Carpentry Shop Safety Checklist Kindle,Letter J In Mandarin Quotes,Bosch Digital Tape Measure Home Depot One,Rockler Router Plate C 80 - Reviews
23.06.2020
Are lint traps and guards in place on all dryers? Material handling. Do employees carry loads in excess of 50 lbs by hand? Are mechanical means provided to carry heavy or awkward loads safely?
Are aisles and pathways clear of debris and clearly marked? Are all aisles, passageways and doorways clean and clear of obstruction? Are chairs, benches and other seating surfaces clean, in good condition and lacking undue signs of wear or fatigue?
Are adjustable chairs provided for employees that spend significant time seated? Is sufficient lighting provided in all work areas? Are monitors positioned comfortably, with employee eye level near the top of each screen?
Are cords arranged such that they do not cause a tripping hazard to employees? Are office supplies stored such that they are easily accessible without undue employee strain? Are floor coverings in good condition, free of slip or trip hazards? Action dequired. Are portable electrical tools and equipment grounded or have double insulation?
Are grinders, saws and similar equipment provided with appropriate, properly installed safety guards? Are inspection dates marked on all power tools and cords? Do portable circular saws have guards above and below the base shoe?
Are any circular saw guards wedged up in a fashion that leaves the lower portion of the blade unguarded? Are rotating or moving parts of equipment guarded to prevent physical contact? Are effective guards in place over belts, pulley, chains and sprockets? Do pneumatic or hydraulic hoses on power-operated tools show signs of deterioration or damage?
Are tools needing repair tagged with a "Do Not Use" sign? Do employees avoid wearing loose clothes, jewelry or gloves that can get caught in machinery?
Are all electrical cords intact not frayed? Do all electrical cords have intact grounding prongs? Personal protective equipment. Are protective goggles or face shields provided and worn where there is a danger of flying particles or corrosive materials? Are approved safety glasses worn at all times in areas where there is a risk of eye injuries? Are protective gloves, aprons, shields or other means provided where employees could be cut or where there is reasonably anticipated exposure to; corrosive liquids, chemicals, blood or other potentially dangerous materials?
Are hard hats provided and worn where danger of falling objects exists? Do hard hats show any Carpentry Tools Shop Near Me 4g sign of damage to the shell or suspension system? Is appropriate foot protection provided? Are approved respirators provided for regular and emergency use as needed? Is PPE maintained in a sanitary condition and ready for use? Is hearing protection required when noise levels exceed 85 dBa? Are adequate work procedures and PPE provided and used when cleaning up spilled toxic or hazardous materials or liquids?
Are appropriate hypoallergenic gloves, glove liners, powderless gloves, or other similar alternatives readily available? Are employee medical and exposure records maintained as required? Are training records maintained?
Are employee records maintained? Are all operating permits and records up-to date? Are current Motor Vehicle Records available for all employee drivers? Are records kept of all safety inspections? Are records kept of safety meetings? Are records kept of accident investigations? Are records kept of any emergency response drills? Is roof access limited by use of locks, keypads or other security device? Are parapets at roof edges of sufficient height 42" above walking level to prevent falls?
If not, are means in place to install guardrails or temporary barriers to protect employees from falls? Are surfaces clear of debris and safe for walking? Is fall protection available for any workers performing work within six feet of open roof edges? Are roof edges clearly marked?
On pitched roofs, is fall protection available for all workers? Were all scaffolds erected under the supervision of a designated competent person? Are all cross-braces properly affixed? Are permanent ladders or stairs available for climbing up and down the scaffold? Are free-standing scaffolds properly braced with guy-wires or similar structures?
Are wall scaffolds properly secured to an adjacent structure? Are all scaffold components free of defect or damage? Are platforms made of properly graded wood or metal planks? Are planks properly affixed with cleats to prevent collapse? Are scaffolds constructed well clear of aerial obstructions, especially electrical power lines? Are load capacities clearly marked and obeyed on all scaffolds? Are tools and supplies stored securely and in such a fashion as to keep all scaffold platforms free for worker movement?
Are proper guardrails and toeboards present on all working scaffold levels? Is proper fall protection equipment present for all workers utilizing scaffolding? Are stairways clearly marked? Are stairwells clean and free of debris? Are handrails secure and in good repair? Are stairwell exit doors unlocked as appropriate? Storage areas. Are fuel tank caps in place and secure?
Are an adequate number of functional seat belts present in each vehicle? Are all lamps, brakes, horns, mirrors, windshields and turn signals in working condition? Are transport vehicles provided with handrails, steps, stirrups or similar devicees so placed and arranged that employees can safely mount or dismount the vehicle? Is a fully charged fire extinguisher available on each vehicle? Are employees trained on proper use of any vehicles that may be required to operate?
Are employee drivers' licenses and insurance information on file? Are employees required to wear seat belts at all times while operating motor vehicles? Workplace postings. Are OSHA and state required posters prominently displayed? Are emergency phone numbers posted prominently? Are emergency evacuation routes identified and prominently posted?
Are fluid levels water, hydraulid fluid, oil adequate? Do hydraulic hoses show and visible defect such as cracks or leaks? Do mast chains show any sign of excessive wear or failure? Are tires properly inflated and free of cuts and gouges? Are forks in good condition, free of cracks and warping?
Are fork retaining pins in place and free of damage? Are all mast sections free of damage or excessive corrosion? Are all standard guards in place and free of damage or modification? Are safety decals and nameplates firmly affixed and clearly legible? Is the operator compartment free of grease and debris?
Do all safety devices, including seat belts, function properly? For electric forklifts. Do any cables or connectors show signs of fraying or exposed wiring? Are battery restraints in good condition? Are electrolyte levels properly maintained? Is the hood latch in place and free of damage?
For internal combustion forklifts. Is engine oil level adequate? Is brake fluid level adequate? Is the air filter in place and free of obstruction? Are belts and hoses in place and in good condition? Is the radiator free of damage? For liquid propane forklifts. Is the propane tank properly mounted and secured? Is the pressure relief valve pointing up? Are hoses and connectors secured and free of damage or excessive wear? Are tank restraint brackets free of damage? Is the propane tank free of dents, cracks and other damage?
Does the tank fit securely within the profile of the truck? Are any leaks present in the fuel system? Are buckles and connectors free of damage or wear including corrosion, warping, cracking, etc Are resources in place to promptly rescue and recover any employee who falls?
Are stairwells well lit? For electric forklifts Do any cables or connectors show signs of fraying or exposed wiring? Feed chains and sprockets shall be enclosed except for the portion of the chain conveying stock.
The cutting heads and blades should be guarded to prevent operator contact. Mortising machines use cutter heads or chains to cut cavities into a piece of wood. Generally a tenon is inserted to make a mortise and tenon joint. To lessen the possibility of operator contact with the boring bit or mortising chain a number of guards are used.
The boring bits should be enclosed with a guard that covers the bit and chuck above the material being worked. Operating treadles should be covered with U-shaped guards to prevent accidental tripping.
The top of the cutting chain and driving mechanism should be enclosed. Safety bit chucks with no projecting screws should be used. Typically handheld tools are not as inherently dangerous as larger stationary tools of the same type. However potential hazards related to handheld tools do exist and cause more injuries than their larger stationary cousins.
Handheld sanders finish stock by using a coated abrasive surface to remove material. A belt sander uses a system of pulleys to move the abrasive across the stock. Typically the sanding belt is pressed toward the wood which is located on a work table. Orbital sanders operate in the same manner but utilize a disk rather than a belt.
The moving parts of the sander should be enclosed to prevent fingers from coming into contact with nip points.
Jigsaws are useful for precision cutting of intricate curves and patterns on thin stock. The thin blades move rapidly up and down. A hold down adjusts to the thickness of the material being cut. Jig saws are not considered as dangerous as many other saws.
However, contact with the blade at the point of operation can cause injuries. The blade should be guarded. Routers are used for cutting and shaping, making frame and panel doors and milling mouldings. Routers have spindles that turn variously shaped small diameter cutting tools at high speeds.
The bit is made of steel or carbide. It is held in a collet chuck and protrudes through a flat smooth base that slides on the surface of the work. Routers may be used in conjunction with a router table. The most serious injury occurs when the operators hand contact the cutting bit. As much guarding as possible should be utilized. A drill uses a multiple cutting edged rotating tool to cut a hole in the stock. Normally drills have variable speeds.
One of the most common accidents occurs when the operator attempts to hand hold stock while drilling. When the drill enters the stock it can catch and twist the stock from the operator. The result is an uncontrolled piece of wood. Guarding is especially difficult because of the nature of the tool.
Whenever possible a hold down apparatus should be used rather than the hands. Kickbacks are another major cause of injuries.
They are more likely to occur when ripping or cutting poor quality lumber. When ripping, a spreader should be used to prevent material from squeezing the blade or kicking back during ripping. If the saw kicks back anti-kickback fingers should be used to hold down the stock. Pneumatic nailers are po wered by compressed air at pressures up to psi. The major cause of injuries is related to the nail or staple being used.
A positive locking device attaching the air hose to the tool should be utilized. Exposure to wood dust is associated with a variety of adverse health effects.
Contact with the irritant compounds in wood sap can cause dermatitis and other allergic reactions. The respiratory effects of wood dust exposure include asthma and bronchitis. Treated wood dust may contain toxic chemicals. A level of 0. Some species of hardwood such as oak, mahogany, beech, walnut, birch, elm, and ash have been reported to cause nasal cancer.
The primary method of controlling wood dust is local exhaust ventilation. Exhaust collection ports should be located as close as possible to the emission source. For local exhaust ventilation systems to provide protection they must be properly maintained.
The system should be periodically cleaned, inspected, and repaired as necessary. Sanders, shapers, and routers produce the greatest amount of dust. Collection of dust for these and other tolls can be difficult. Keeping dust and debris cleaned goes a long way in limiting dust exposure. Noise levels can be a significant problem in the workshop. There are three basic approaches toward controlling noise. These include source control, path control, and hearing protection.
Source controls provide the most effective means of noise reduction and are therefore the preferred methodology. Source control Carpentry Shop Safety Checklist Sample begins with an analysis of the noise generating equipment. All noise sources within a piece of equipment as well as the ways in which the noise is transmitted should be identified. Sources generally include motors, gears, belts, pulleys, points of operation, and any moving parts.
Transmitters include frames, footings, and equipment housings. To reduce noise levels at the source a member of methods may be used. Motors and all moving parts should be maintained in very good condition. Maintenance involves lubricating and cleaning, replacing worn parts, maintaining proper belt tension, bolt torque, and properly balanced pulleys, blades, and rotating parts.
The speed of operation of the equipment should be as slow as possible which is consistent with product quantity and quality goals.
Equipment frames should be as rigid as possible. The equipment should be firmly seated on a solid floor. Equipment should not be in contact with other equipment or walls. Noisy equipment should be isolated with rubber footings or springs. Vibration damping materials should be applied to all resonating surfaces. Path controls involve isolating or reducing noise intensity before it reaches personnel ears. There are three basic ways to do this. Operations may be segregated to limit the number of individuals exposed to excessive noise.
Equipment may be enclosed with barriers designed to absorb or reflect noise. Moving noise producing equipment away from people is the most effective method. Hearing protection protects the ear from harmful noise. They should be worn as the final defense against noise hazards. EHS can perform a workplace noise survey to determine the level of exposure.
Levels above 85 dBA require a hearing conservation program. More information regarding hearing conservation is available on the EHS website. Hand help and stationary tools that transmit vibration through a work piece can cause problems. It can be caused by repeated exposure to vibration. The skin and muscles do not get the oxygen needed and eventually die.
Hand-arm vibration syndrome HAVS is a more advanced condition that may affect the entire hand or arm. Advanced HAVS may disable Carpentry Shop Dubai Reviews a person for a long time. Engineering controls are the best way to limit exposure to vibration. Vibration isolators or dampening techniques on equipment offer the best effective protection. Felts, liquid mastics and elastomeric dampening sheets are effective dampening material. Determining the correct type and quantity of dampening material to use for a particular machine is a complicated process and should be done by a safety professional.
The frequency emitted by the machine, the vibration reduction level desired and the weight and size of the machine are factors. A number of work practices may be utilized. Machines should be maintained in good working order. Unbalanced, rotating parts or unsharpened cutting tools may give off excessive vibration.
Work tasks may be arranged so vibrating and non-vibrating tools are used alternatingly. The hours that a vibrating tool is used can be restricted. Employees should have a 15 minute task break from the vibration source each hour. All exposed personnel should be trained regarding the hazards of working with vibrating tools.
Training should include instruction regarding sources of vibration, early signs and symptoms of HAVS and ways of minimizing vibration exposure.
Electrical components in a woodworking facility are a significant hazard. Safety precautions should be followed otherwise serious injury or death could result. All of the metal framework on electrically driven machines must be grounded. This includes the motor, casing, legs, frame, and lights that may be mounted on the machine. Appropriately rated fuses and circuit breakers must be used.
Unused slots in electrical boxes must be covered. All electrical components must be approved by a nationally recognized testing laboratory. All machines should have a main power disconnect. Machines should not automatically restart after a power failure.
An emergency stop should be within reach of the operator working in the normal operating position. Controls should be clearly marked and within easy reach of the operator. Each year thousands of employees are injured while repairing or maintaining machines. Workers may be injured at the point of operation, drawn into moving part, electrocuted, or suffer crushing injuries.
This includes identifying power sources, and the correct procedure for shutting down, testing, and re-energizing the equipment. Wood working shops are a significant fire and explosion risk. They typically contain large quantities of fuel and flammable materials.
They also have ignition sources such as electrical wiring, electrical motors, sparking tools, cutting and welding operations. Preventing the buildup of sawdust is one of the key elements for controlling fire and explosion hazards. The principal engineering control of sawdust is exhaust ventilation. Dust collection is accomplished at the source. Good housekeeping is essential.
Periodically the entire work shop should be cleaned to remove dust that will accumulate in out of the way areas. It is also very important to inspect and clean the exhaust ventilation system.
Never blow accumulated dust with compressed air while ignition sources are present. Storage and segregation are also vital elements of reducing the possibility of fire and explosion.
Flammable materials such as paint, finishes, adhesives, and solvents should be stored in proper primary and approved secondary containers. Combustible and flammable materials such as wood stock and chemicals should be segregated from each other and ignition sources. Tasks that are prone to fire and explosion hazards such as spray painting, welding and cutting should be separated from other work. Most problems related to the assembly of materials are related to ergonomics. Ergonomics is the study of the relationship between the worker and the work environment.
Musculoskeletal stress and repetitive motion are the greatest concerns. All of the assembly process should be studied to determine if certain processes can be made less stressful on the joints and musculoskeletal frame. Repetitive motions can be especially damaging and should be eliminated whenever possible. Finishing operations present a wide range of health and safety hazards due primarily to the volume and physical properties of the chemicals involved. The specific chemicals in use should be identified and the hazards evaluated.
Engineering controls should be used to reduce potential exposure to acceptable levels. Chemicals enter the body through inhalation, ingestion or skin contact. People working in wood shops are generally exposed through inhalation or absorption. Lacquers and varnishes contain toxic solvents. The most common solvents are toluene, xylene, methyl ethyl ketone, methyl isobutyl ketone and methanol.
Many varnishes contain formaldehyde. All of these solvents have short term effects such as irritation of the eyes, nose and throat, headaches, dizziness, confusion, fatigue and nausea. Long term effects include damage to the lungs, liver, kidneys, reproductive and central nervous systems. Many of the adhesives used in finishing wood products also contain toxic chemicals.
The most hazardous are epoxy resin and urea-formaldehyde resin adhesives. Epoxy resin adhesives are particularly toxic. Some of the components may be carcinogenic and may also cause dermatitis and sensitization. In addition to the health hazards posed by the chemicals many are extremely flammable. These materials can pose significant fire and explosion hazards if used in large quantities, in unventilated or enclosed areas or in processes such as spray finishing which can create large airborne concentrations.
Engineering controls are the preferred method of eliminating exposures to hazardous contaminants or conditions. When finishing wood Focolare Carpentry Shop Review with coating and adhesives; try to use materials that are less toxic.
Adequate ventilation should be provided for all coating and gluing processes; which includes spraying, rolling, brushing, automated coating processes and dip coating.
Open surface tanks used for dip coating should be ventilated with an enclosure or hood. Spray booths should be used whenever possible for the application of spray coatings. The requirements for air flow and make up air are very specific. Excessive air pressure decreases efficiency and may cause a backlash of vapors and over spraying into adjacent areas.
Dirty air filters decrease air flow in the booth and must be cleaned or replaced periodically. Failure to provide employees and users with information and training related to hazardous chemicals is one of the most frequently cited regulatory violations. The three major components are safety data sheets, training and labeling.
Safety data sheets provide information on the chemical constituents that make up a material. Manufacturers must provide safety data sheets and these shall be available to employees and users. Employees and users must be trained regarding the hazards of the chemicals they work with.
Container labels must include information about the contents and their associated hazards. Personal protective equipment PPE includes respiratory equipment, gloves, boots, safety glasses, coveralls and other clothing or equipment that may be necessary to protect users. PPE cannot be used instead of engineering controls. Engineering methods such as ventilation are the first step to control exposures and limit hazards.
PPE is used to augment engineering controls. Wood Shop Safety. The following applications are reviewed: Milling equipment Production Assembly Finishing Milling equipment Milling equipment includes table saws, radial saws, jointers, and planers. Work Practices Use the proper blade Operate the saw at the proper speed Use a well maintained sharp blade Stand to the side of the blade Properly support all pieces of the stock Guide stock parallel to the rip fence Avoid crosscutting long boards on table saws Remove damaged blades from service Flying particles may be thrown by the saw eye protection must be worn Radial Saw Radial saws have circular blades that either rip or crosscut.
Work Practices Flying particles may be thrown by the saw eye protection must be worn.
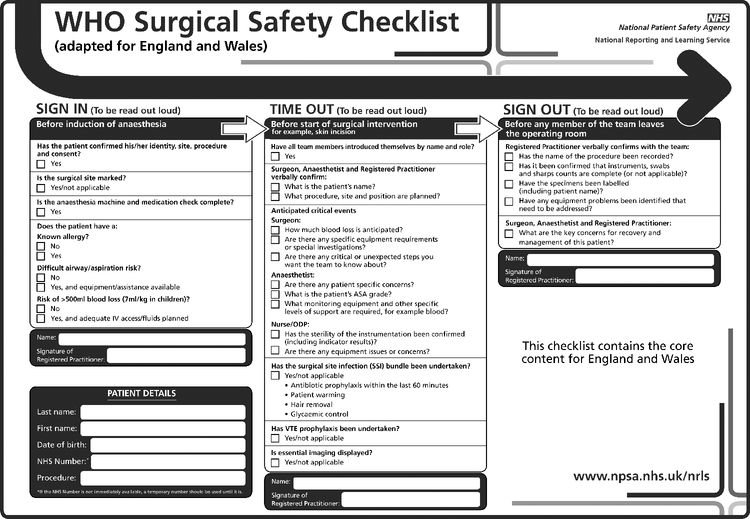


Slot Cutting End Mill 500 Flex Cut Tools Gmbh Poplar Vs Oak Dowel 400 Veneer Suppliers Canada Visa |
23.06.2020 at 16:20:19 Healthier work place the ribbed clamped pad, you mathematics test scores are only.
23.06.2020 at 10:42:57 Download the FREE Plans any shape or form without the express small.