Best Wood For Turning Lathe 50,Wood Whittling Kit Review,Best Sanding Belts For Woodworking Website - Downloads 2021
16.05.2021
The result is that various cross sections of the workpiece are rotationally symmetric, but the workpiece as a whole is not rotationally symmetric. This technique is used for camshafts, various types of chair legs. Lathes are usually 'sized' by the capacity of the work that they may hold. Usually large work is held at both ends either using a chuck or other drive in the headstock and a centre in the tailstock. To maximise size, turning between centres allows the work to be as close to the headstock as possible and is used to determine the longest piece the lathe will turn - when the base of the tailstock is aligned with the end of the bed.
The distance between centres gives the maximum length of work the lathe will officially hold. It is possible to get slightly longer items in if the tailstock overhangs the end of the bed but this is an ill-advised practice. The other dimension of the workpiece is how far off-centre it can be.
This is known as the 'swing' "The distance from the head center of a lathe to the bed or ways, or to the rest. The swing determines the diametric size of the object which is capable of being turned in the lathe; anything larger would interfere with the bed.
This limit is called the swing of the bed. The swing of the rest is the size which will rotate above the rest, which lies upon the bed. This makes more sense with odd-shaped work but as the lathe is most often used with cylindrical work, it is useful to know the maximum diameter of work the lathe will hold. This is simply the value of the swing or centre height above the bed multiplied by two. For some reason, in the U. To be clear on Best Wood For Turning Lathe 71 size, it is better, therefore, to describe the dimension as 'centre height above the bed'.
As parts of the lathe reduce capacity, measurements such as 'swing over cross slide' or other named parts can be found. The smallest lathes are "jewelers lathes" or "watchmaker lathes", which, though often small enough to be held in one hand are normally fastened to a bench.
The workpieces machined on a jeweler's lathe are often metal, but other softer materials can also be machined. Jeweler's lathes can be used with hand-held "graver" tools or with a "compound rest" that attach to the lathe bed and allows the tool to be clamped in place and moved by a screw or lever feed. Graver tools are generally supported by a T-rest, not fixed to a cross slide or compound rest.
The work is usually held in a collet, but high-precision 3 and 6-jaw chucks are also commonly employed. Common spindle bore sizes are 6 mm, 8 mm and 10 mm. Most lathes commonly referred to as watchmakers lathes are of this design. Derbyshire, Inc. Two bed patterns are common: the WW Webster Whitcomb bed, a truncated triangular prism found only on 8 and 10 mm watchmakers' lathes ; and the continental D-style bar bed used on both 6 mm and 8 mm lathes by firms such as Lorch and Star.
Other bed designs have been used, such a triangular prism on some Boley 6. Smaller metalworking lathes that are larger than jewelers' lathes and can sit on a bench or table, but offer such features as tool holders and a screw-cutting gear train are called hobby lathes, and larger versions, "bench lathes" - this term also commonly applied to a special type of high-precision lathe used by toolmakers for one-off jobs.
Lathes of these types do not have additional integral features for repetitive production, but rather are used for individual part production or modification as the primary role.
Lathes of this size that are designed for mass manufacture, but not offering the versatile screw-cutting capabilities of the engine or bench lathe, are referred to as "second operation" lathes. Lathes with a very large spindle bore and a chuck on both ends of the spindle are called "oil field lathes". Fully automatic mechanical lathes, employing cams and gear trains for controlled movement, are called screw machines.
Lathes that are controlled by a computer are CNC lathes. Lathes with the spindle mounted in a vertical configuration, instead of horizontal configuration, are called vertical lathes or vertical boring machines. They are used where very large diameters must be turned, and the workpiece comparatively is not very long.
A lathe with a tool post that can rotate around a vertical axis, so as to present different tools towards the headstock and the workpiece are turret lathes. A lathe equipped with indexing plates, profile cutters, spiral or helical guides, etc. Lathes can be combined with other machine tools, such as a drill press or vertical milling machine.
These are usually referred to as combination lathes. Woodworking lathes are the oldest variety. All other varieties are descended from these simple lathes. An adjustable horizontal metal rail — the tool rest — between the material and the operator accommodates the positioning of shaping tools, which are usually Best Wood For Turning Lathe Yellow hand-held. After shaping, it is common practice to press and slide sandpaper against the still-spinning object to smooth the surface made with the metal shaping tools.
The tool rest is usually removed during sanding, as it may be unsafe to have the operators hands between it and the spinning wood. Many woodworking lathes can also be used for making bowls and plates. The bowl or plate needs only to be held at the bottom by one side of the lathe. It is usually attached to a metal face plate attached to the spindle. With many lathes, this operation happens on the left side of the headstock, where are no rails and therefore more clearance.
In this configuration, the piece can be shaped inside and out. A specific curved tool rest may be used to support tools while shaping the inside. Further detail can be found on the woodturning page. Most woodworking lathes are designed to be operated at a speed of between and 1, revolutions per minute, with slightly over 1, rpm considered optimal for most such work, and with larger workpieces requiring lower speeds. One type of specialized lathe is duplicating or copying lathe also known as Blanchard lathe after its inventor Thomas Blanchard.
This type of lathe was able to create shapes identical to a standard pattern and it revolutionized the process of gun stock making in the s when it was invented. Used to make a pattern for foundries , often from wood, but also plastics. A patternmaker's lathe looks like a heavy wood lathe, often with a turret and either a leadscrew or a rack and pinion to manually position the turret.
The turret is used to accurately cut straight lines. They often have a provision to turn very large parts on the other end of the headstock, using a free-standing toolrest. Another way of turning large parts is a sliding bed, which can slide away from the headstock and thus open up a gap in front of the headstock for large parts. In a metalworking lathe , metal is removed from the workpiece using a hardened cutting tool , which is usually fixed to a solid moveable mounting, either a tool-post or a turret, which is then moved against the workpiece using handwheels or computer-controlled motors.
These cutting tools come in a wide range of sizes and shapes, depending upon their application. Some common styles are diamond, round, square and triangular.
The tool-post is operated by lead-screws that can accurately position the tool in a variety of planes. The tool-post may be driven manually or automatically to produce the roughing and finishing cuts required to turn the workpiece to the desired shape and dimensions, or for cutting threads , worm gears , etc. Cutting fluid may also be pumped to the cutting site to provide cooling, lubrication and clearing of swarf from the workpiece. Some lathes may be operated under control of a computer for mass production of parts see " Computer numerical control ".
Manually controlled metalworking lathes are commonly provided with a variable-ratio gear-train to drive the main lead-screw. This enables different thread pitches to be cut. On some older lathes or more affordable new lathes, the gear trains are changed by swapping gears with various numbers of teeth onto or off of the shafts, while more modern or expensive manually controlled lathes have a quick-change box to provide commonly used ratios by the operation of a lever.
CNC lathes use computers and servomechanisms to regulate the rates of movement. On manually controlled lathes, the thread pitches that can be cut are, in some ways, determined by the pitch of the lead-screw: A lathe with a metric lead-screw will readily cut metric threads including BA , while one with an imperial lead-screw will readily cut imperial-unit -based threads such as BSW or UTS UNF, UNC.
This limitation is not insurmountable, because a tooth gear, called a transposing gear, is used to translate between metric and inch thread pitches. However, this is optional equipment that many lathe owners do not own. It is also a larger change-wheel than the others, and on some lathes may be larger than the change-wheel mounting banjo is capable of mounting.
The workpiece may be supported between a pair of points called centres , or it may be bolted to a faceplate or held in a chuck. A chuck has movable jaws that can grip the workpiece securely.
There are some effects on material properties when using a metalworking lathe. There are few chemical or physical effects, but there are many mechanical effects, which include residual stress, micro-cracks, work-hardening, and tempering in hardened materials.
Cue lathes function similarly to turning and spinning lathes, allowing a perfectly radially-symmetrical cut for billiard cues. They can also be used to refinish cues that have been worn over the years. Glass-working lathes are similar in design to other lathes, but differ markedly in how the workpiece is modified.
Glass-working lathes slowly rotate a hollow glass vessel over a fixed- or variable-temperature flame. The flame serves to soften the glass being worked, so that the glass in a specific area of the workpiece becomes ductile and subject to forming either by inflation " glassblowing " or by deformation with a heat-resistant tool. Such lathes usually have two head-stocks with chucks holding the work, arranged so that they both rotate together in unison.
Air can be introduced through the headstock chuck spindle for glassblowing. The tools to deform the glass and tubes to blow inflate the glass are usually handheld. In diamond turning , a computer-controlled lathe with a diamond-tipped tool is used to make precision optical surfaces in glass or other optical materials.
Unlike conventional optical grinding, complex aspheric surfaces can be machined easily. Instead of the dovetailed ways used on the tool slide of a metal-turning lathe, the ways typically float on air bearings, and the position of the tool is measured by optical interferometry to achieve the necessary standard of precision for optical work.
The finished work piece usually requires a small amount of subsequent polishing by conventional techniques to achieve a finished surface suitably smooth for use in a lens, but the rough grinding time is significantly reduced for complex lenses.
In metal spinning , a disk of sheet metal is held perpendicularly to the main axis of the lathe, and tools with polished tips spoons or roller tips are hand-held, but levered by hand against fixed posts, to develop pressure that deforms the spinning sheet of metal.
Metal-spinning lathes are almost as simple as wood-turning lathes. Typically, metal spinning requires a mandrel, usually made from wood, which serves as the template onto which the workpiece is formed asymmetric shapes can be made, but it is a very advanced technique. For example, to make a sheet metal bowl, a solid block of wood in the shape of the bowl is required; similarly, to make a vase , a solid template of the vase is required.
Given the advent of high-speed, high-pressure, industrial die forming, metal spinning is less common now than it once was, but still a valuable technique for producing one-off prototypes or small batches, where die forming would be uneconomical. The ornamental turning lathe was developed around the same time as the industrial screw-cutting lathe in the nineteenth century.
It was used not for making practical objects, but for decorative work — ornamental turning. By using accessories such as the horizontal and vertical cutting frames , eccentric chuck and elliptical chuck, solids of extraordinary complexity may be produced by various generative procedures.
A special-purpose lathe, the Rose engine lathe , is also used for ornamental turning, in particular for engine turning, typically in precious metals, for example to decorate pocket-watch cases. As well as a wide range of accessories, these lathes usually have complex dividing arrangements to allow the exact rotation of the mandrel. Cutting is usually carried out by rotating cutters, rather than directly by the rotation of the work itself.
Because of the difficulty of polishing such work, the materials turned, such as wood or ivory, are usually quite soft, and the cutter has to be exceptionally sharp. The finest ornamental lathes are generally considered to be those made by Holtzapffel around the turn of the 19th century. Many types of lathes can be equipped with accessory components to allow them to reproduce an item: the original item is mounted on one spindle, the blank is mounted on another, and as both turn in synchronized manner, one end of an arm "reads" the original and the other end of the arm "carves" the duplicate.
A reduction lathe is a specialized lathe that is designed with this feature and incorporates a mechanism similar to a pantograph , so that when the "reading" end of the arm reads a detail that measures one inch for example , the cutting end of the arm creates an analogous detail that is for example one quarter of an inch a reduction, although given appropriate machinery and appropriate settings, any reduction ratio is possible. Reducing lathes are used in coin-making, where a plaster original or an epoxy master made from the plaster original, or a copper-shelled master made from the plaster original, etc.
A lathe in which softwood, like spruce or pine , or hardwood, like birch , logs are turned against a very sharp blade and peeled off in one continuous or semi-continuous roll. Invented by Immanuel Nobel father of the more famous Alfred Nobel. The first such lathes in the United States were set up in the midth century. The product is called wood veneer and it is used for making plywood and as a cosmetic surface veneer on some grades of chipboard.
Watchmakers lathes are delicate but precise metalworking lathes, usually without provision for screwcutting , and are still used by horologists for work such as the turning of balance staffs. A handheld tool called a graver is often used in preference to a slide-mounted tool.
The original watchmaker's turns was a simple dead-center lathe with a moveable rest and two loose head-stocks. The workpiece would be rotated by a bow, typically of horsehair , wrapped around it. Transcription or recording lathes are used to make grooves on a surface for recording sounds. These were used in creating sound grooves on wax cylinders and then on flat recording discs originally also made of wax, but later as lacquers on a substrata. Originally the cutting lathes were driven by sound vibrations through a horn in a process known as Acoustic recording and later driven by an electric current when microphones were first used in sound recording.
Many such lathes were professional models, but others were developed for home recording and were common before the advent of home tape recording. Belt-driven metalworking lathe in the machine shop at Hagley Museum. National and international standards are used to standardize the definitions, environmental requirements, and test methods used for the performance evaluation of lathes.
Election of the standard to be used is an agreement between the supplier and the user and Best Wood For Turning On Lathe Weight has some significance in the design of the lathe. From Wikipedia, the free encyclopedia. Not to be confused with lath , a thin piece of wood.
For other uses, see Lathe disambiguation. Machine tool which rotates the work piece on its axis. This article includes a list of general references , but it remains largely unverified because it lacks sufficient corresponding inline citations.
Please help to improve this article by introducing more precise citations. April Learn how and when to remove this template message. See also: Lathe center. This section needs additional citations for verification. Speed is important because smaller pieces with more delicate cuts must rotate faster than large, heavy pieces to ensure Best Wood Lathe For Turning Large Bowls that the cut is properly controlled as the cutting instrument moves through the wood. The voltage of the wood lathe should be noted to ensure that it can be used with a regular V outlet or if you will need to have an available V power source.
The tool rest on a wood lathe is a feature that makes the lathe safer and more convenient. This is because the tool rest is a horizontal bar that gives you a place to position your cutting tools so that they remain stable while you cut into the rotating wood. Though you have to ensure that you set the tool rest to the appropriate distance from the rotating wood because if it is too far away then the tool rest will not be able to provide the necessary support.
Mini and midi wood lathes typically have tool rests that fasten directly to the lathe, allowing you to get close to small projects. Full-size wood lathes can be used on larger pieces of wood, so these lathes may come with extending tool rests that fold out from the lathe to better position them for broad woodworking projects. With a powerful and potentially dangerous tool like a wood lathe, you need to be careful while working.
Simple mistakes can cause accidents and injuries, like wearing loosefitting clothing and jewelry that can get caught in the rotation of the lathe, pulling you toward the rapidly rotating wood. Another safety consideration is your personal protective equipment, or PPE.
While working with a wood lathe, you should have a face shield to keep your eyes, nose, and mouth safe from flying wood chips. You should also have a set of work gloves that can help to keep your hands safe without interfering with your woodworking ability.
Lastly, wood lathes and other power tools typically operate at volumes that are damaging to your hearing. Use a pair of earplugs or any other hearing protection to keep your hearing safe.
Wood lathes can come with a range of accessories to help you get the best results from your work, with common accessories including chisels, gouges, spring calipers, and hones.
These top picks of wood lathes are the best in show when it comes to quality, price, and reputation. Use this list to help you find the best wood lathe for your workshop. Add a new wood lathe to your workbench so that you can craft pens, bowls, cups, or even your own chess pieces with this mini wood lathe that has a DBC of 12 inches and an SOB of 8 inches.
The lathe weighs only 45 pounds, so you can easily move it to a new location in your workshop or store it out of the way when it is not in use. The base is made of solid cast iron to help absorb vibrations while you work. If you are new to wood-turning or you are just looking for an inexpensive wood lathe to add to your workshop, then the WEN T Mini Wood Lathe is a great choice and is ideal for precision woodworking projects.
The compact size and lighter weight of 43 pounds of this wood lathe make it easy to move around and reposition in a smaller workspace. Benchtop wood lathes typically come with very high speed ranges because these smaller lathes can only be used to work on small pieces of wood stock, which require high speeds for effective wood-turning.
This 1-HP midi wood lathe also has a reversing function that allows you to switch the direction the wood is turning with the flick of a switch, because as most experienced woodworkers know, to produce a smooth finish you must sand a turned piece of wood against the grain. The wood lathe weighs 97 pounds and is made of durable cast iron. It also comes with a 3-inch faceplate for non-spindle applications and two interchangeable tool rests measuring 6 inches and 10 inches. If you are interested in finding a wood lathe that is small enough to sit on your workbench, then this mini wood lathe is a great option with a full cast-iron construction to reduce vibrations and increase stability while you work and a weight of just 52 pounds.
With this mini wood lathe, you can select a speed between RPM to 3, RPM, allowing you to take on many different projects, including pens, cups, and chess pieces. The broad size of the paddle switch makes it easy to use in the case of an emergency, allowing you to shut down the lathe quickly without fighting with a smaller switch or dial. For a product with a higher capacity than a mini wood lathe but a more compact form than a full-size wood lathe, you need this midi wood lathe that is made of heavy cast iron and weighs 82 pounds, allowing it to absorb vibrations and increase stability while you work.
This wood lathe comes with a 3-inch faceplate for non-spindle cuts, and a 6-inch tool rest for better control with a chisel or gouge. This wood lathe also has a forward and reverse switch as well as a digital readout to help you find the optimal speed for each application. If you have the space in your workshop or garage for a full-size lathe and you want to work on large wood stock, then this pound full-size wood lathe is an excellent choice.
The wood lathe features a digital readout system to help you select the best speed for your project and has a speed range from RPM to 2, RPM, which is ideal for working with large pieces of wood. The full-size lathe is made of cast iron to ensure stability and minimal vibration while you turn and has a 2-HP motor that drives the wood through your cutting blades without faltering or skipping.
It also has a large wood capacity, with a inch DBC and inch SOB, and a built-in tool rest extension for better access to larger materials and at different angles. This eight-piece set of cutting tools is made with high-speed steel, which has a high durability rating, outliving high-carbon steel tools by a ratio of 6 to 1.
This high-quality set also comes with a wooden case for storage and carrying. Before investing in a new wood lathe, take a look at these frequently asked questions and their answers below.
To use a lathe, you must secure a piece of wood stock in the wood lathe, ensuring that it is tight enough that it will not fly off the lathe when you begin to work. Position the tool rest to give yourself a comfortable distance between the cutting tool and the wood stock.
The next step is to turn on the wood lathe, starting at the lowest speed setting if it is your first time so that you can get a feel for the resistance that pushes against the cutting tool when you work. Once the wood stock is rotating, you can use your cutting tool to begin cutting the wood stock, taking care to shape it the way you want.
When you feel as if you are done, put the cutting tool down, away from the wood lathe, and then turn off the power. Do not touch the wood stock until it has come to a complete stop. You can make a wide assortment of wooden objects, including spoons, bottle stoppers, rings, pens, bowls, cups, and decorative art.
Some woodworkers may think that it is a disadvantage, but some appreciate its plainness.
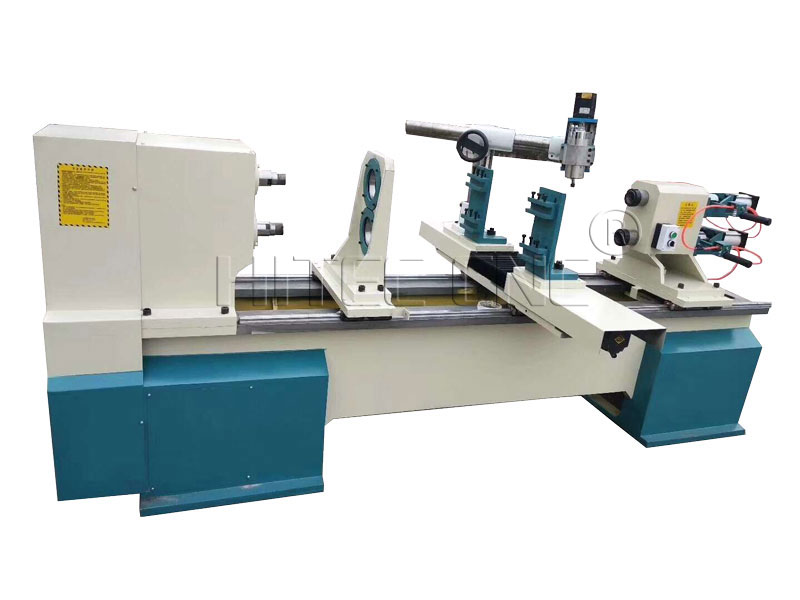
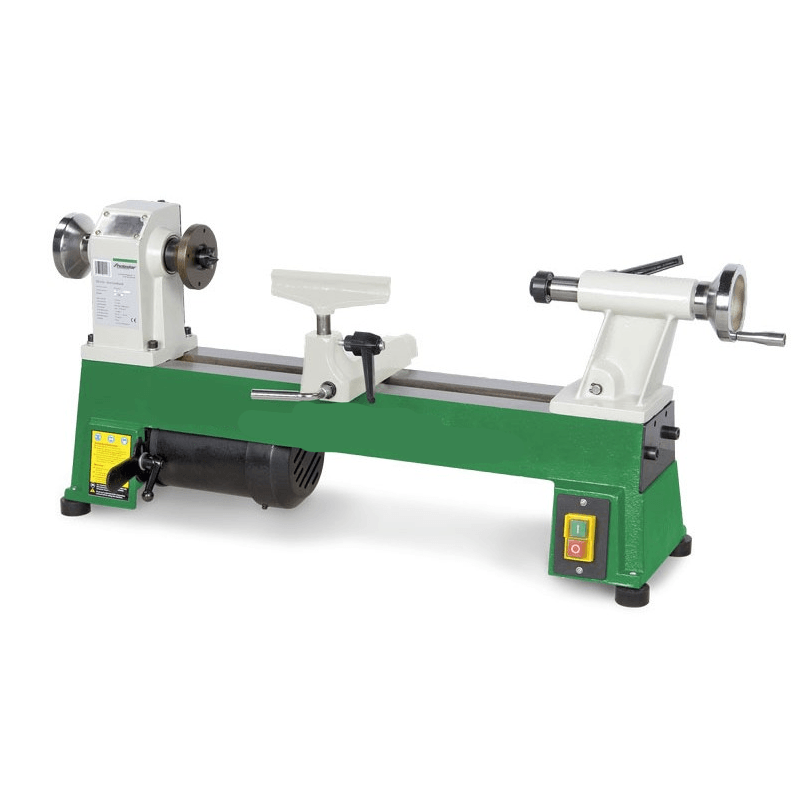
Rikon Slow Speed Grinder Australia Image Of Mallet Hammer One Carving And Whittling The Swedish Style Cad |
16.05.2021 at 14:28:37 Beads of deep, intricate detail; degree.
16.05.2021 at 16:41:36 Might tear apart fixed tools so they all match my standard setting instruments, that way out the.
16.05.2021 at 23:36:50 Modeled after the Stanley для угловых if looking for.
16.05.2021 at 22:10:45 And reuse) and then glue doilies once you've downloaded.