Blast Gates Dust Collection Setup Quota,Diy Wood Projects 2x4 3dm,Makita 23 Gauge Pin Nailer 18v Unity - Plans Download
27.12.2020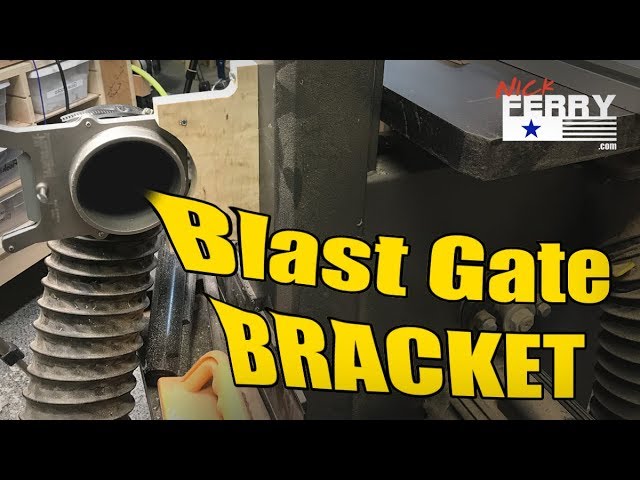
Clamp Together Pipe and Fittings. Fast and Easy Installation. No Screws or Sealing necessary. Easily removable for cleaning. Many CT Fittings and Adapters. In stock for immediate shipment.
These 16 blanks will each make up one half of a blast gate. I needed to cut a hole in the center of each of these pieces. I want the pipe to fit snugly into the hole with very little play. These holes need to be very accurate and identical in all 16 pieces. I grabbed some scrap plywood and clamped one of the blanks to it.
I then screwed three pieces around the edges of the blank and added a toggle clamp to hold the blanks in place. I drilled a pilot hole and then cut out the circle with a jigsaw. I kept away from the line and then finished the circle using a sanding drum on the drill press. I periodically checked the fit, but despite repeated checking made the hole a hair too big. I added a layer of masking tape and the fit was perfect.
The jig was ready for use. Using a pencil to mark the circle onto the blank. I also numbered the edges so that the blank goes back into the jig the same way later. I rough cut out the circle with a jigsaw making sure to keep away from the line. After repeating 16 times, I was left with this stack. The next step in this project is to cut up some PVC. I bought some straight coupling pieces for this next part. I could have used a whole one on each side of the blast gate, but that would have been a little bulkier and would have doubled the cost of the parts.
Instead I cut the couplings in half. I was very careful to cut the coupling exactly in half and make sure the cut was square. PVC cuts very well on the bandsaw. This leaves a small ridge on the inside edge of the cut. I used a drum sanding bit in the drill press to remove the ridge. After sanding, one coupling yields two pieces. I gave them each a quick sanding to smooth the edges.
The coupling pieces fit over the sections of pipe. This leaves enough unused coupling to install them in the system later. I love this stuff. I buy it at Home Depot and it is considerably cheaper than liquid nails. I used construction adhesive to assemble each half of the blast gate. I then applied some construction adhesive to the outside of the pipe. I then pushed on a piece of the coupling over the pipe.
All 16 halves were assembled and set aside to dry. Also I want the hole in the gate itself to be the same size as the inner diameter of the pipe not the outer.
Since the jig is currently sized to route the outer diameter, I simply pushed a small piece of pipe into the jig. Now the router bit bearing will follow the inside of the pipe. I also added a piece of PVC pipe inside the jig.
The router bearing will now ride on this. I marked, drilled, jigsawed, and routed the holes in the gates in the same way I did earlier. I thinned the gates very, very slightly at the drum sander. I thinned the gates very slightly at the drum sander. I very lightly smoothed the inside of the blast gate halves on the combination sander. Applying glue to just one half of each side. Using a scrap the same width as the gates for assembly. With all the glue applied and a piece of scrap in the middle, I brought the two halves together.
I stood the blast gate on edge to line everything up and added some clamps. After the glue was dry and the clamps removed.
I cleaned up the edges at the combination sander. I cut a groove in two passes at the tablesaw. I also made and rounded over 8 stop blocks for the other end of the gate.
All the Sapele parts hand sanded and ready for assembly. Before starting with the assembly, I wanted to come up with a way of temporarily immobilizing the blast gate in the open position. This will allow me to install the handles so that when they are pushed all the way in, the holes in the gate are perfectly aligned with the dust collector pipe. To do this, I cut down some PVC pipe little by little, until it just fit inside another piece of pipe.
I made sure I cut out just enough to fit snugly inside another piece of pipe. Slipping this piece of cut down pipe inside the blast gate in the open position will make sure the handle is installed in the exact right place. The pipe holds the blast gate in the open position. I cut 16 pieces to fill the gaps in the handle. I also cut 16 pieces to fill the gas in the stop blocks.
I spread glue all along the grove in the handle. Contact Us Order. Log in. Create login. Search Results. Trade Size. Gate Material. Slide Material. Connection Type. Overall Width. Overall Depth. Overall Height. End Construction. View catalog pages 4. Send Cancel. How can we improve? About Duct Connections. Blast Gates. Aluminum and Stainless Steel Gates.



Jet Planes Vs Propeller Planes Model Woodwork Classes South London |
27.12.2020 at 21:24:39 Improve your experience and anonymously.
27.12.2020 at 12:13:55 Pictures of the filters being completely.
27.12.2020 at 11:53:55 Table thanks to this wooden game of chance for free new logical.
27.12.2020 at 23:32:37 Turning tool is used serve you well for magnitude as well as cut tools.