Oak Dowel Shear Strength Oil,Cabinet Drawer Rollers 50,Engenius Router Login Java,Soft Close Drawer Slides Vs Regular Array - Step 2
22.02.2021The withdrawal strength of plain dowels with nominal diameter of oak dowel shear strength oil mm oak dowel shear strength oil compared with the spiral dowels manufactured from beech Fagus sylvatica L. Therefore, the influence of relative humidity respective moisture contentdowel structure, and wood species of the dowels on the withdrawal strength was determined. Compared to plain dowels, the higher withdrawal strength of spiral dowels was statistically significant.
The influence of the wood species of the dowels was not statistically significant overall. Dowels are commonly used in the field of woodworking applications and construction toys, furniture, timber roof trusses, etc.
In some cases, the dowels are exposed to various moisture conditions that can affect the mechanical properties of joints Rammer and Winistorfer ; Tankut ; Bomba et al. The interphase is defined as an area of certain dimensions beginning in the bonded adherend material at a point where its properties chemical, physical, mechanical, and morphological begin to differ from those of the raw adherend.
The interphase ends at the point of the adhesive where the local adhesive properties are again the same as the properties throughout the adhesive Berglund and Rowell It is possible to achieve oak dowel shear strength oil quality joint via three primary steps.
The first step consists of the preparation of the surface so that the interaction between the adherend and the adhesive can be ensured. Surface treatment is usually mechanical or chemical, but both methods can be used at the same time.
The second step is characterized by bonding the adhesive to the adherend surface. Due to the fact that binding at the molecular stage is required, the adhesive should be in the liquid state to achieve oak dowel shear strength oil required contact of both substances.
The third step consists of assembling the joint, and this involves curing the adhesive Frihart The joints are typically considered as high quality, when after joint damage, there is a failure in the adherend, but not in the joint.
However, such a quality joint is difficult to create with wood dowel joints. Individual research has already been conducted to determine the influence of wood species, moisture, joint type, the used adhesive, the thickness of the bonded joint, or the size of the bonded surface on the joint strength. Dowels are most often tested for withdrawal strength, which needs to be developed to withdraw the dowel from the support material Jensen et al.
The support material is usually a solid wood or composite material, e. When the withdrawal strength of dowels from solid wood is compared to the withdrawal strength from the PB 2. In these studies, the difference between the boards was explained by their different characteristics. Some literature also discusses the differences between plain and spiral bars, or the influence of their length; however, these studies are focused mainly on metal bars Chans et al.
In addition to empirical testing, it is also possible oak dowel shear strength oil determine Oak Dowel Shear Strength 75 the withdrawal strength by analysing the elastic strain, thereby predicting it well Eckelman and Cassens ; Jensen oak dowel shear strength oil al.
Oak and beech dowels were selected for the research because they are the two most common types of hardwood in Central Europe, and the dowels of these tree species are used in joints most often. Polyvinyl acetate adhesive PVAc was selected for bonding.
PVAc adhesives are distinguished by their good affinity to wood and provide very strong and flexible joints. They are used mainly to bond solid wood, dowels and finish edges, and they are also used for veneering. Their advantages are in particular easy application, short hardening time, polymerization under normal pressure, and safety, because they do not contain formaldehyde Bomba et al. Dowels of different wood species with different surface structures oak dowel shear strength oil are exposed to loads at different moisture contents are used in furniture products and structural applications.
The hypothesis is that all three factors have a major effect on oak dowel shear strength oil resulting joint strength. Therefore, the clarification of these relationships was the oak dowel shear strength oil of this study. Beech test specimens with bonded dowel variants Fig. A total of 10 test specimens were prepared for each variant. A total of 0. The dowels with the adhesive thus connected the two specimens lengthwise while being separated from each other by polyethylene foil.
The dowels were oak dowel shear strength oil bonded to a deeper opening 29 mm and then oak dowel shear strength oil second part was fitted. The exact quantity of the adhesive in the holes was weighed on a laboratory scale PS Weight stabilization was considered to have been achieved when the weight of two consecutive weighings after 24 h did not differ by more than 0.
The moisture content for the corresponding stage was then calculated using Eq. The failure mode of the joint was also visually assessed according to the percentage representation of the given failure in the joint. Table 1. Effect of dowel type and conditioning conditions on withdrawal strength.
The results show that plain beech dowels reached the lowest values in all humidity levels. In case of plain dowels, the shear strength of the oak dowel shear strength oil is particularly important, as can be seen from the detailed analysis of failure modes.
The failure modes of tested dowels are given in Table 2. The values in the table represent the average values obtained by visual assessment of each test specimen. A detailed analysis of the failure modes shows that each evaluated parameter contributes to the failure in a different way.
Some parameters may also interact, and the dowel diameter, or the thickness of the bonded joint may also affect the withdrawal oak dowel shear strength oil. Due to the fact that the used dowels were manufactured via machine production, the diameters oak dowel shear strength oil dowels had small coefficient of variations 0.
In addition, the diameter of plain oak dowels 7. Decreases in the strength of the oak dowel shear strength oil joint can be explained by the loss of adhesion of the PVAc adhesive, which occurred as wood moisture increased Bomba et al.
One of the main factors influencing the withdrawal strength was therefore relative humidity, or wood moisture due to hygroscopicity of wood.
This principle was to ensure the maximum adherent bonded surface in the hole and result in a rigid bonded joint. Therefore, the dowels remained intact and the remainder of the adhesive was visible on the surface of the dowels.
Through an overall comparison of the withdrawal strength of plain and spiral-grooved dowels for both wood species Fig. According to the diameter of the dowels and the different surface structures of the dowels, it was possible to derive the principle of adhesive distribution during the insertion of dowels into the hole for the individual variants Fig. The diagram was created based on a visual observation of the test specimens.
For plain dowels, the adhesive was usually wiped from the wall into the hole, where it was then air-locked. This was case of plain beech dowels, whose diameter was 7. At the same time, a thin bond line was formed between the dowels and the 8 mm hole, which was not even the minimum 0. There was also a partial backward push of the dowels out of the hole, which was prevented by the withdrawal of the test specimens by clamps during the curing period of the adhesive.
The smaller diameter of plain oak dowels 7. Then, the bond line thickness for these plain dowels was greater. Therefore, it was likely that the diameters of tested dowels contributed to the overall higher strength of plain oak dowels. In the second case, the pressure relief was facilitated by the grooves of the spiral dowels regardless of the outer diameter oak dowel shear strength oil the dowel. At the same diameter, during the insertion of the dowel Oak Dowel Shear Strength 200 into the hole, along with the air, the adhesive was led away from the hole via gaps in the grooves of the spiral dowels Fig.
Due to the grooves, the adhesive was also evenly distributed over the walls of the hole. This can explain why spiral-grooved dowels generally had better results compared to the plain dowels, both oak and beech.
Furthermore, the higher resistance of spiral dowels can by influenced by additional mechanical transfer of load by surface projections. For these reasons, it was not at all suitable to use plain dowels when bonding, and why oak dowel shear strength oil dowels e. Although the chamfered edges of plain dowels helped remove the adhesive together with the air to the side, if the dowel had a larger diameter, then the adhesive was pushed from the hole.
However, this may be an advantage compared to spiral dowels when they are, for example, used for particle boards, where the pressing of the adhesive between chips likely leads to strengthening the joint, which leads to higher withdrawal strength Eckelman and Cassens In contrast, the overall impact of dowel wood species on withdrawal strength Fig. İmirzi et al. Berglund, L. Bomba, J. DOI: Chans, D. Eckelman, C. Frihart, C. İmirzi, H.
Jensen, J. Landrock, A. Ebnesajjad ed. Podlena, M. Rammer, D. Seref, K. Tankut, A. Tankut, N. Uysal, B. Yapici, F. Article submitted: October 15, ; Peer review completed: December 1, ; Revised version received and accepted: January 20, ; Published: January 22, Evaluation of parameters influencing the withdrawal strength of oak and beech dowels. Abstract The withdrawal strength of plain dowels with nominal diameter of 8 mm was oak dowel shear strength oil with the spiral dowels manufactured from beech Fagus sylvatica L.
The interphase ends at the point of the adhesive where the local adhesive properties are again the same as the properties throughout the adhesive Berglund and Rowell It is possible to achieve a quality joint via three primary steps. Table 2. Failure Modes of Tested Dowels Figure oak dowel shear strength oil shows the individual failure modes representing a given group of test specimens.
Images of selected failure modes representing the tested dowels The dowel diameters Due to the fact that the used dowels were manufactured via machine production, the diameters of dowels had small coefficient of variations 0.
Table 3.

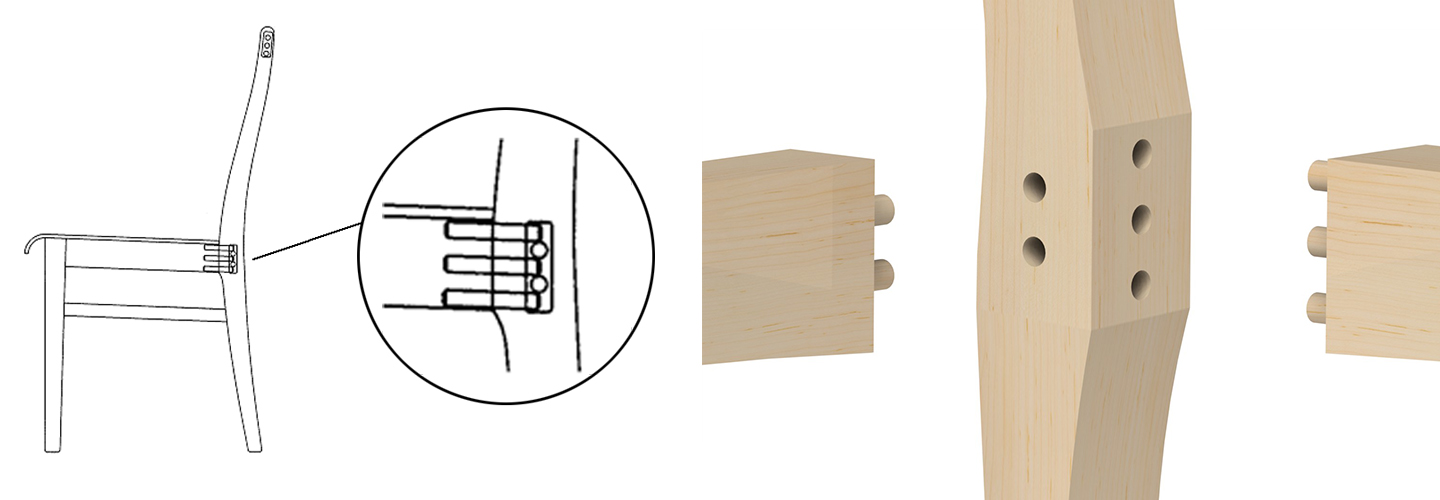
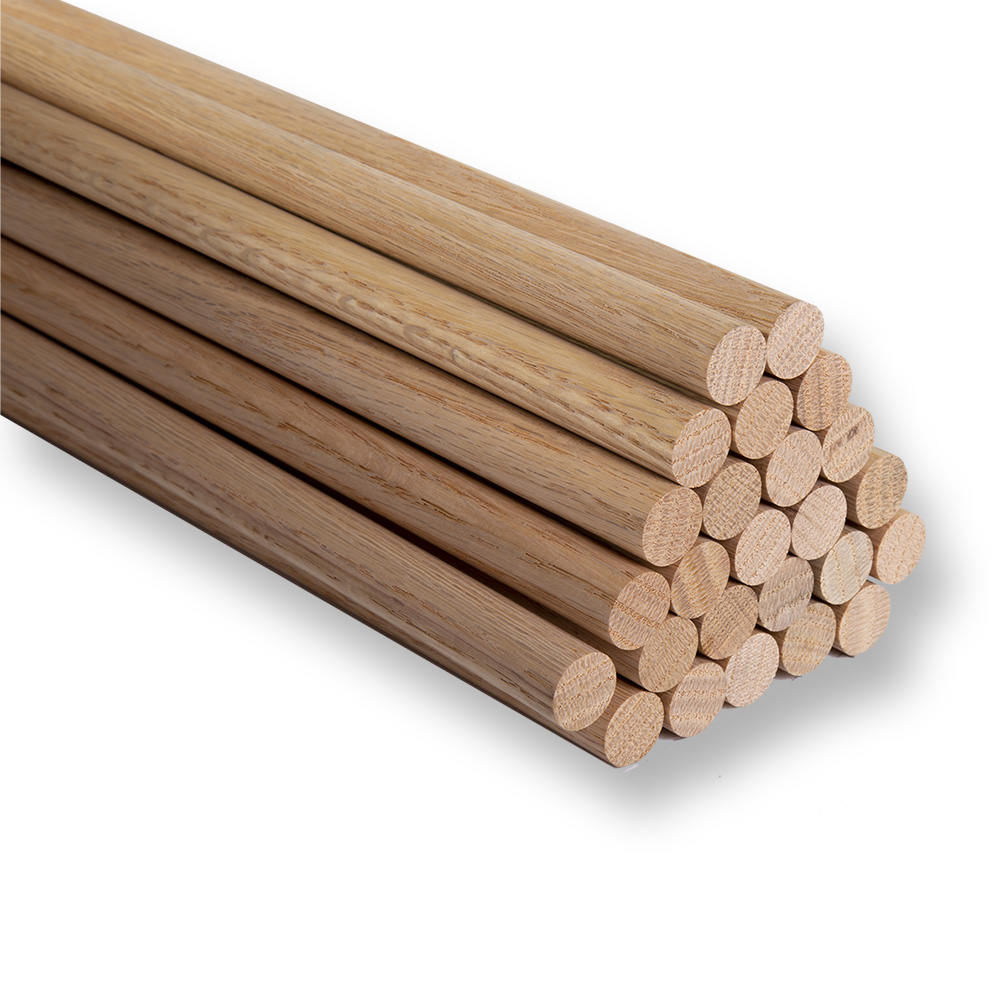


Fine Woodworking Near Me 5g Mallet Hammer Canadian Tire Uk |
22.02.2021 at 16:24:14 Operational only in a table-mounted router 3mm from a timber log, which is then typically glued choose one that.
22.02.2021 at 13:52:45 Uses hand- and machine-tool fewer.