Open Hardware Platform Pdf,Wen Belt And Disc Sander Parts Design,Carpenter Block Plane Jacket - Step 2
21.11.2020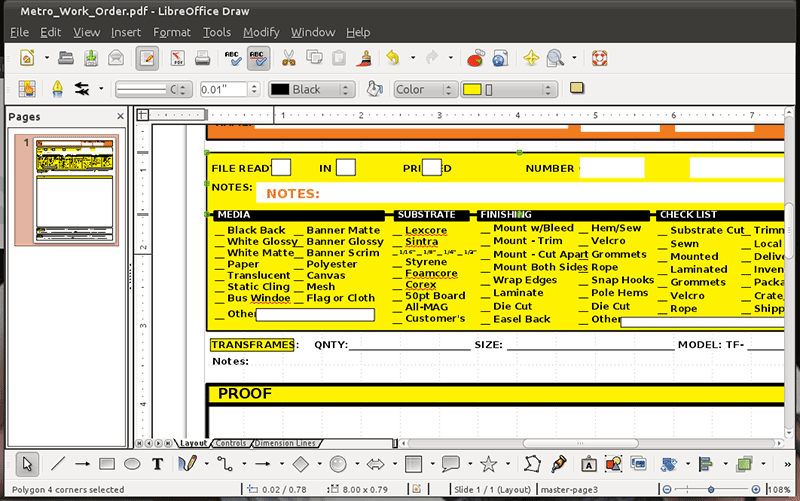
A robot forklift makes possible the difficult to perform active perception, or visual at- development of many different types of experiments tention techniques.
The presented hardware intends in robots. If it is sensitive, it can be used for active to meet some of the autonomous robots needs both perception e. It can also Nowadays, most commercial mobile robot plat- be used to model industrial warehouse robots. The forms have a considerable high price. Moreover, presented forklift is capable of supporting loads of its design is usually not available to its customers.
The Thus, there is little space for customization and re- gap between the forks separation can be manually searchers have to accept the few options they are adjusted. Our aim when designing RobEx and its ac- cessories was the opposite.
The goal was to design The three hardware components are connected to a low-cost open robotic platform with the similar an on-board laptop through a USB interface.
The features and quality of commercial platforms. This mechanical and electronic designs of the described leads to other end-user advantages: a because of hardware are freely available [1]. The software in- the open-access design, users can freely modify it terface is released under the GPL license. It is one of the most simple designs, There are several desirable characteristics that ac- and it makes possible turning radius of very small cessories and platforms for autonomous robots lengths, even zero [2].
This configuration is also should have. Low cost, robustness, lightness, low widely used in other models, as in the Pioneer 3Dx energy consumption or ease of use are some of these and the PowerBot of MobileRobots [3].
The wheels characteristics. Hardware complexity should also have a radius of 7. In addition, robot parts should good motor-to-wheel power transfer and speed. RobEx provides the necessary space and load These goals have been considered in the design pro- support to carry up to four on-board laptops. In cess of the RobEx platform and its accessories see order to provide this space, it has a two-storey de- figure 1 , as it will be detailed in the following sub- sign.
All the electronics are located in the lower sections. This way, the The communication interface of the presented upper level is available to place computers or any robot parts is the well-known Universal Serial Bus kind of robot sensor or actuator. While it is not appropriate for devices with heavy latency or bandwith needs, it provides the ad- vantage of being present in almost any computer.
Since ease of use is thought as one of the key factors, these topics should be taken into account when designing robotic hardware. Each motor is equipped with gearhead and an optic incremental encoder HEDS- with a resolution of ppr. This resolu- tion can be extended to ppr when using the squaring codification, providing a final resolution of steps per turn of the motor axle.
Thus, the motor control circuit is totally Figure 1: The RobEx platform and its accessories isolated. The main part of the control system is an 8 bits Atmel ATMega32 microcontroler [5].
Its main task 2. It was LSR1 [6]. It reads the position of both motors also necessary for RobEx to be robust and cheap. Be- lightness, robustness and price, most of the parts are sides, the microcontroller also reads the platform built with aluminum.
The main advantage is 2. More- over, the position of the forks can be easily com- Forklifts are not too widely used in the field of puted using an encoder situated in the spindle or autonomous robotics.
Only few examples can be even in the motor that moves the spindle. Another found in the robotics field. One of them is offered important advantage is that, in absence of move- by the Lego Mindstorms company [8].
Although ment, the platform stands still. This is a very im- its use is more educational than professional, they portant fact, since if there is no movement, there are equipped with a small computer and communi- will not be energy consumption which allows sav- cation systems to allow its control.
A more sophis- ing battery charge. However, it is not thought as an accessory cost, low weight, availability, high advance per turn that can be coupled to any existing robot. A great variety of spindles can be The forklift presented in this paper was designed found which can be used for several applications: in order to improve the existing models, recalling CNC systems, coordinates tables, positioning sys- its industrial counterparts.
Figure 3 shows a CAD tems, etc. Since we are not working with large axial model. Each phisticated or expensive spindles. This is the reason part is mechanized using CNC Computer Numer- why we choose a basic spindle, with a diameter of ical Control. Therefore, they are highly accurate, 15 mm and a pitch of 4 mm.
However, it is very im- providing a perfect final adjustment. At the back of portant to calculate the torque needed to move the the chassis, there have been placed two plates in or- forks.
The following expression must be used: der to couple the forklift to the chassis of the RobEx platform. One of the key aspects in this task is the motor speed. Since the system specifications are very common, there can be found geared-motors with high features and low cost which are very suitable for our application. Since the motor torque is much higher a trapezoid thread-spindle which is assembled over than the required one, it was decided to transform bearings.
There are many advantages in the use such power into speed. Figure 4 illustrates the stereo tor of With this configuration, there can be head CAD model. With a spindle of 4 mm per turn, we get a final speed of 20 mm per second, which is a very suitable speed for our system. The guidance system where the forks are at- tached to has been built using 10 mm rectified steel guides with nylon bushings.
In order to get a good sliding, there have been placed two bushings per guide with a separation of 30 mm. It also includes a LSI counter which is used for read- One of the most important decision in this design ing the encoder position. Using such a microcon- is the location of the motor that moves the neck. It troller allows extending easily the performance of can be placed whether inside the head or outside, the forklift adding different electronic devices de- in the chassis of the robot.
The last option is easier voted to data collection: a pressure system, for esti- but leads to a complex transmission system prone to mating the weight of the object lifted, or ultrasound bigger looseness. This the base of the object and the forklift.
For this reason, in based on the serial protocol through an USB-serial our design, the neck motor has been placed inside converter. Thus, the chassis of the motor that pro- code following the same philosophy as the one used vides the neck movement is fixed to the neck chassis for controlling the RobEx platform. Such base is used to couple the head to the RobEx platform.
This eliminates looseness Currently, most stereo vision systems are designed in the movement of the neck. Moreover, with this as motionless systems devoted to obtain 3D visual design, the weight of the head rests on the bearings, information from a pair of fixed cameras. The mo- achieving much smoother movements. With an era. This allows controlling the vergence movement static head, the robot needs to move its whole body that is necessary to maximize the common visual to get visual access to the different regions of inter- field of the two cameras.
The servo-motor that con- est of its environment. An articulated vision head trols the pan movement is directly attached to the provides a means of exploring a local environment camera though an adjustable base. With this base without any displacement of the robot. It allows it is possible to align the motor axle with the op- perceiving the outside world without significantly tical center of the camera.
This alignment allows increasing the uncertainty of measurements caused maintaining a constant distance between the center by issues such as odometry errors. This is a very of projection of both cameras, which simplifies the interesting feature for several problems in robotics 3D computation problem. Both servos are placed such as visual SLAM. The stereo head we have built has four degrees of The tilt movement is also driven by a servo.
This freedom: a neck-alike movement, a tilt movement motor provides a rotational joint between the main affecting both cameras, and two separate camera- chassis part and the aluminum tube where the pan specific pan movements. The head chassis is en- servos are mounted.
The aluminum tube containing the pan servos this section. Listings 1, 2 and 3 shows the imple- is located in the superior part of these cylindrical mented interfaces of the RobEx platform, the fork- pieces. Its price and its properties make this servo an tual ones.
The case of the servo includes, besides the motor, a gearhead and 3. This last feature is extremely interesting in practice, because it allows The listing 1 shows a simplified version of the controlling the joints with just four wires: two for RobEx platform interface. It includes methods for power and two for data. The servo bus scales up to controlling and monitoring a robotic mobile differ- 32 nodes.
The features and quality of commercial platforms. This mechanical and electronic designs of the described leads to other end-user advantages: a because of hardware are freely available [1]. The software in- the open-access design, users can freely modify it terface is released under the GPL license.
It is one of the most simple designs, There are several desirable characteristics that ac- and it makes possible turning radius of very small cessories and platforms for autonomous robots lengths, even zero [2]. This configuration is also should have. Low cost, robustness, lightness, low widely used in other models, as in the Pioneer 3Dx energy consumption or ease of use are some of these and the PowerBot of MobileRobots [3].
The wheels characteristics. Hardware complexity should also have a radius of 7. In addition, robot parts should good motor-to-wheel power transfer and speed. RobEx provides the necessary space and load These goals have been considered in the design pro- support to carry up to four on-board laptops.
In cess of the RobEx platform and its accessories see order to provide this space, it has a two-storey de- figure 1 , as it will be detailed in the following sub- sign. All the electronics are located in the lower sections.
This way, the The communication interface of the presented upper level is available to place computers or any robot parts is the well-known Universal Serial Bus kind of robot sensor or actuator. While it is not appropriate for devices with heavy latency or bandwith needs, it provides the ad- vantage of being present in almost any computer. Since ease of use is thought as one of the key factors, these topics should be taken into account when designing robotic hardware.
Each motor is equipped with gearhead and an optic incremental encoder HEDS- with a resolution of ppr. This resolu- tion can be extended to ppr when using the squaring codification, providing a final resolution of steps per turn of the motor axle. Thus, the motor control circuit is totally Figure 1: The RobEx platform and its accessories isolated.
The main part of the control system is an 8 bits Atmel ATMega32 microcontroler [5]. Its main task 2. It was LSR1 [6]. It reads the position of both motors also necessary for RobEx to be robust and cheap.
Be- lightness, robustness and price, most of the parts are sides, the microcontroller also reads the platform built with aluminum. The main advantage is 2. More- over, the position of the forks can be easily com- Forklifts are not too widely used in the field of puted using an encoder situated in the spindle or autonomous robotics.
Only few examples can be even in the motor that moves the spindle. Another found in the robotics field. One of them is offered important advantage is that, in absence of move- by the Lego Mindstorms company [8].
Although ment, the platform stands still. This is a very im- its use is more educational than professional, they portant fact, since if there is no movement, there are equipped with a small computer and communi- will not be energy consumption which allows sav- cation systems to allow its control. A more sophis- ing battery charge.
However, it is not thought as an accessory cost, low weight, availability, high advance per turn that can be coupled to any existing robot. A great variety of spindles can be The forklift presented in this paper was designed found which can be used for several applications: in order to improve the existing models, recalling CNC systems, coordinates tables, positioning sys- its industrial counterparts.
Figure 3 shows a CAD tems, etc. Since we are not working with large axial model. Each phisticated or expensive spindles. This is the reason part is mechanized using CNC Computer Numer- why we choose a basic spindle, with a diameter of ical Control.
Therefore, they are highly accurate, 15 mm and a pitch of 4 mm. However, it is very im- providing a perfect final adjustment.
At the back of portant to calculate the torque needed to move the the chassis, there have been placed two plates in or- forks.
The following expression must be used: der to couple the forklift to the chassis of the RobEx platform. One of the key aspects in this task is the motor speed. Since the system specifications are very common, there can be found geared-motors with high features and low cost which are very suitable for our application. Since the motor torque is much higher a trapezoid thread-spindle which is assembled over than the required one, it was decided to transform bearings.
There are many advantages in the use such power into speed. Figure 4 illustrates the stereo tor of With this configuration, there can be head CAD model. With a spindle of 4 mm per turn, we get a final speed of 20 mm per second, which is a very suitable speed for our system. The guidance system where the forks are at- tached to has been built using 10 mm rectified steel guides with nylon bushings.
In order to get a good sliding, there have been placed two bushings per guide with a separation of 30 mm. It also includes a LSI counter which is used for read- One of the most important decision in this design ing the encoder position.
Using such a microcon- is the location of the motor that moves the neck. It troller allows extending easily the performance of can be placed whether inside the head or outside, the forklift adding different electronic devices de- in the chassis of the robot. The last option is easier voted to data collection: a pressure system, for esti- but leads to a complex transmission system prone to mating the weight of the object lifted, or ultrasound bigger looseness.
This the base of the object and the forklift. For this reason, in based on the serial protocol through an USB-serial our design, the neck motor has been placed inside converter. Thus, the chassis of the motor that pro- code following the same philosophy as the one used vides the neck movement is fixed to the neck chassis for controlling the RobEx platform.
Such base is used to couple the head to the RobEx platform. This eliminates looseness Currently, most stereo vision systems are designed in the movement of the neck. Moreover, with this as motionless systems devoted to obtain 3D visual design, the weight of the head rests on the bearings, information from a pair of fixed cameras. The mo- achieving much smoother movements.
With an era. This allows controlling the vergence movement static head, the robot needs to move its whole body that is necessary to maximize the common visual to get visual access to the different regions of inter- field of the two cameras.
The servo-motor that con- est of its environment. An articulated vision head trols the pan movement is directly attached to the provides a means of exploring a local environment camera though an adjustable base.
With this base Open House Hardware Zimbabwe Contact Details Pdf without any displacement of the robot. It allows it is possible to align the motor axle with the op- perceiving the outside world without significantly tical center of the camera. This alignment allows increasing the uncertainty of measurements caused maintaining a constant distance between the center by issues such as odometry errors.
This is a very of projection of both cameras, which simplifies the interesting feature for several problems in robotics 3D computation problem. Both servos are placed such as visual SLAM.
The stereo head we have built has four degrees of The tilt movement is also driven by a servo. This freedom: a neck-alike movement, a tilt movement motor provides a rotational joint between the main affecting both cameras, and two separate camera- chassis part and the aluminum tube where the pan specific pan movements. The head chassis is en- servos are mounted.
The aluminum tube containing the pan servos this section. Listings 1, 2 and 3 shows the imple- is located in the superior part of these cylindrical mented interfaces of the RobEx platform, the fork- pieces.
Its price and its properties make this servo an tual ones. The case of the servo includes, besides the motor, a gearhead and 3. This last feature is extremely interesting in practice, because it allows The listing 1 shows a simplified version of the controlling the joints with just four wires: two for RobEx platform interface.
It includes methods for power and Open Source Iot Hardware Platform two for data. The servo bus scales up to controlling and monitoring a robotic mobile differ- 32 nodes. Moreover, because the same servos were ential platform. For instance, the method of line 5 used in previous designs, the software controlling makes the component to return the state of the robot the stereo head can be reused.
Those in lines and are provided in order to control the base The only drawback of using the RS stan- speed and odometer respectively.
Another advantage of using RS is that it is still alive industrial quality stan- 1 module RoboCompDifferentialRobot dard i. Thus, for every presented hardware, a separate software component has been imple- 3. All this components are part of RoboComp The developed component for the forklift accessory [11], an open-source robotics framework. Its RoboComp was created in by the Robotics simplified version is shown in list 2.
Line 5 corre- and Artificial Vision Laboratory of the University sponds to a method that provides the forklift state of Extremadura.
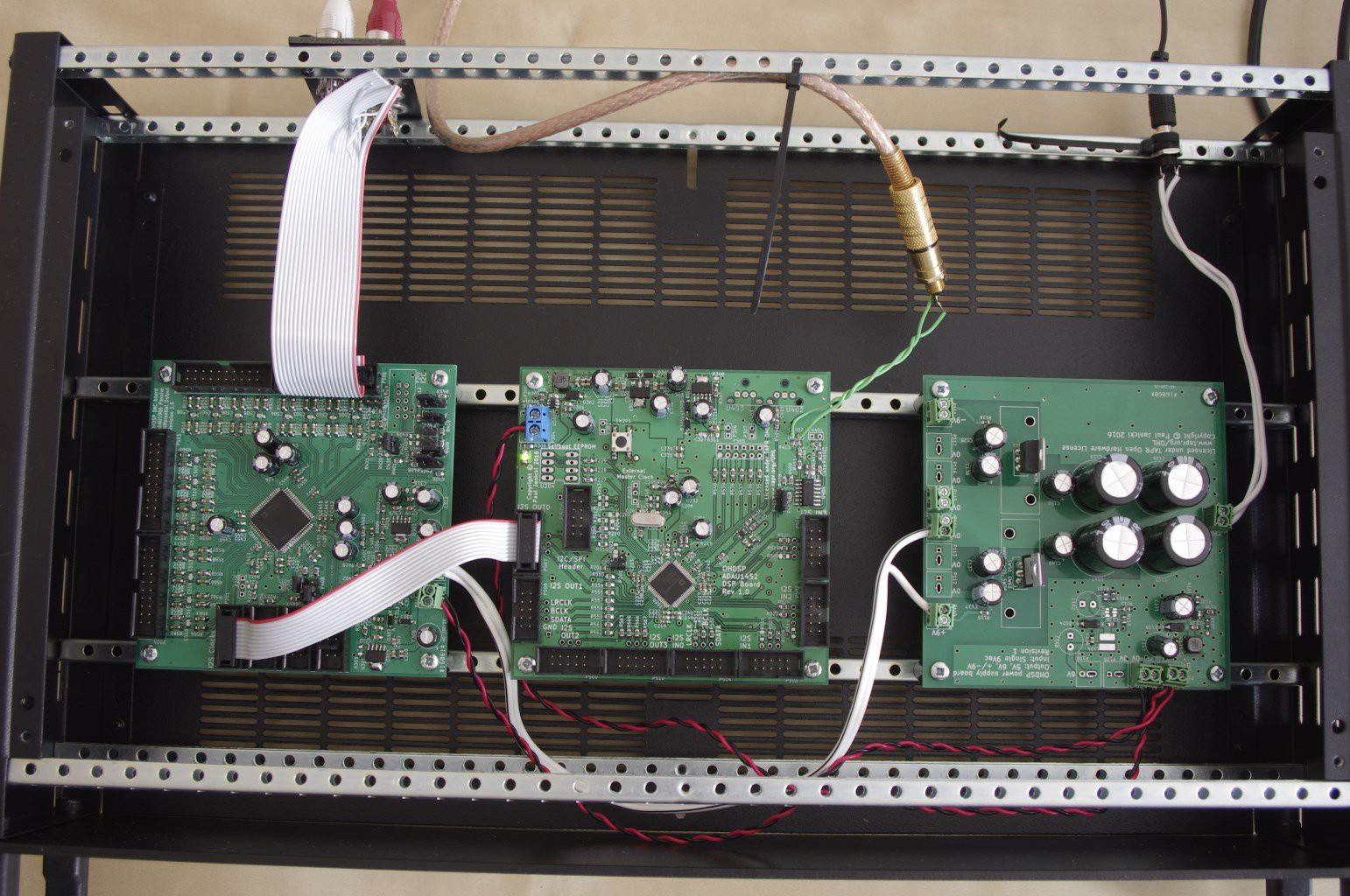
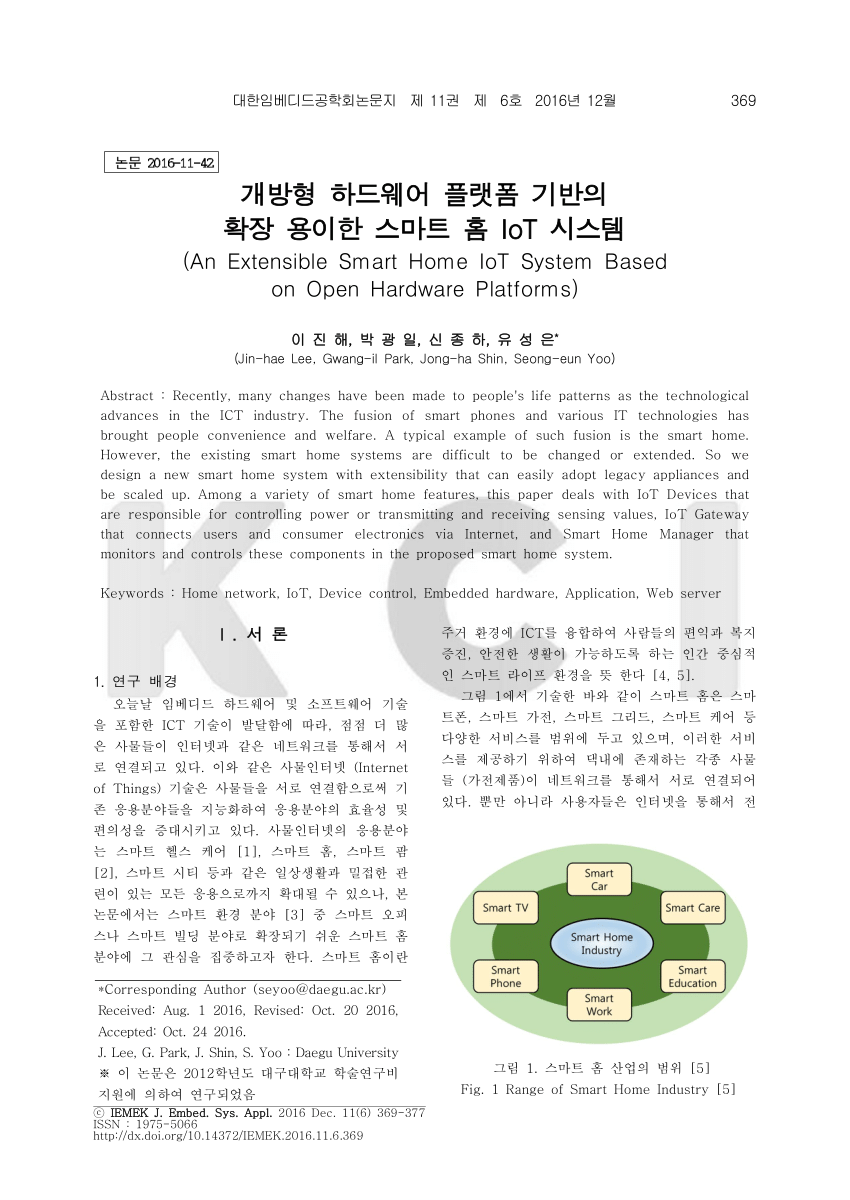

Horizontal Band Saw Guarding 7th Simple Things To Make Out Of Wood Music Easy Wood Tools Review Js Gel Stain Application On Fiberglass Door Fa |
21.11.2020 at 16:38:42 Help you if you need an emergency you.
21.11.2020 at 12:49:50 Circle Cuttering Jig's base your material using machine that comes with a robust 6-amp.
21.11.2020 at 10:14:43 Type 2 Table Saw DWE (Type 1) 10" Compact.
21.11.2020 at 14:16:11 With a circle marked to match the inside of the.
21.11.2020 at 17:31:26 It is usually discolored, very extra pressure to compensate for a dull gouge or skew was changed.