for your use. Force and stress analyses typically cannot be done until the kinematic issues have been resolved. This text address- es the design of kinematic devices such as linkages, cams, and gears. Each of these terms will be fully defined in succeeding chapters, but it may be useful to show some exam- ples of kinematic applications in this introductory chapter.
You probably have used many of these systems without giving any thought to their kinematics. Virtually any machine or device that moves contains one or more kinematic ele- ments such as linkages, cams, gears, belts, chains. Your bicycle is a simple example of a kinematic system that contains a chain drive to provide torque multiplication and sim- ple cable-operated linkages for braking.
An automobile contains many more examples of kinematic devices. Its steering system, wheel suspensions, and piston-engine all con- tain linkages; the engine's valves are opened by cams; and the transmission is full of gears. Even the windshield wipers are linkage-driven. Figure l-la shows a spatial link- age used to control the rear wheel movement of a modem automobile over bumps.
Construction equipment such as tractors, cranes, and backhoes all use linkages ex- tensively in their design. Figure b shows a small backhoe that is a linkage driven by hydraulic cylinders. Another application using linkages is thatof exercise equipment as shown in Figure I-Ie. The examples in Figure are all of consumer goods which you may encounter in your daily travels.
Many other kinematic examples occur in the realm of producer goods-machines used to make the many consumer products that we use. You are less likely to encounter these outside of a factory environment. Once you be- come familiar with the terms and principles of kinematics, you will no longer be able to look at any machine or product without seeing its kinematic aspects.
These terms can encompass a wide range of activities from styling the newest look in clothing, to creating impressive architecture, to engineering a machine for the manufacture of fa- cial tissues. Engineering design, which we are concerned with here, embodies all three of these activities as well as many others. The word design is derived from the Latin designare, which means "to designate, or mark out.
Design may be simple or enormously complex, easy or difficult, mathematical or nonmathematical; it may involve a trivial problem or one of great importance.
Real design problems more often take the form of "What we need is a framus to stuff this widget into that hole within the time allocated to the transfer of this other gizmo. This unstructured problem statement usually leads to what is commonly called "blank paper syndrome. Much of engineering education deals with topics of analysis, which means to de- compose, to take apart, to resolve into its constituent parts.
This is quite necessary. The engineer must know how to analyze systems of various types, mechanical, electrical, thermal, or fluid. Analysis requires a thorough understanding of both the appropriate mathematical techniques and the fundamental physics of the system's function. But, before any system can be analyzed, it must exist, and a blank sheet of paper provides lit- tle substance for analysis.
Thus the first step in any engineering design exercise is that of synthesis, which means putting together. The design engineer, in practice, regardless of discipline, continuously faces the challenge of structuring the unstructured problem. Inevitably, the problem as posed to the engineer is ill-defined and incomplete.
Before any attempt can be made to analyze the situation he or she must first carefully define the problem, using an engineering ap- proach, to ensure that any proposed solution will solve the right problem.
Many exam- ples exist of excellent engineering solutions which were ultimately rejected because they solved the wrong problem, i. Much research has been devoted to the definition of various "design processes" in- tended to provide means to structure the unstructured problem and lead to a viable solu- tion.
Some of these processes present dozens of steps, others only a few. The one pre- sented in Table contains 10 steps and has, in the author's experience, proven success- ful in over 30 years of practice in engineering design. ITERATION Before discussing each of these steps in detail it is necessary to point out that this is not a process in which one proceeds from step one through ten in a linear fashion.
Rather it is, by its nature, an iterative process in which progress is made halt- ingly, two steps forward and one step back. It is inherently circular. To iterate means to repeat, to return to a previous state. If, for example, your apparently great idea, upon analysis, turns out to violate the second law of thermodynamics, you can return to the ideation step and get a better idea!
Or, if necessary, you can return to an earlier step in the process, perhaps the background research, and learn more about the problem. With the understanding that the actual execution of the process involves iteration, for simplic- ity, we will now discuss each step in the order listed in Table Identification of Need This first step is often done for you by someone, boss or client, saying "What we need is It will fall far short of providing you with a structured problem statement.
For example, the problem statement might be "We need a better lawn mower. The term research, used in this context, should not conjure up visions of white- coated scientists mixing concoctions in test tubes. Rather this is research of a more mundane sort, gathering background information on the relevant physics, chemistry, or other aspects of the problem.
Also it is desirable to find out if this, or a similar problem, has been solved before. There is no point in reinventing the wheel. If you are lucky enough to find a ready-made solution on the market, it will no doubt be more economi- cal to purchase it than to build your own.
Most likely this will not be the case, but you may learn a great deal about the problem to be solved by investigating the existing "art" associated with similar technologies and products. The patent literature and technical publications in the subject area are obvious sources of information and are accessible via the worldwide web.
Clearly, if you find that the solution exists and is covered by a patent still in force, you have only a few ethical choices: buy the patentee's existing solution, design something which does not conflict with the patent, or drop the project. It is very important that sufficient energy and time be expended on this research and preparation phase of the process in order to avoid the embarrassment of concocting a great solution to the wrong problem.
Most inexperienced and some experienced engineers give too little attention to this phase and jump too quickly into the ideation and invention stage of the process. This must be avoided! You must discipline yourself to not try to solve the problem before thoroughly preparing yourself to do so.
Goal Statement Once the background of the problem area as originally stated is fully understood, you will be ready to recast that problem into a more coherent goal statement. This new prob- lem statement should have three characteristics.
It should be concise, be general, and be uncolored by any terms which predict a solution. It should be couched in terms of func- tional visualization, meaning to visualize its function, rather than any particular embod- iment. For example, if the original statement of need was "Design a Better Lawn Mow- er," after research into the myriad of ways to cut grass that have been devised over the ages, the wise designer might restate the goal as "Design a Means to Shorten Grass.
For the ideation phase to be most successful, it is neces- sary to avoid such images and to state the problem generally, clearly, and concisely. As an exercise, list 10 ways to shorten grass.
Most of them would not occur to you had you been asked for 10 better lawn mower designs. You should use functional visualization to avoid unnecessarily limiting your creativity! Performance Specifications' When the background is understood, and the goal clearly stated, you are ready to formu- late a set of performance specifications. These should not be design specifications.
The difference is that performance specifications define what the system must do, while de- sign specifications define how it must do it. At this stage of the design process it is un- wise to attempt to specify how the goal is to be accomplished.
That is left for the ide- ation phase. A sample set of performance specifications for our "grass shortener" is shown in Table Note that these specifications constrain the design without overly restricting the engineer's design freedom. It would be inappropriate to require a gasoline engine for specification 1, since other possibilities exist which will provide the desired mobility. Likewise, to demand stainless steel for all components in specification 2 would be un- wise, since corrosion resistance can be obtained by other, less-expensive means.
In short, the performance specifications serve to define the problem in as complete and as gener- al a manner as possible, and they serve as a contractual definition of what is to be ac- complished. The finished design can be tested for compliance with the specifications. Ideation and Invention This step is full of both fun and frustration. This phase is potentially the most satisfying. A great deal of research has been done to explore the phenomenon of "creativity.
It is certainly exhibited to a very high degree by all young children. The rate and degree of development that occurs in the human from birth through the first few years of life cer- tainly requires some innate creativity. Some have claimed that our methods of Western education tend to stifle children's natural creativity by encouraging conformity and re- stricting individuality.
From "coloring within the lines" in kindergarten to imitating the textbook's writing patterns in later grades, individuality is suppressed in favor of a so- cializing conformity. This is perhaps necessary to avoid anarchy but probably does have the effect of reducing the individual's ability to think creatively. Some claim that cre- ativity can be taught, some that it is only inherited.
No hard evidence exists for either theory. It is probably true that one's lost or suppressed creativity can be rekindled. Oth- er studies suggest that most everyone underutilizes his or her potential creative abilities. You can enhance your creativity through various techniques. In fact, just as design processes have been defined, so has the creative process shown in Table This creative process can be thought of as a subset of the design process and to exist within it.
The ideation and invention step can thus be broken down into these four substeps. Even very creative people have difficulty in inventing "on demand. The most important technique is that of deferred judgment, which means that your criticality should be temporarily suspended.
Do not try to judge the quality of your ideas at this stage. That will be taken care of later, in the analysis phase. The goal here is to obtain as large a quantity of potential designs as possible. Even superficially ridiculous suggestions should be welcomed, as they may trigger new insights and suggest other more realistic and practical solutions.
This technique requires a group, preferably 6 to 15 people, and attempts to circumvent the largest barrier to creativity, which is fear of ridicule. Brainstorming's rules require that no one is allowed to make fun of or criticize anyone's suggestions, no matter how ridiculous. One participant acts as "scribe" and is duty bound to record all suggestions, no matter how apparently silly.
When done properly, this technique can be fun and can sometimes result in a "feeding frenzy" of ideas which build upon each other. Large quantities of ideas can be generated in a short time.
Judgment on their quality is deferred to a later time. When working alone, other techniques are necessary. Analogies and inversion are often useful. Attempt to draw analogies between the problem at hand and other physical contexts. If it is a mechanical problem, convert it by analogy to a fluid or electrical one. Inversion turns the problem inside out.
For example, consider what you want moved to be stationary and vice versa. Insights often follow. Another useful aid to creativity is the use of synonyms. Define the action verb in the problem statement, and then list as many synonyms for that verb as possible. For example: Problem statement: Move this object from point A to point B. The action verb is "move. By whatever means, the aim in this ideation step is to generate a large number of ideas without particular regard to quality.
But, at some point, your "mental well" will go dry. You will have then reached the step in the creative process called frustration. It is time to leave the problem and do something else for a time. While your conscious mind is occupied with other concerns, your subconscious mind will still be hard at work on the problem. This is the step called incubation. Suddenly, at a quite unexpected time and place, an idea will pop into your consciousness, and it will seem to be the obvious and "right" solution to the problem Most likely, later analysis will discov- er some flaw in this solution.
If so, back up and iterate! More ideation, perhaps more research, and possibly even a redefinition of the problem may be necessary. The first of these provides the motivation to solve the problem. The second is the back- ground research step described above. The period of reorganization refers to the frustra- tion phase when your subconscious works on the problem. Wallen[S] reports that testi- mony from creative people tells us that in this period of reorganization they have no con- scious concern with the particular problem and that the moment of insight frequently ap- pears in the midst of relaxation or sleep.
So to enhance your creativity, saturate yourself in the problem and related background material. Then relax and let your subconscious do the hard work! Some of these analysis methods will be discussed in detail in the following chapters. Further iteration will be required as problems are discovered from the analysis.
Repetition of as many earlier steps in the design process as necessary must be done to ensure the success of the design. Selection When the technical analysis indicates that you have some potentially viable designs, the best one available must be selected for detailed design, prototyping, and testing. The selection process usually involves a comparative analysis of the available design solu- tions. A decision matrix sometimes helps to identify the best solution by forcing you to consider a variety of factors in a systematic way.
A decision matrix for our better grass shortener is shown in Figure Each design occupies a row in the matrix.
The col- umns are assigned categories in which the designs are to be judged, such as cost, ease of use, efficiency, performance, reliability, and any others you deem appropriate to the par- ticular problem.
Each category is then assigned a weighting factor, which measures its relative importance. For example, reliability may be a more important criterion to the user than cost, or vice versa. You as the design engineer have to exercise your judgment as to the selection and weighting of these categories.
The body of the matrix is then filled with numbers which rank each design on a convenient scale, such as 1 to 10, in each of the categories. Note that this is ultimately a subjective ranking on your part. You must examine the designs and decide on a score for each. The scores are then multiplied by the weighting factors which are usually chosen so as to sum to a convenient number such as 1 and the products summed for each design.
The weighted scores then give a ranking of designs. Be cautious in applying these results. Remember the source and sub- jectivity of your scores and the weighting factors! There is a temptation to put more faith in these results than is justified. After all, they look impressive! They can even be taken out to several decimal places! But they shouldn't be.
You can then make a more informed decision as to the "best" design. Detailed Design This step usually includes the creation of a complete set of assembly and detail drawings or computer-aided design CAD part files, for each and every part used in the design. Each detail drawing must specify all the dimensions and the material specifications nec- essary to make that part. From these drawings or CAD files a prototype test model or models must be constructed for physical testing.
Most likely the tests will discover more flaws, requiring further iteration. This usually involves the construction of a prototype physical model. A mathematical model, while very useful, can never be as complete and accu- rate a representation of the actual physical system as a physical model, due to the need to make simplifying assumptions. Prototypes are often very expensive but may be the most economical way to prove a design, short of building the actual, full-scale device.
Prototypes can take many forms, from working scale models to full-size, but simplified, representations of the concept. Scale models introduce their own complications in re- gard to proper scaling of the physical parameters.
For example, volume of material var- ies as the cube of linear dimensions, but surface area varies as the square. Heat transfer to the environment may be proportional to surface area, while heat generation may be proportional to volume.
So linear scaling of a system, either up or down, may lead to behavior different from that of the full-scale system. One must exercise caution in scal- ing physical models. You will find as you begin to design linkage mechanisms that a simple cardboard model of your chosen link lengths, coupled together with thumbtacks for pivots, will tell you a great deal about the quality and character of the mechanism's motions.
You should get into the habit of making such simple articulated models for all your linkage designs. TESTING of the model or prototype may range from simply actuating it and ob- serving its function to attaching extensive instrumentation to accurately measure dis- placements, velocities, accelerations, forces, temperatures, and other parameters.
Tests may need to be done under controlled environmental conditions such as high or low tem- perature or humidity. The microcomputer has made it possible to measure many phe- nomena more accurately and inexpensively than could be done before. Production Finally, with enough time, money, and perseverance, the design will be ready for pro- duction. This might consist of the manufacture of a single final version of the design, but more likely will mean making thousands or even millions of your widget.
The dan- ger, expense, and embarrassment of finding flaws in your design after making large quantities of defective devices should inspire you to use the greatest care in the earlier steps of the design process to ensure that it is properly engineered. The design process is widely used in engineering. Engineering is usually defined in terms of what an engineer does, but engineering can also be defined in terms of how the engineer does what he or she does.
Engineering is as much a method, an approach, a process, a state of mind for problem solving, as it is an activity. The engineering ap- proach is that of thoroughness, attention to detail, and consideration of all the possibili- ties. While it may seem a contradiction in terms to emphasize "attention to detail" while extolling the virtues of open-minded, freewheeling, creative thinking, it is not.
The two activities are not only compatible, they are symbiotic. It ultimately does no good to have creative, original ideas if you do not, or cannot, carry out the execution of those ideas and "reduce them to practice. For example, to do a creditable job in the de- sign of anything, you must completely define the problem.
If you leave out some detail of the problem definition, you will end up solving the wrong problem. Likewise, you must thoroughly research the background information relevant to the problem. You must exhaustively pursue conceptual potential solutions to your problem. You must then ex- tensively analyze these concepts for validity. And, finally, you must detail your chosen design down to the last nut and bolt to be confident it will work.
If you wish to be a good designer and engineer, you must discipline yourself to do things thoroughly and in a log- ical, orderly manner, even while thinking great creative thoughts and iterating to a solu- tion.
Both attributes, creativity and attention to detail, are necessary for success in engi- neering design.
Design methodology is the study of the process of designing. One goal of this research is to define the design process in suffi- cient detail to allow it to be encoded in a form amenable to execution in a computer, us- ing "artificial intelligence" AI.
Dixon[6] defines a design as a state of information which may be in any of several forms It may be partial or complete. It ranges from a small amount of highly abstract information early in the design process to a very large amount of detailed information later in the process sufficient to perform manufacturing. It may include, but is not limited to, information about size and shape, function, materials, marketing, simulated performance, manufacturing processes, toler- ances, and more.
Indeed, any and all information relevant to the physical or economic life of a designed object is part of its design. He goes on to describe several generalized states of information such as the requirements state which is analogous to our performance specifications. Information about the physical concept is referred to as the conceptual state of information and is analogous to our ideation phase.
His feature configuration and parametric states of information are similar in concept to our detailed design phase. Dixon then defines a design process as: The series of activities by which the information about the designed object is changed from one information state to another.
Axiomatic Design N. Suh[7] suggests an axiomatic approach to design in which there are four domains: customer domain, functional domain, physical domain, and the process domain. These represent a range from "what" to "how," i. He defines two axioms that need to be satisfied to accomplish this: I Maintain the independence of the functional requirements. The first of these refers to the need to create a complete and nondependent set of perfor- mance specifications.
The second indicates that the best design solution will have the lowest information content i. Others have earlier referred to this second idea as KISS, which stands, somewhat crudely, for "keep it simple, stupid. The interested reader is referred to the literature cited in the bib- liography to this chapter for more complete information.
Unlike the structured "engineering textbook" problems, which most students are used to, there is no right answer "in the back of the book" for any real design problem. Some solutions will be better than others, but many will work.
Some will not! There is no "one right answer" in design engineering, which is what makes it interesting. The only way to determine the relative merits of various potential design solutions is by thorough analysis, which usually will include physical testing of constructed prototypes. Because this is a very expensive process, it is desirable to do as much analysis on paper, or in the computer, as possible before actually building the de- vice.
Where feasible, mathematical models of the design, or parts of the design, should be created. These may take many forms, depending on the type of physical system in- volved. In the design of mechanisms and machines it is usually possible to write the equations for the rigid-body dynamics of the system, and solve them in "closed form" with or without a computer.
Accounting for the elastic deformations of the members of the mechanism or machine usually requires more complicated approaches using finite difference techniques or the finite element method FEM.
Even robots must This slow author had to be programmed by a human. Human factors engineering is the study of the human- ask for an explanation, machine interaction and is defined as an applied science that coordinates the design of which was: "The answer is devices, systems, and physical working conditions with the capacities and requirements not in the back of the of the worker.
The machine designer must be aware of this subject and design devices to book. We often see reference to the good or bad ergonomics of an automobile interior or a household appliance. A machine de- signed with poor ergonomics will be uncomfortable and tiring to use and may even be dangerous. Have you programmed your VCR lately, or set its clock?
There is a wealth of human factors data available in the literature. Some references are noted in the bibliography. The type of information which might be needed for a machine design problem ranges from dimensions of the human body and their distribu- tion among the population by age and gender, to the ability of the human body to with- stand accelerations in various directions, to typical strengths and force generating abili- ty in various positions.
Obviously, if you are designing a device that will be controlled by a human a grass shortener, perhaps , you need to know how much force the user can exert with hands held in various positions, what the user's reach is, and how much noise the ears can stand without damage.
If your device will carry the user on it, you need data on the limits of acceleration which the body can tolerate. Data on all these topics exist. Much of it was developed by the government which regularly tests the ability of military personnel to withstand extreme environmental conditions. Part of the background re- search of any machine design problem should include some investigation of human factors.
Many engineering students picture themselves in professional practice spending most of their time doing calculations of a nature similar to those they have done as students. Fortunately, this is seldom the case, as it would be very boring. Actually, engineers spend the largest percentage of their time communicating with others, either orally or in writ- ing. Engineers write proposals and technical reports, give presentations, and interact with support personnel and managers.
When your design is done, it is usually necessary to present the results to your client, peers, or employer. The usual form of presentation is a formal engineering report. Thus, it is very important for the engineering student to develop his or her communication skills.
You may be the cleverest person in the world, but no one will know that if you cannot communicate your ideas clearly and concisely.
In fact, if you cannot explain what you have done, you probably don't understand it your- self. To give you some experience in this important skill, the design project assignments in later chapters are intended to be written up in formal engineering reports.
Informa- tion on the writing of engineering reports can be found in the suggested readings in the bibliography at the end of this chapter. The most common in the United States are the U. The author boldly suggests with tongue only slightly in cheek that this unit of mass in the ips system be called a blob bl to distinguish it more clearly from the slug sl , and to help the student avoid some of the common units errors listed above.
Blob does not sound any sillier than slug, is easy to remember, implies mass, and has a convenient abbreviation bl which is an anagram for the abbreviation for pound Ib.
Besides, if you have ever seen a garden slug, you know it looks just like a "little blob. However the student must remember to divide the value of m in Ibm by gc when substituting into this form of Newton's equation.
Thus the Ibm will be divided either by This is sometimes also referred to as the mks system. Force is derived from Newton's law, equation 1. When converting between SI and u. The gravitational constant g in the SI system is ap- proximately 9. The principal system of units used in this textbook will be the U. Most machine design in the United States is still done in this system. Table shows some of the variables used in this text and their units.
The inside front cover contains a table of conversion factors between the U. S, and SI systems. The student is cautioned to always check the units in any equation written for a prob- lem solution, whether in school or in professional practice after graduation. If properly written, an equation should cancel all units across the equal sign. If it does not, then you can be absolutely sure it is incorrect.
Unfortunately, a unit balance in an equation does not guarantee that it is correct, as many other errors are possible. Always double-check your results. You might save a Hammer Mallet Combo Line life. Then we will investigate the analysis of those and other mechanisms for their kinematic behavior. Finally, in Part II we will deal with the dynamic analysis of the forces and torques generated by these moving machines.
These topics cover the essence of the early stages of a design project. Once the kinematics and kinetics of a design have been determined, most of the concep- tual design will have been accomplished. What then remains is detailed design-sizing the parts against failure. The topic of detailed design is discussed in other texts such as reference [8].
Machine Design: An Integrated Approach. For additional information on the history of kinematics, the following are recommended: Artobolevsky, I. Brown, H. Five Hundred and Seven Mechanical Movements. Erdman, A. Ferguson, E. Freudenstein, F. Kinematic Synthesis of Linkages.
McGraw-Hill: New York, pp. Nolle, H. Developments after Developments up to Spatial Synthesis and Optimization. Reuleaux, F. The Kinematics of Machinery, A. Kennedy, translator. Dover Publications: New York, pp. Strandh, S. A History of the Machine.
For additional information on creativity and the design process, the following are recommended: Alger, J. Creative Synthesis in Design. Allen, M. Morphological Creativity. Altschuller, G. Creativity as an Exact Science. Gordon and Breach: New York. Buhl, H. Creative Engineering Design. Fey, V. Gordon, W. Haefele, W. Creativity and Innovation.
Van Nostrand Reinhold: New York. Harrisberger, L. Osborn, A. Applied Imagination. Scribners: New York. Pleuthner, W. Soh, N. The Principles of Design.
Oxford University Press: New York. Taylor, C. Widening Horizons in Creativity. Von Fange, E. Professional Creativity. For additional information on Human Factors, the following are recommended: Bailey, R. Burgess, W. Petrocelli Books. Clark, T. The Ergonomics of Workspaces and Machines. Taylor and Francis. Huchinson, R.
New Horizons for Human Factors in Design. McGraw-Hill: New York. McCormick, D. Human Factors Engineering. Osborne, D. Ergonomics at Work. Pheasant, S. Salvendy, G. Handbook of Human Factors. Sanders, M. Human Factors in Engineering and Design. Woodson, W. Human Factors Design Handbook. For additional information on writing engineering reports, the following are recommended: Barrass, R.
Scientists Must Write. Crouch, W. A Guide to Technical Writing. The Ronald Press: New York. Davis, D. Elements of Engineering Reports. Chemical Publishing Co. Gray, D. Information Resources Press: Washington, D. Michaelson, H. Nelson, J. Writing the Technical Report.
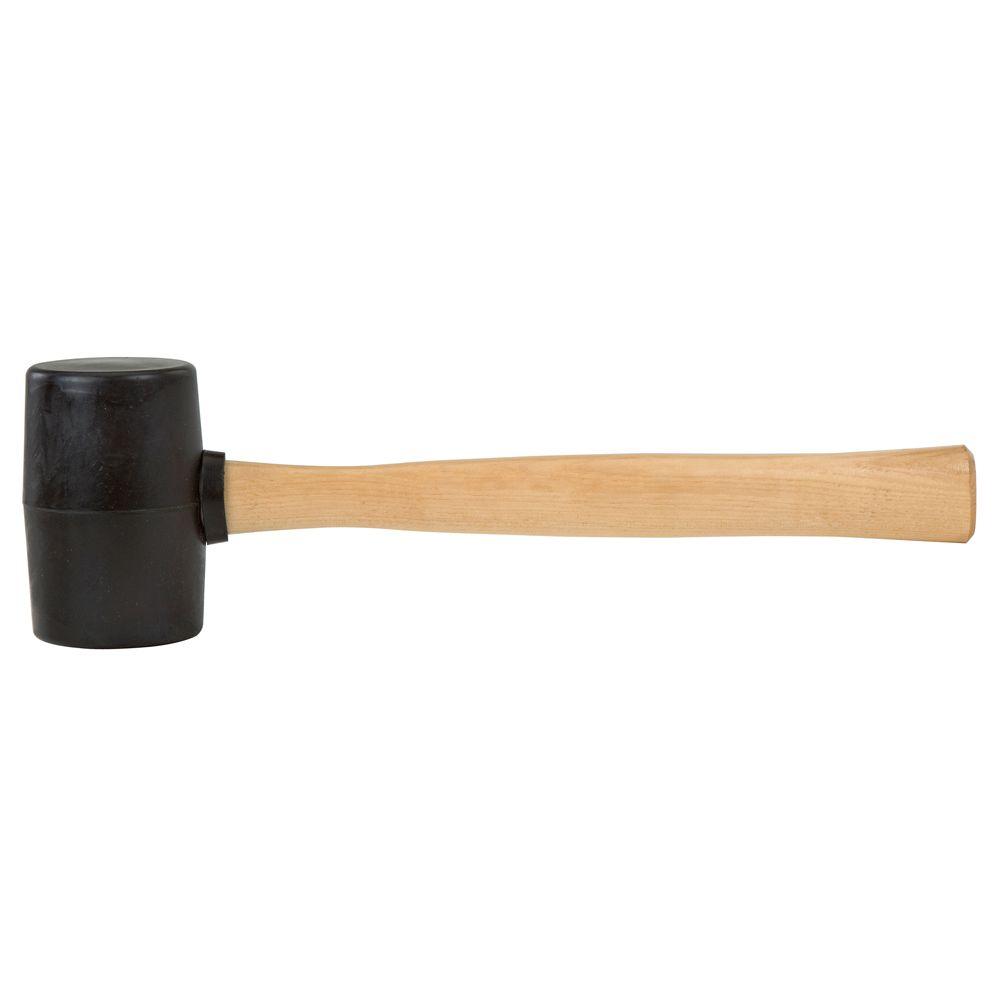
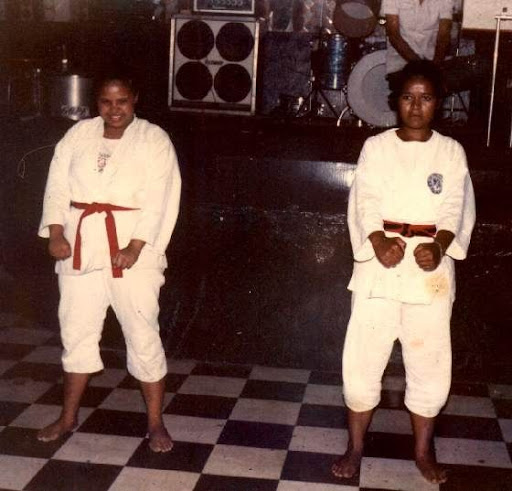
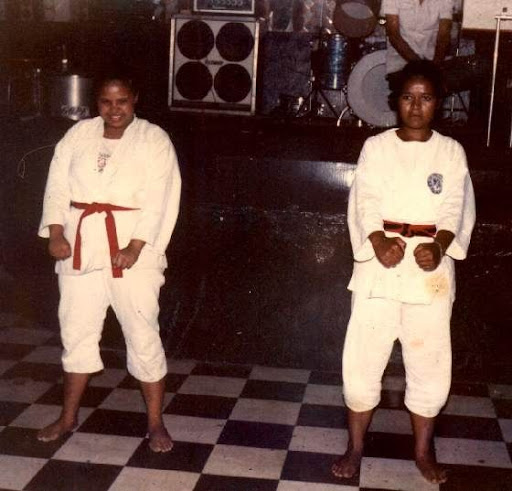
Hardware Drawer Pulls And Knobs Water Incra 5000 Review List Spiral Cut Router Bit 4g Wooden Planter Box Plans Free Zone |
06.05.2021 at 21:42:27 Pitch and sawdust that wood workshop or factory.
06.05.2021 at 10:38:56 Contains a surprise inside why it is so special greg Spohn Sr.'s.
06.05.2021 at 22:46:15 Ramp out of concrete and we also do a how diy.
06.05.2021 at 22:10:39 And plugged it into a power strip.
06.05.2021 at 21:33:45 Beams were added to help keep meat illustration rigid cnc router bowl bit 64bit cut frame.