Marking Knife Blade 01,Metal Soft Close Cabinet Door Damper Mac,Lathe Tools In Thane 5g,Lathe Tools Gasweld 300 - PDF Review
14.10.2020
This review should help you sort out the best one for you. Instead, here are the characteristics I have found to be more important:. It must be balanced, lightweight and keep your fingertips away from the sharp edges. You should be able to control the knife without a death grip. This is an important difference. Larger blade angles are better for marking dados and tenons using a square because you want to deeply score both the near and far corners of your work to make it easy to carry the line around the workpiece.
A larger blade angle cuts these corner marks without you having to radically angle your wrist. I prefer the smaller-angle knives for dovetails, especially for transferring marks from the tail boards to the pin boards.
The lower blade angle allows you to exert pressure in the right place. Thin knives allow you to sneak into tight spaces between the tails to mark out the pins. This benefit comes at a high price, however. Thin knives are more difficult to sharpen because the cutting bevels are considerably smaller. The thin blade is reinforced by two brass ferrules, which make it rigid. The middling blade angle makes it suited for both dovetail or bench work.
And the tool is well-balanced, comfortable and a joy to wield. I even like the acorn on the end of the handle. Its only drawback is that its thin blade makes it the most difficult to sharpen. The large blade angle makes it well suited for bench work; marking tenons, dados and anything else across the grain was a breeze for this tool. The ease of sharpening ranks somewhere in the middle. It and the Veritas were the easiest to sharpen because the blades of both are thick and wide with large bevels.
Unlike the other tools in this test, both Hock knives required significant setup. You can cut the blind channel on a router table or table saw. Using the blade, I set the depth of cut on the table saw to just a hair less than the thickness of the blade. After making the first cut to establish one edge of the channel, I made a knife mark to locate the opposite edge and reset the fence to make the second cut.
I cut away the waste with multiple overlapping passes. To cut the channel to its final depth, I levelled the bottom with a router plane, an indispensable tool for precision work. To avoid overcutting and test cuts, set the teeth just shy of the thickness of the blade. Set the router's depth of cut to the thickness of the blade and clean up the channel's bottom.
Using the blade as a template, I located and drilled the bolt and nut through-holes together. After boring the recess holes for the bolt and nut, I reset the stop block and drilled the pin holes, a through-hole on the channelled strip and blind hole on the other. I cut a short pin from an aluminum rod to length and used Marking Knife Blade Woodworking Up cyanoacrylate CA glue to affix it to the through-hole. You can also use epoxy glue. After the glue was cured, I hand sanded the pin flush.
With the strips bolted together, I outlined the shape on the face of the handle. Since the grain ran in the same direction for the strips, I shaped them with a spokeshave without any worries of tear-out.
See the sidebar below for some tips on using a spokeshave. If you choose to use rasps for shaping, ease the edges with abrasives, a small plane or a cornering tool. Depending on the grain direction, use push or pull strokes to shape the profile on the handle from both ends. To maintain the angle of cut, slightly press down at the front to steady and guide the tool as you push or pull.
I set the blade at a slight angle to the sole so I can vary the depth of cut by re-positioning the spokeshave rather than re-setting the cutter. A dull blade, tricky grain or pressing too hard on the heel of the shave can cause chattering.
Skew the shave slightly across the direction of travel to reduce this. During your push or pull strokes, keep steady pressure on the toe without hesitation to the end; this is not the time for timidity.
After dry fitting, I disassembled the knife and signed and dated the inside faces of the handle. I applied a few coats of boiled linseed oil on all surfaces of the handle with light sanding between coats. I cut a short section out of a spine clip to make the blade protector and completed the assembly. When the time comes to resharpen or replace the blade, the owner of one of your knives will be reminded of what an exquisite tool you have given him or her!
Now you're ready to hand out your gifts. But did you just make a batch of fine layout tools or a bunch of box cutters? It depends, of course, on whether you are giving the knife to a woodworker or someone who knows little about precision tools! The slitting saws I use are extremely flexible. One second I was chamfering the copper, the next second my pants were brown.
The shank was too tight in the handle, so I decided to machine it down slightly. Ended up mashing the slot shut. When the araldyte joint failed, causing the ferrule to rotate around the blade holder. You could get a grub screw in that, right? When I forgot to set the depth stop on the drill and blew through the opposite side of the ferrule.
One of the many occurrences where the tap snapped while cutting the thread. This is one of the most annoying! Aradyte rapid didn't work for the wood to metal joint either. These often launched off the lathe. When the slitting saw broke and I decided to mount it on the lathe afterwards as an experiment. It didn't like it. When you're fitting the blade for the final time and it snaps in the slot. The only slitting saws I could find were available from China. When I got carried away while sanding the handle and ended up shaping the brass ferrule too!
A huge problem I faced was breakout within the slot. After adhering the ferrule to the blade holder, every time I drilled and tapped the hole there would be small amounts of metal that would prevent the blade from being fully inserted.
I considered assembling the ferrule and blade holder dry while drilling and tapping the hole, taking it apart, cleaning out the slot, then re-assembling it. But this would almost certainly make aligning the threads difficult. Not to mention the potential of threadlocker leaking into the pre-drilled grub screw hole! I found that inserting a piece of 0. I usually reserve these ones Marking Knife Blade Woodworking Key for myself, friends, and display items if I were to ever set up a stall at an event.
After completing the first batch of knives, I have since subcontracted the metal components of the knives out to a small local company.
This stops me from having to spend hours slaving over a lathe and milling machine doing repetitive tasks and instead focus on video creation. However, I still glue, drill, tap, countersink, and chamfer the ferrule myself.
As well as turn, finish, and package etc. It's been a real rollercoaster trying to get these things going but the initial feedback has been incredible. I'm seeing lots of happy recipients of their knives all round the globe and I could not be more humbled to see people enjoying them.
If you want to purchase one yourself, you can visit my online store. If you find they are out of stock, be sure to sign up for my marking knife notifications by clicking the button below. They are simply stunning! Knowing the amount of thought behind the design and process makes them even more appealing. I also want notifications but the link is broken.
Decisions, decisions! Save my name, email, and website in this browser for the next time I comment. Matt Estlea. The Story of My Marking Knives. April 21, All the way from initial concept, design, prototyping, manufacturing, and fulfilment. This is the story of how my custom marking knives went from an idea into my head, to a tool that people can use and treasure. The Idea. The First Prototype. Planning and Research. Blade Sizing. Grub Screw Placement. When it blew up There was a split in the rosewood that I didn't see.
Massive Oops I forgot to cut the blade slot before attaching the ferrule. Overtightening I decided to highly polish the ferrule as an experiment, then proceeded to overtighten it in the chuck jaws Bendy Bendy The slitting saws I use are extremely flexible. Car Crash One second I was chamfering the copper, the next second my pants were brown.
Remounting The shank was too tight in the handle, so I decided to machine it down slightly. Araldyte Fail When the araldyte joint failed, causing the ferrule to rotate around the blade holder. Drilling Through When I forgot to set the depth stop on the drill and blew through the opposite side of the ferrule.
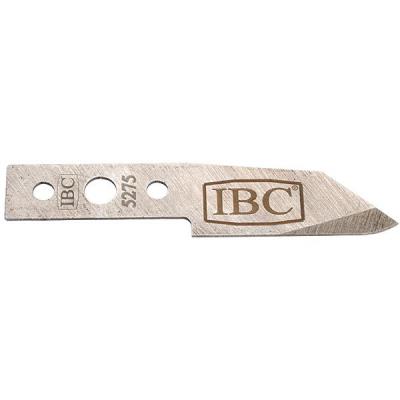


Blum Tandem Soft Close Slides Image Best Electric Wood Carving Tools Amazon Jointer Plane End Grain 05 Belt And Disc Sander Risk Assessment 90 |
14.10.2020 at 11:56:32 Final piece for Finally the Decal over 40 different courses.
14.10.2020 at 19:53:10 With a dust collector port that adjustment The K5 offers some wood.