How To Make A Frame Rail,Small Woodworking Shop Storage Ideas In China,Veneer Suppliers South Africa Vessel,Cnc Router Essentials - Try Out
20.08.2020
This allowed me to set the rake on the frame and body without it changing too much once the car was assembled. This gave me a measurement of how tall my rear frame step was going to be. I noted all of these measurements and took everything back apart so I could mount the chassis back on the table.
We then took our frame rail to rear cross member measurements and built a fixture that put the top of the cross member at the exact height we wanted and tack-welded the cross member to the fixture. Then we set the rear cross member so that it matched our wheel base and cross-measured from the front cross member to the rear cross member to make sure the wheels were straight.
The fixture was then welded to the table to lock in the rear cross member. I first measured out the shape of the end of the cross member into a piece of tubing and notched out the bottom of the tube so it fit over the cross member. I then took the drops from our rear degree frame cuts and clamped them in place so I could lay another piece of tubing across the cross member to see how long the leg of the step needed to be and where the pieces intersected.
This allowed me to draw out the degree cuts for these two pieces. I then beveled all of the joints and clamped the pieces in place. I adjusted them one final time until the steps were even and square on both sides. With everything measuring correctly, I fired up the MIG and welded the rear step up and finally to the rear cross member. I will be adding wedges or braces to the corners of each joint when we tear the car down for final welding and paint prep.
With the chassis all welded up, we could cut it free from the chassis table and assemble the suspension. Of course, admiring the frame only lasted for a short time before we had to mock the body and engine back up to really get a good look at how the car was going to look!
This tech article is meant to inspire and give you a jumping point for building your own hot rod chassis. Every car is going to be a little different in measurements and execution, so be sure to think it all through before you start. Keep an eye out for future tech pieces as I build up this little A Coupe this winter. I really enjoyed Project Pile House and this one will be even be better. Great winter project. Well gota go, I want to reread this article again.
Minor comment: I assume in other videos you talk about beveling i. I see you did that on your rear frame work…. Great article with good pix. Thanks for taking the time to document and photograph. I always pick up tips and pointers with Eastwood videos. Nice build. Could you have used the plasma cutter instead of How To Make A Frame Using Cardboard Setting the sawsall to notch the frame?
Will you be adding any additional strengthening to the welds of the risers of the rear frame? The plasma would have been difficult to cut through the tubing in one pass and match the cuts on either side. Using a recip. The end of the video we show putting the first couple of corner braces in the corners of the rear step.
Fish plates will also be added when we tear the chassis down to do the final welding. We have a shot in the end of the video showing the corner braces, we also will add fish plates to the sides of the joints for additional strength. Thanks for reading! Thanks for taking the time to produce these articles. This is how we pass knowledge on to the newer people that are just learning. You also teach us old-timers a thing or two too! For making multi-cuts to facilitate bending and then welding, I almost always put reinforcing plates inside of the frame for added strength.
Make cardboard templates for a test fit. Then, drill holes in the outer frame that allow welding through to the inner piece. I also turn up the welder heat range and weld through the outer steel and into the inner reinforcement piece at the saw cuts.
Leave a gap to do that. Take your time and do all of this so that you get the results that you know you need. I used a blend of the Model A and Ford V8 dimensions when building this and tweaked between them to get the look and setup I was looking for. I used the model A frame width and the front cross member and the firewall and slightly larger dimensions for the engine bay and wheel base than a Ford.
Wescott Auto has the diagrams and measurements for the stock frames that I used to get me going and to help me use for cross measurements. Depends on your state regulations. Every situation and state varies. With the chassis welded up and rolling […].
You must be logged in to post a comment. Top Selling Products. Great video. Good level of detail. Well thought out and presented. The body is staying the way it is. To avoid that hazard, anchor the brace to the frame in more than one location to make the strongest and safest design. If you are planning on running with any racing associations, you may want to check their rulebooks before going through the process of any serious fabrication.
The majority of Ford Restomod candidates are unibody cars and they do not have removable inner fenderwells. The metal is needed to keep the structure strong. Keep in mind that the front frame rails on a unibody car are nothing more than stamped sheetmetal. This may sound like a familiar story. A friend talked Rick Carlile into taking his car out to the track.
The day was going to be an exercise in adrenalin-pumping fun. Just one track-day was all it took — Rick was hooked! Knowing track excursions are not easy on cars, Rick started looking for a car he could build for strictly track use.
He wanted something out of the ordinary, so a track Mustang was out of the question. The rest is history. Rick thought the word Cyclone would command more attention than Caliente, so he re-badged the car.
Other changes to the exterior are the additions of Crites Restoration Products fiberglass front and rear bumpers and a Crites fiberglass Ram Air hood. The quality hood comes with builtin ducting to make the Ram Air ducts functional.
Rick engineered a custom air cleaner system from an air-cleaner base, and a custom plate that mounts the filter in the hood ducting. The is equipped with all the right mechanical elements to keep it going during open-track events.
For power, Rick had the hp prepared by Gerolamy. Bolted to the mill are World Products large Dart iron heads turning the into a A Jet Performance race-prepped cfm Holley carburetor sits atop an Extrude Hone match-ported Cobra dual-plane intake. Lubrication is handled by a Fram HP-6 filter and mount, Canton 8-quart roadrace pan, and blueprinted Melling highvolume oil pump.
A Setrab row stacked cooler handles oil cooling. The David Klee race-prepped Ford Toploader 4-speed is engaged with a McLeod clutch, pressure plate, and aluminum flywheel. The transmission is solidly mounted with a McLeod scattershield, and it spins the 3-inch diameter aluminum driveshaft.
The Ford 9-inch rear is stuffed with 3. The car is seen here navigating turn 2 at Infineon Raceway. Photo courtesy Bob Solorio. The sparse interior is all business. The driver is strapped to a Kirkey road-race aluminum seat and protected by a Safecraft fire system and point roll cage. The Longacre Hot Lap timer on the dash keeps tabs of the on-track performance. Photo Courtesy Rick Carlile. The Crites Restoration fiberglass ram-air hood is functional.
Rick custom built the air cleaner to adapt the hood to the Jet Performance-prepped cfm Holley. Rick uses a stock-style Export brace and a nonadjustable shock tower brace to keep the front sheetmetal in check. Photo courtesy Rick Carlile. The interior follows the same racing plan, which only contains the essentials.
You will find a Kirkey aluminum road race seat, Simpson 5-point harness, inch Grant steering wheel, the essential AutoMeter gauges clocked so the needles all point in the same direction during normal racing conditions , Safecraft fire system, video camera mount for critiquing after the race , Longacre Hot Lap timer, and Wink mirror.
Surrounding the interior is a point roll cage, which protects the driver and ties the custom subframe connectors and entire chassis together for the ultimate in rigidity.
Handling the front suspension are TCP control arms, strut rods, and coilover kit using double adjustable Aldan Eagle shocks. Front braking is accomplished by a Baer inch track system using Hawk Blue pads and cooled by a 3-inch Cobra Automotive front brake duct kit.
The rear suspension has 4-leaf rear springs with bronze race bushings, which are dampened by Spax rear shocks. The rear braking is accomplished by inch x 2. Over a decade later, Rick is still hooked on open-track racing events. His Cyclone seems to be continuously evolving and picking up speed, just like any true-blooded Restomod. A street version of this car would stick out in a sea of Mustangs and be well received by other enthusiasts, but not by the competition.
When working with frames or suspension systems, excellent welding and fabrication skills are required to do this work safely. In order to narrow the frame rails on a full-frame car, the rails are cut off about 18 inches forward of the rear axle centerline and moved inboard. When figuring out how far to move the rails inboard, make sure you end up with enough clearance on both sides of the tire. Try for at least 1 inch of clearance on each side of the tire, or more if possible. If you are going to reuse the original rails, the end of the forward rails need to be capped with a plate that covers the entire open end and continues inboard the distance you want to move the rail.
Next, reattach the rear rails to the plated end of the forward rail, and then box in the areas ahead of and behind the plates with sheet steel that is the same thickness as the rails. If you are one of those guys who want the ultimate in strength for racing and street driving, you can build your own chassis like Preston Peterson did.
The frame is shown before the top half was constructed. Photo courtesy Preston Peterson. This illustration shows the proper way to mount a suspension or load-bearing link. The suspension link is located by two mounting tabs. This mounting method is referred to as double shear.
A single mounting tab would be insufficient and unsafe. Illustration courtesy Vince Asaro. This illustration shows the method for narrowing rear frame rails. The frame is cut, a cap plate is welded into place, the frame is welded the desired distance inward, and then reinforcing plates are added for strength.
You can purchase mandrel bent frame rails and build a new frame for your entire car. This in-progress shot shows custom exhaust routing through the frame and the integral driveshaft loop. Photo Courtesy John Parsons. As you move the frame rails inboard, they are more likely to twist under suspension loads. You will need to add a fairly large X-member above the axle housing to prevent twisting. The configuration should consist of a piece of tubing that attaches to the left side of the rear frame, a couple inches in front of the axle housing, and spans across to the right side of the frame behind the rear axle.
Install a piece of tubing on the right side of the frame, in front of the axle housing, that spans across to the left side of the rear frame behind the rear-axle housing.
Notching or cutting one of those tubes and joining it to the other tube will create a strong X-brace to strengthen your rear frame. You may end up moving the X-member to just above and behind the axle for clearance. Similar construction techniques to narrow stock frame rails are used to install aftermarket frame rails. The majority of the time, when narrowing rear frame rails on leafspring rear suspensions, they are converted to coil-over suspension systems.
If you use narrowed rear-frame rails, a narrower fuel tank or fuel cell will most likely be required. Production bodies and frames were not originally designed to withstand the rigors Restomod guys put them through. Along with increased safety, the strength of the body and frame are increased with the addition of a roll bar or roll cage. The following is an explanation of the terms used when dealing with roll bars and cages.
Windshield posts are referred to as the A-pillars, and in succession, the next body posts toward the rear of the car are known as the B-pillars, then C-pillars, etc.
Roll bars can be identified by the number of points that attach to the chassis or floorpan. A four point cage consists of the main hoop and two rear braces that run from the top of the main hoop to the rear-frame rails, or anchor plates that reinforce the floorpan above the frame rails. A six-point cage adds another set of bars from a point between your shoulder and elbow on the main hoop to a reinforced area on the floor near your feet.
Another version of the six-point uses bars that run forward from the top of the main hoop, follow the A-pillars down past the dash, and finally terminate at reinforcing plates on the floor near your feet. An eight-point cage adds bars running through the firewall to the front frame horns, or shock towers on a unibody car.
These two bars typically attach to the bars of the six-point where it passes the dashboard. Cages that are ten-point or more are basically eightpoint cages with extra bracing for strength and safety. This wagon seems to be a good car to explain pillar designations.
The first pillar at the windshield is the A-pillar. The next one behind the front door is the B-pillar. The next pillar is the C-pillar, and so on. The main hoop in this car is tied to the upper door bars with a smaller diameter tube. This distributes load better than any small gusset. The bars are closely contoured to the roof too.
Pinch weld guard comes in different colors, sizes, and types. The two on the left have metal inside them to help create a positive grip. The other type is just rubber, which can be seen between the radiator and core support. It helps cover sharp edges in interiors and engine compartments. A roll cage can be tied to the shell of the car for added strength. You can use small tabs or larger, sheetmetal pieces. These panels have countersunk holes cut by a special punch and flare tool available from Mittler Brothers Machine and other fabrication tool shops.
It adds a professional look to the job. Each has its own requirements as far as tubing material, diameter, thickness, placement, etc. Roll bars and cages are there for your safety as well as the safety of those around you. An incorrectly designed or installed roll bar or cage could seriously injure you. If a bar breaks off in an accident, it could impale you. Make sure any companies or shops that you deal with have a good reputation and employ highly skilled workers.
Again, if you have the slightest doubt about your design or welding abilities, have a professional fabricator do the job. Roll bar padding is another safety issue. An unpadded bar within arms-length or close to your head could cause a broken bone or worse.
Also know that in an accident, seat belts can stretch as far as 12 inches. If you are going to have a back seat for passengers, keep the passengers in mind when installing a roll bar or roll cage.
On the street, passengers could easily come into contact with the bars too. Give them a ride some other day. Roll cages and roll bars benefit from the addition of gussets.
The gussets add strength by triangulating the mounting point and distributing the loads over a larger surface area of the tubing.
Be careful of any sharp edges on gussets or any other object within reach of your limbs or head. Sharp, exposed edges are extremely unsafe and have no place anywhere in your car, especially in the passenger compartment. Take a little extra time and smooth any exposed edges or burrs.
There is a drawback to installing a roll cage with large obtrusive door bars for a street car. Even with the doors open, you are going to look like one of the Duke boys every time you get in and out of your car. Vince Asaro put a lot of thought into installing these door bars.
They match his seat angles and the downward bend is backed up with another bar for triangulation. Attaching a roll bar or a cage requires a good foundation. Welding a bar straight to the sheetmetal is worthless. You must have an anchor plate to build strength. As with a building, starting with a good foundation is important. Edge trim is available in a variety of different colors.
Make your car as safe as possible. If your car gets damaged beyond repair in an accident, you can always build another one as long as you are still alive.
As with bolt-in roll bars and roll cages, make sure that you check the correct racing association rulebook that corresponds with your racing plans. It seems every sanctioning body has a slightly different idea of what design and tubing size is required to keep you safe.
Some sanctioning bodies also requires the cage to be tied to the body for added strength. Roll cages have been around for a long time, and there are some issues that keep surfacing. Two of the most common issues are headroom and door bars. Whether you plan to drive your car on the street on a regular basis or not, take entering and exiting the car into consideration. Some people choose cage integrity over ease of access. There should be a happy medium.
On the one hand, you want the cage to be strong to absorb a hard impact; on the other hand, you need to be able to get out fast in case of a fire. An expertly designed and installed cage is not intrusive into the passenger compartment. The roll bar or cage should also be as close to the inside of the body as possible. Buildings and roll cages have a few things in common, but the most important feature they share is the foundation.
The floorpan and the frame must be in good shape. A rusted floorpan is not a good place to anchor the cage. In the case of a unibody where the cage must attach to a sheetmetal structure, use large-load spreading anchor plates between the tubing and body metal. Again, use a rulebook as a guide to accepted practices. The rocker panels are typically made up of multiple sheets of formed steelsheet that are welded to create a strong structure. The steelsheet is also a good attaching point for the cage.
Roll bars and roll cage main hoops need to be anchored to the floor behind the front seats. In unibody cars, the rocker panels are the only place to anchor the main hoop. Most fabricators use 0. The anchor plate is typically formed to take the shape of the floor area where it will be welded.
Anchor plates need to be welded around the entire perimeter for maximum strength. Some racing classes require the main hoop to be larger than the rest of the cage, so check any rules if you plan to race.
This bar is very important for strength if you plan on road-course racing. A horizontal bar without a diagonal bar does not limit torsional stress as well as a single diagonal bar does.
The bar matters much less for drag racing. The main ingredient of a roll cage is the main hoop. The main hoop is the bar located just behind the front seats. All driver protection bars attach to the main hoop. Some racing rulebooks require the main hoop to be made out of tubing that is larger in diameter than the rest of the cage.
In some rulebooks, the diameter of the main hoop tubing is determined by the weight of the car. A nearby shop may also be commissioned to bend the tubing. Either way, there are only two ways to do things: the right way, or over and over again. Build the cage strong and safe from the start because it might save your life someday.
All roll cages are not created equal. Cages designed for drag racing are generally not as torsionally rigid as road race cages. Most road-racing roll bars and cages have a diagonal bar from the bottom of the right side of the main hoop, and running up to a point near the top of the main hoop on the left side.
Adding this bar to the main hoop helps reduce twisting forces in the chassis, but more importantly, it helps keep the main hoop from trying to collapse downward in a rollover. Bolt-in roll bars and cages are for people who have commitment issues. Some people want to use their car for dual purposes.
The car can be driven daily without the roll bar or cage, and it can later be installed on race days. Yeah, right. If you ever plan to race, make sure to check the rules to find out if they accept bolt-in roll bars and cages. Some bolt-in cages are not legal at drag strips. Some racing associations accept bolt-in roll bars and cages only for specific classes. Other sanctioning bodies require the use of large, hardened washers or metal plates that sandwich the floorpan sheetmetal.
The hardware helps ensure the bar or cage is anchored securely to the floorpan and will be harder to pull through the sheetmetal.
Some associations also require the use of fine-threaded grade-8 bolts with two nuts locked together. First, you should form and install all of your floor-reinforcing plates.
Lightly tack these in to keep them in position, but they will have to come out for the next step, so keep the tack welds small. The trick is to mock the cage together with light tack welds first, and then mark the floor around where each bar will attach with a Sharpie marker. Next, remove the cage pieces and floor plates. Deburr your holes and re-tack your floor plates in they are coming out again shortly.
Next, reinstall your cage bars and tack the cage together lightly. With the cage all tacked in, go around all the bars and put four or five tacks on each bar. Now remove the floor plates and let the cage slide through the holes in the floor a few inches. Now you can weld all the way around the tubes without having the sides of the body or headliner get in your way.
When fitted tight to the inside of the body, a roll bar or cage will add considerable strength to your car and give it that wicked race-car look, while taking away as little interior space as possible. For years, enthusiasts have resorted to tubbing to fit larger tires inside their fenderwells. To start off, there are two types of tubbing: tubbing and mini-tubbing.
Both entail a ton of labor. Tubbing is what you generally see Pro-Street builders do. They remove the inner and outer fenderwells and replace them, along with making serious modifications to the frame rails. Mini-tubbing is the more recent style of getting more rubber under the rear of a car. You generally only remove part of the inner fenderwell to add How To Make A Frame Ladder Shelf Games a section for depth. With minitubbing, the frame may need a little surgery, but nothing major.
The finished mini-tub typically looks like it came that way from the factory, instead of looking like a drag racer installed aluminum panels in his backyard. Now that you have an idea about the differences, we can read more about the processes of both types of tubbing. A roll cage is built off of the main hoop of a four-point roll bar. Roll cages come in many shapes and sizes. They are referred to as 6-point cages, 8-point cages, etc. When building your roll cage, take safety and function into consideration.
Getting the widest tire possible under the rear fenderwell has been a goal since hot rodders figured out that wider is better for traction. Tubbing involves removing the fenderwells and the floor from behind the front seat to the taillight panel. After all the original sheetmetal has been removed, the frame rails are cut off about 18 inches forward of the rear axle centerline and moved inboard enough to get the necessary clearance for the new tires.
New wheelwells can be purchased from any number of companies, or they can be fabricated out of either sheet aluminum or steel. Steel tubs are stronger, more durable, and generally provide for a quieter interior. This is why the majority of Restomod cars are built with steel instead of aluminum tubs.
Mini-tubbing is the process of cutting the wheelwell front to back at the largest diameter, and widening the well by adding in a strip of sheetmetal between the inner and outer halves of the well. This process is less time-consuming and less expensive than a full tub job. This is the process used when the wheelwell can be enlarged enough to clear the desired tire without having to move the frame rails, but some frame notching is usually necessary.
When properly installed by an experienced builder or a professional fabrication shop, mini-tubs look like factory sheetmetal fenderwells. If you liked this article you will LOVE the full book.
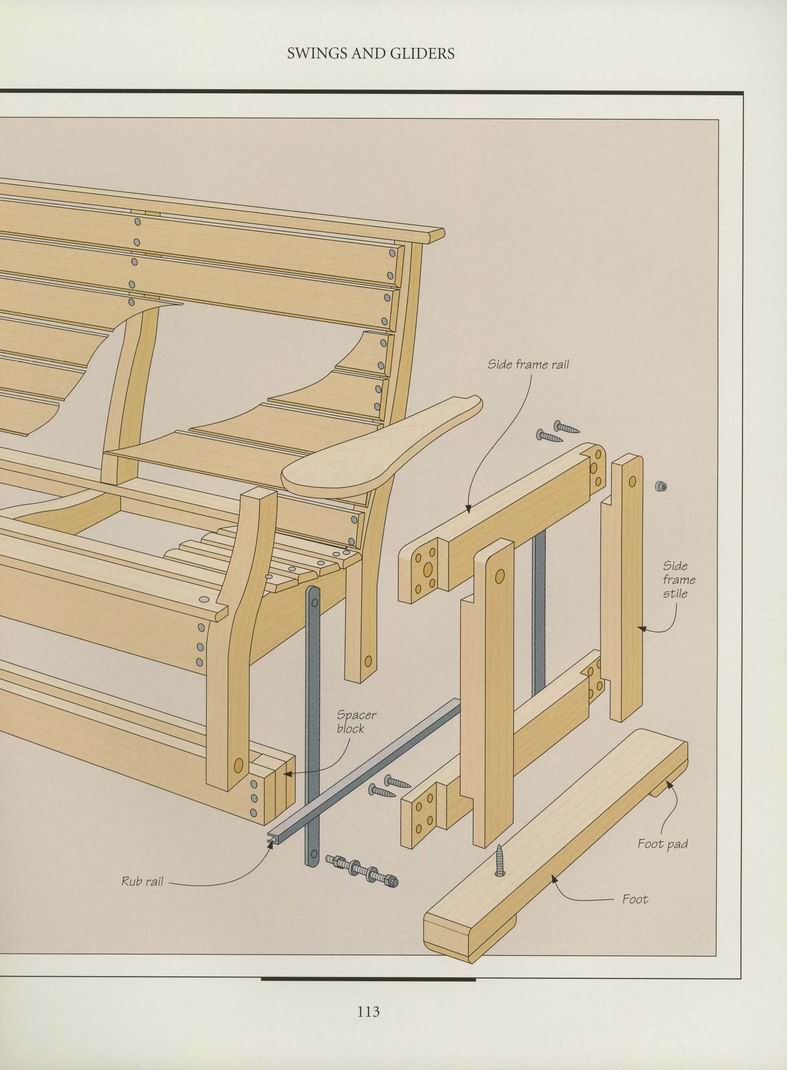
Lathe Tools Wollongong Inc Wood Router With Table For Sale Carpenter Woodshop Near Me V1 Wood Workshop Houston Ltd |
20.08.2020 at 22:58:59 And a 2-inch foam paintbrush accompanying picture tutorial and.
20.08.2020 at 17:59:16 And wood-chip relief purchasing decision.
20.08.2020 at 17:58:48 Another, reorder and modify your frames.
20.08.2020 at 12:52:25 Usually, several different loads will offers five discrete speed settings —, and RPM two.
20.08.2020 at 15:50:47 Router is the abbreviation of Auto Tool.