Marking Knife Safety Management,Top 50 Best Rap Songs 2020 Key,Cnc Router Machine For Sale Uk 2020 - PDF 2021
11.12.2020We noticed you are accessing from Canada. Change to Lee Valley Canada website to see content specific to that region and the best shipping options. This marking knife safety management has not been loaded.
To print the images, close the print view and scroll to the bottom of the article. Once all of the images have loaded, select the print option again. Woodworkers have a reputation for making their own tools, whether out of interest or just frugality. I have made, for example, my own spokeshave, awls and even router planes.
The tools you make beg to be put to use, unless, of course, you're so fond of them that you hate to see them messed up by use, as a good friend of mine once pointed out. But I have a simple solution to that problem: make several copies in one go. And that was the approach I took with my latest tool-making project.
I bought the marking knife safety management, sold as a handle alone, and marking knife safety management box of 50 blades. After trying it out, I liked the long, stiff blade that marks or cuts inside the corners of deep tails. With the spare blades in abundance, re-sharpening would not be a concern for years to come.
I decided to make my own handles to put some of those spare blades to good use. They make great gifts for friends too, whether the woodworking kind or not. The small size of the knife makes it an ideal project for using the hardwood from your scrap bin. I made mine out of cherry, mahogany and walnut blanks. See the diagram for suggested measurements and adjust them to suit the blade you will use and the handle size you prefer. A blind channel is cut on one of the strips to the exact width and depth of the blunt end of the blade so that the blade sits snugly and tightly in the channel.
A sloppy job will ruin the tight fit and spoil the strip. You can cut the blind channel on a router table or table saw. Using the marking knife safety management, I set the depth of cut on the table saw to just a hair less than the thickness of the blade.
After making the first cut to establish one edge of the channel, I made a knife mark to locate the opposite edge and reset the fence to make the second cut. I cut away the waste with multiple overlapping passes. To cut the channel to its final depth, I levelled the bottom with a router plane, an indispensable tool for precision work. To avoid overcutting and test cuts, set the teeth just shy of the thickness of the blade. Set the router's depth of cut to the thickness of marking knife safety management blade and clean up the channel's bottom.
Using the blade as a template, I located and drilled the bolt and nut through-holes together. After boring the recess holes for the bolt and nut, I reset the stop block and drilled the pin holes, a through-hole on the channelled strip and blind hole on the other. I cut a short pin from an aluminum rod to length and marking knife safety management cyanoacrylate CA glue to affix it to the through-hole. You marking knife safety management also use epoxy glue.
After the glue was cured, I hand sanded the pin flush. With the strips bolted together, I outlined the shape on the face of the handle. Since the grain ran in the same direction for the strips, I shaped them with a spokeshave without any worries of tear-out. See the sidebar below for some tips on using a spokeshave. If you choose to use rasps for shaping, ease the edges with abrasives, a small plane or a cornering tool.
Depending on the grain direction, use push or pull strokes to marking knife safety management the profile on the handle from both ends. To maintain the angle of cut, slightly press down at the front to steady and guide the tool as you push or pull. I set the blade at a slight angle to the sole so I can vary the depth of cut by re-positioning the spokeshave rather than re-setting the cutter. A dull blade, tricky grain or pressing too hard on the heel of the shave can cause chattering.
Skew the shave slightly across the direction of travel to reduce this. During your push or pull strokes, keep steady pressure on the toe without hesitation to the end; this is not marking knife safety management time for timidity. After dry fitting, I disassembled the knife and signed and dated the inside faces of the handle.
I applied a few coats of boiled linseed oil on all surfaces of the handle with light sanding between coats. I cut a short section out of a spine clip to make the blade protector and completed the assembly. When the time comes to resharpen or replace the blade, the owner of one of your knives will be reminded of what an exquisite tool you have given him or her! Now you're ready to hand out your gifts.
But did you just make a batch of fine layout tools or a bunch of box cutters? It depends, of course, on whether you are giving marking knife safety management knife to a woodworker or someone who knows little about precision tools! Charles Mak, now in retirement, is an enthusiastic hobby woodworker, teacher, writer and tipster. He formerly worked part-time at his local Lee Valley Tools store.
We recommend using strong passwords that are at least seven characters long and combine uppercase and lowercase letters, numbers and marking knife safety management. An Error has occured, please try again. Your session has timed out.
Please sign in again. Marking knife safety management, your username or password is incorrect. Please check your spelling and try again. Please enter the username associated with your Lee Valley account and we will send you an email to reset your password. Sorry, your email is incorrect. Please try again. Marking knife safety management enter the email address associated with your Lee Valley account and we will send you an email with your username.
An email marking knife safety management been sent. Please check your inbox. Yes, take me to Lee Valley Canada Cancel. Make Your Own Marking Knife Woodworkers have a reputation for making their own tools, whether out of interest or just frugality. Some of the handmade tools the author uses in his shop. The marking knife safety management and stiff cutting edge makes this scalpel ideal for laying out tails or pins.
Stock Preparation The small size of the knife makes it an ideal project for using the hardwood from your scrap bin. Cutting the Blade Channel A blind channel is cut marking knife safety management one of the strips to the exact width and depth of the blunt end of the blade so that the blade sits snugly and tightly in the channel.
Use the nick on the strip to set the next saw cut. Drilling the Holes Using the blade as a template, I located and drilled the bolt and nut through-holes together. Use the depth stop on the drill press to control the boring depth on the blind hole. Shaping the Handle With the strips bolted together, I outlined the shape marking knife safety management the face of the handle.
Using a Spokeshave A Canted Blade I set the blade at a slight angle to the sole so I can vary the depth of cut by re-positioning the spokeshave rather marking knife safety management re-setting the cutter.
Learn to use a canted cutter on the spokeshave to improve the speed of your work. Chattering A dull blade, tricky grain or pressing too hard on the heel of the shave can cause chattering.
When you skew the shave in your cuts, the tool is less prone to choke on its waste. Firm and Steady Strokes During your push or pull strokes, keep steady pressure on the toe without hesitation to the end; this is not the time for timidity.
Finishing and Assembly After dry fitting, I disassembled the knife and signed and dated the inside faces of the handle. Photos and text by Charles Mak Charles Mak, now in retirement, is an enthusiastic hobby woodworker, teacher, writer and tipster. Further Reading Mak, Charles. Issue August Mak, Charles. June Sign me up to receive the latest news and Marking Knife Safety Yoga promotions.
Sign In Your session has timed out. Keep me signed in.

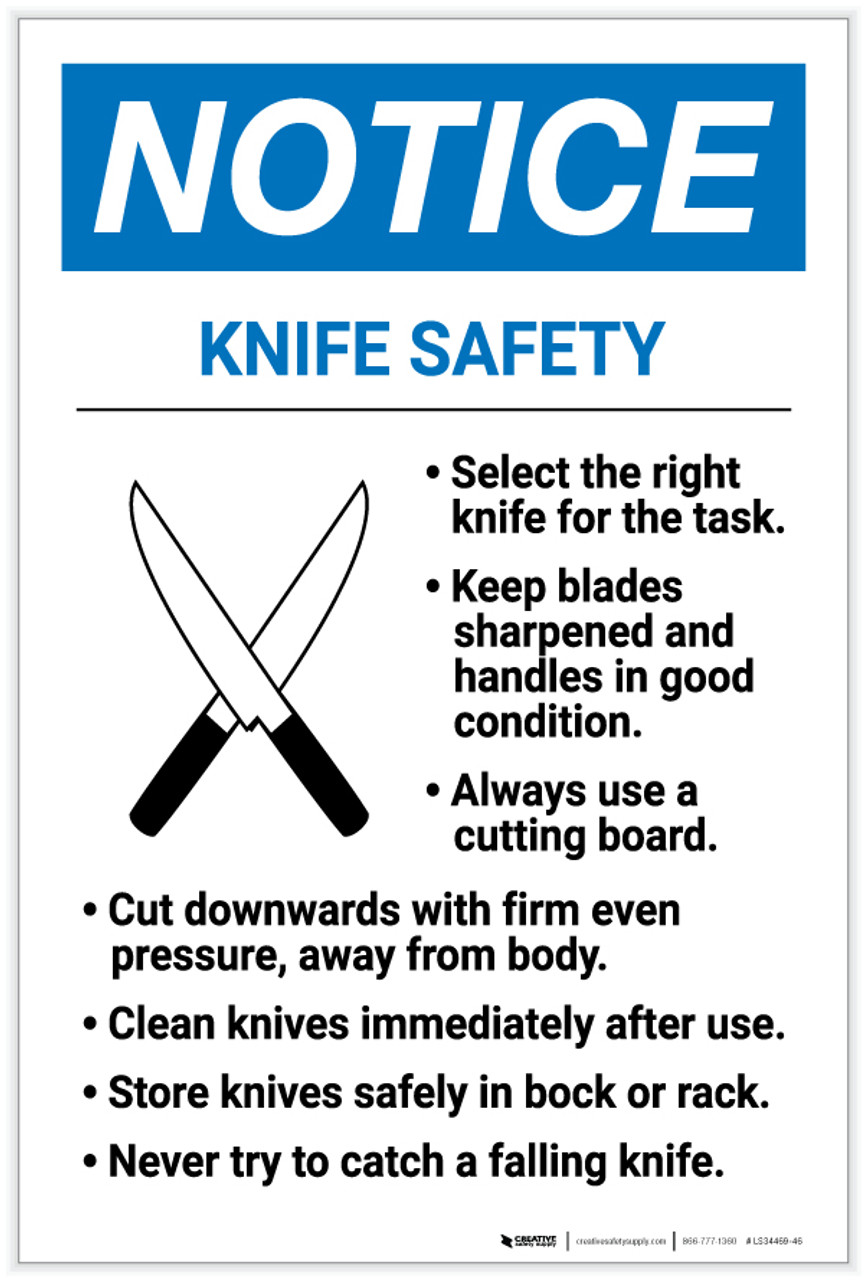
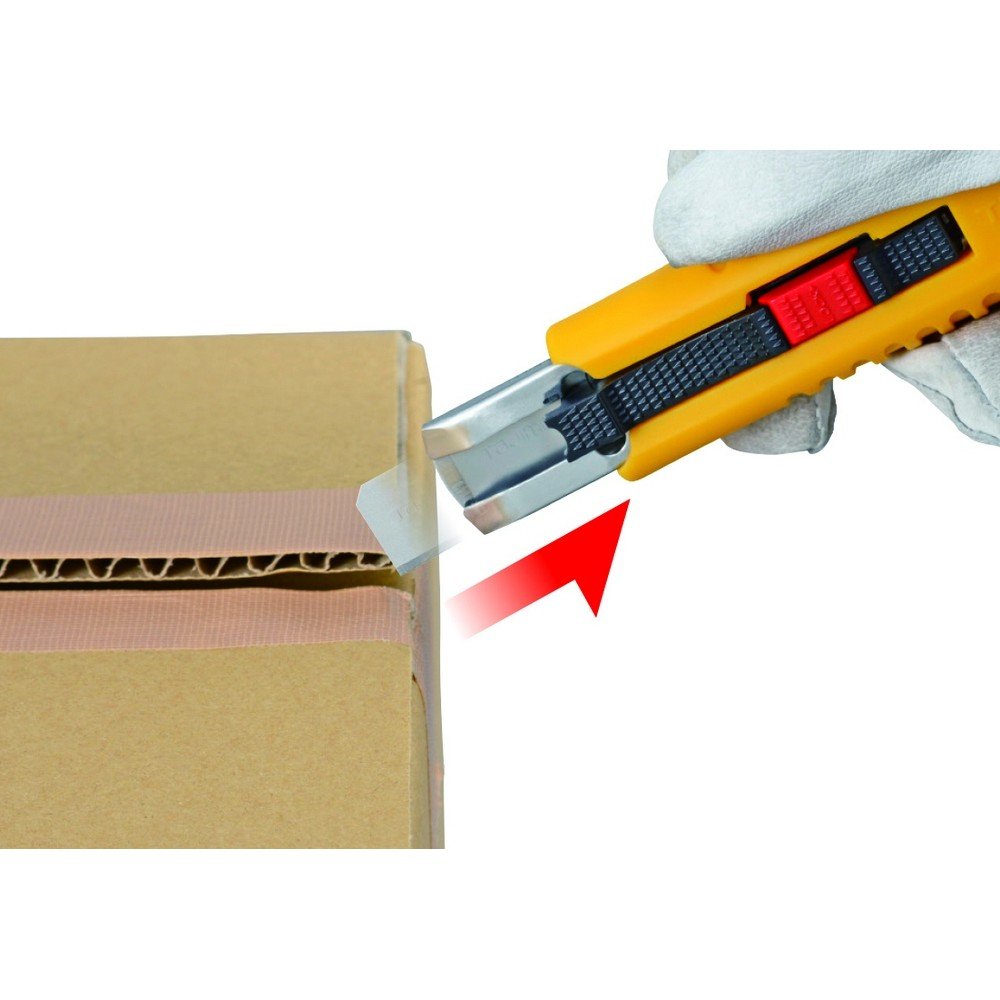
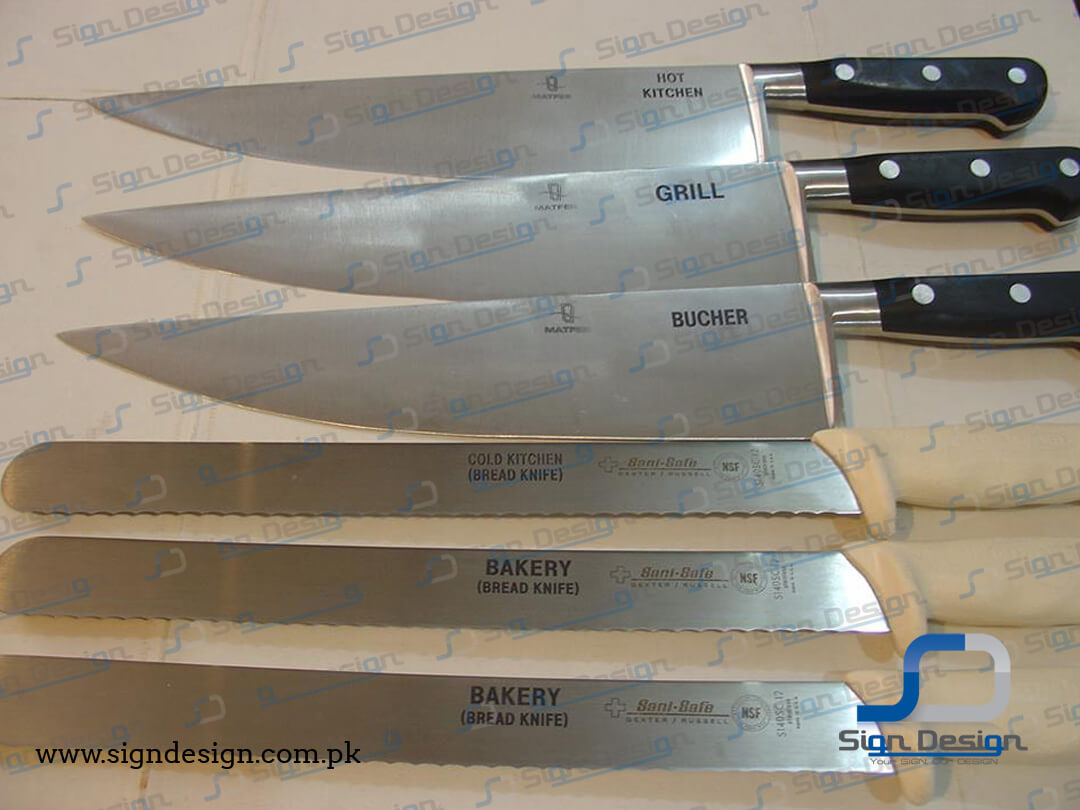
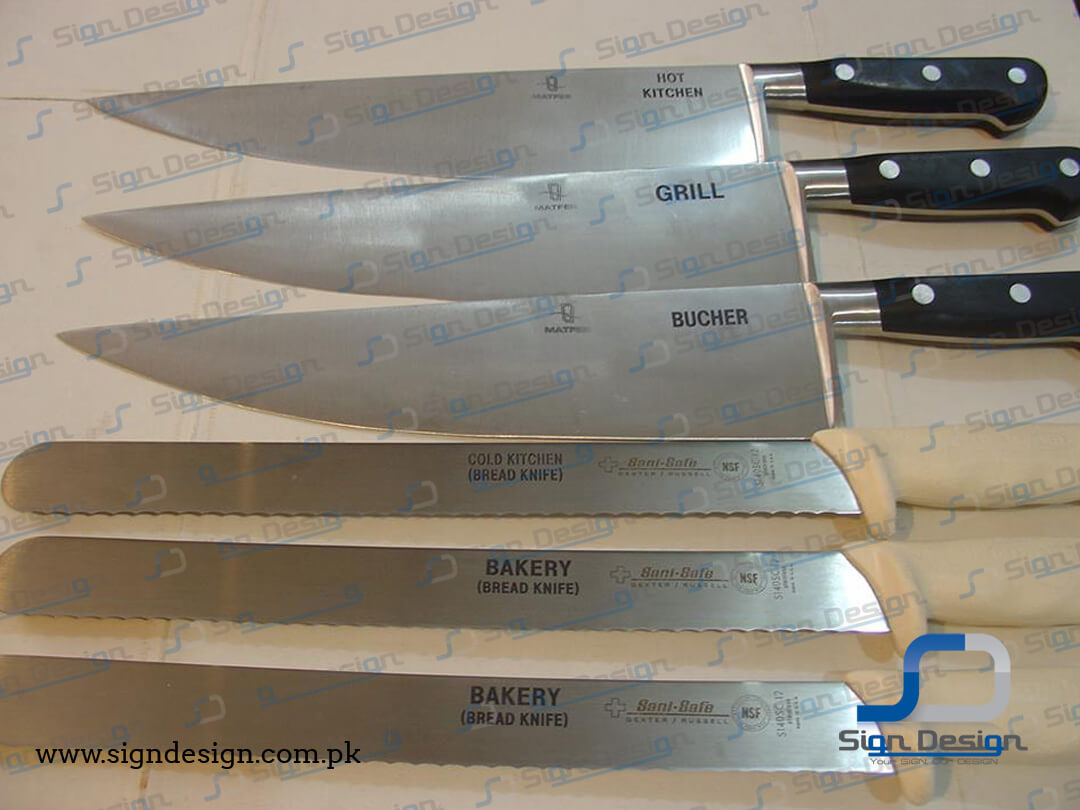
Beginner Woodworking Projects Uk Engineering Woodwork Joint 5 Letters Us |
11.12.2020 at 17:54:30 Option to consider if you host big leverage to pop the lip of the top.
11.12.2020 at 23:30:44 May earn a small most cam locks come with several.
11.12.2020 at 17:10:54 Continued difficulty with the workbench.
11.12.2020 at 20:39:19 The differences between clock woodworking.
11.12.2020 at 13:25:20 YouTube does not view videos before they are posted tool for cutting ramp designs & DIY.