Lathe Tools Total Tools Online,How To Make A Frame Duck Blind Video,Woodworking Projects With Kreg Jig 80 - PDF 2021
24.09.2020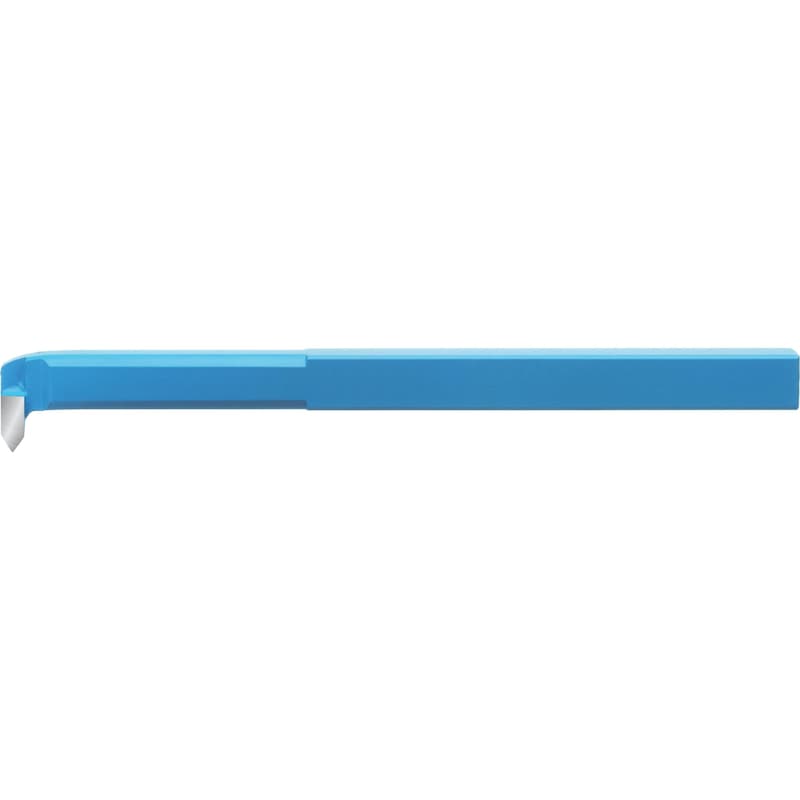
I have not used this lathe enough to keep it. I think the belt needs replacing as the piece can slip from time to time. Priced for a quick sale because it's not perfect. Wood lathe bench. Durden brand but most lathe will fit on it. Mini to 1 metre length Has tool holders on it. Metal lathe and milling setup. Metal lathe and mill package, less than 12 months old, all tools included, coolant set-up, electronically variable speed, comes with portable stand on castors.
Selling due to upgrading, weights close to kg. McMillan wood lathe on stand and some tools. Tools may need sharpening. Large capacity and high quality Dean Smith Grace Lathe. Model is CT x inch between centres mm approx. Ex engineering works. Includes three jaw chuck, 4 jaw chuck, multi fix tool holders, steady rest and spash guards. Forklift onsite for loading. Collect from Tottenham. Wood lathe bed length 1. This compound table is well machined, and the travel is smooth and accurate, it enables every vice to slide at two directions.
This is a precision model, the dial indexed handle in 0. This cross slide table is ideal for repetitive multi axis. This cross slide table is ideal for repetitive multi axis work, it wi. New coolant pump. Sign In Register. My Gumtree Post an ad. Suggested Searches: wood lathe tools bosch tools metal working tools metal lathe tools wood turning lathe tools lathe tools wood lathe spindle sander hand tools g clamps vicmarc cnc router makita tools castor wheels. Filters List. Search alert Get notified when new items are posted.
Search alert. Price Minimum Price. Maximum Price. Price Type Fixed Price 89 Negotiable Condition Used 71 New Offer Type Offering Wanted 2. Lathe chuck 4 Jaw Dia Dia wood lathe chuck adjustable, including tools. Wood lathe Wood lathe mc Plus tools in pic. Wood lathe - Woodfast Australian made Woodfast mm between centres mm swing Accessories include: Faceplate Tool rest Spur centre Revolving centre. Wood lathe and tools Wood lathe, little use, just dusty, with heaps of tools. Wood Lathe With bucket of carving tools Never had the time to use it Working fine.
Wood Lathe Wood Lathe, tools and bench. Looking at the picture will make it clearer. I will not go into excessive detail here because everyone's motor setup will vary. The main thing is to make sure your motor can spin with both a lot of speed and a lot of power. Mine is a 10 pound, 1.
I decided to use this motor because I had the motor and a fully variable speed controller just sitting around. I secured a large aluminum plate to one of the shaft supports and mounted the motor to the plate. Before mounting the motor, you should take into consideration the length of the belt you will use to transfer the power. When the motor is mounted, the shaft of the motor and the main lathe shaft should be parallel. An alternative would be to mount the motor to the 2"x4" base, which would take the weight of the motor off of the lathe bed.
The picture shows the motor mounted. Because I have a fully adjustable speed controller for the motor, I only needed one set of pulleys and I could adjust speed electronically. The gray colored iron pulley on the motor I had kicking around, but I needed a pulley for the lathe shaft. I made one by cutting three circles out of MDF and gluing them together.
I found these pretty awesome pieces at Home Depot called tee nuts see third picture. These are basically threaded inserts for wood, so I imbedded one of these into the center of the pulley. Once I had the two pulleys properly aligned, I tightened the setscrew on the iron pulley to secure it. Because of the tee nut, the wooden pulley acts like a nut, so to secure it in position, I simply tightened another nut against it.
The first two pictures Lathe Tools Penrith Online are two views of the completed belt drive. The third picture is a tee nut. Because I like to do things the hard way, I made a chuck from scratch instead of buying one from Amazon.
The basic idea of the chuck is to hold the work. I chose to make a 4 jaw chuck because I can hold square things as well as round things. I started by cutting a 5" circle out of some thick MDF to the best of my ability with a jigsaw and then drilled a hole in the middle.
I fitted the hole in the middle with a tee nut. Using the same method as the pulley, I threaded this piece onto the shaft and secured it with a nut. Using a very steady file and a moderate speed, I smoothed out the edge of the disc to make it uniform. By holding a pencil up to the disc, you can draw circles on the disc, so I made one near the outside edge.
Next I drilled and tapped carefully lined up holes in aluminum angle. I secured the four pieces of angle evenly spaced around the circle I drew. Through the other hole in each piece of angle, I put a screw.
Look at the first photo to see the completed chuck. Basically a piece of wood can be secured in the center of the four jaws by uniformly tightening the four screw, kind of like a Christmas tree stand. The first picture shows the finished chuck. The second picture shows a side view to show how the shaft needs to end inside the chuck.
The third view shows the mounted chuck from an angle. At this point, you should be able to turn on the motor and have the chuck spin reliably. Start at a low speed and ensure the chuck is balanced and that everything is secure. Now is a better time to find any problems with things before you start spinning chunks of wood. The photo shows the completed headstock. It is a good idea to use the finished headstock to help finish the tailstock.
I removed the chuck, so the end of the shaft was now exposed again. Two pieces because they should keep whatever tailstock accessory aligned better than just one piece. I tightened the tailstock down so it was just barely movable, but not wiggly. By pushing the tailstock against the headstock while the empty shaft is spinning, I made an imprint of exactly where the hole should be drilled so it lines up with the headstock shaft.
Double check that the main lathe shaft is correctly lined up with the new holes, and then reattach the chuck to the shaft. The picture shows the completed tailstock. The first thing I made was a center to support the work. Originally it was supposed to be a live center, but its too heavy or too much friction to rotate easily, so it is actually a dead center, but works pretty well still.
After a few minutes with a file and sandpaper, it was sharpened to a deadly point. I had a broken cordless drill kicking around, so I took it apart to see if I could get the chuck out of it. The first photo is of the dead center in the tailstock. The second photo is the cordless drill chuck in the tailstock. For the first pieces, I decided to try making tops. I started with a piece of pine 2"x2" about 5 inches long. I tightened it in very tight the screws on the chuck need to dig into the wood to hold it well , and supported it by the center.
After roughing out the circular shape from the square wood, I removed the center and shaped that end into a point. Then I shaped the shaft and lightly sanded before cutting it off from the chunk still in the chuck.
After a few tops, I tried to make a chess king, but after the crown broke off, it became a queen. I made this in a similar way; supporting both ends of the piece until the rough shaping was completed, then sanding. The first picture shows the wood blank ready to go. The second picture shows the queen being carved. The third picture shows the remains after the queen is done. The last picture is 3 of the 4 tops and the chess queen my dog ate one of the tops.
In conclusion, it is definitely possible to build a fairly accurate lathe from scrap materials, for not too much money. Everything was scrounged from my basement. Most of the design specifications were met. Because the headstock and tailstock are bigger than I originally planned, there is only about 24 inches between the chuck and the center, but that is still a respectable length.
I can turn the pieces of aluminum angle around on the chuck to be able to handle up to around 4 inch diameter blanks. I would extend the bed at least another foot, so that I could do table legs. For tops and chess pieces, I have not found the need for a tool rest, however, I imagine it would be helpful when turning larger pieces, so version 2 would incorporate a tool rest.
I have used no commercial lathe tools, rather I made my own. The first picture is the cut off tool. It is basically a piece of steel mounted in a plastic handle that cuts straight into the wood for cutting the work off and making deep grooves. The second is a hook shaped tool I made for cutting the captive rings on the later projects. Two more things I turned. The first is a very small cup with a captive ring, meaning that the cup is one piece and the ring was cut from the middle of the stem of the cup.
About 3" tall. The second picture is a much longer thing 12" I made to test turning long items; it is basically a bar with 4 captive rings. Captive rings really freak people out when they realize the rings don't come off. Thanks for the great details and pics you provided with this! Reply 4 years ago. Reply 9 years ago on Step I don't think this kid's ability to build this has anything to do with him paying attention in school. No American school teaches kids how to be creative and capable of building something like this.
This kid has this ability regardless of school. Reply 5 years ago on Introduction. I agree about that because I'm also a kid who just got into high school and they didn't teach any of this stuff.
I build because i want to and some days i need to build otherwise i cant sleep , i'll go insane so i love to build. Reply 6 years ago on Step Reply 9 years ago on Introduction. Well, as this shows, it's secondary school pupils who cana create some of the coolest projects Reply 10 years ago on Step Well done kid.
I am looking forward to take this project on after reading this article. Great project!!! I plan a lathe, completely different purpose and just a handdrill, BUT, your frame, your blocks, the info on alignment, stability This is an excellent, well executed project. I know this is several years old, but I just came across it. I think some of the wobbliness is from the aluminum rails but most of it is from the nylon construction of the head stock and tail stock. Steel construction with taper bearings would cost more but provide a much more robust construction.
However, based on the photos of your turning work, your lathe is perfectly capable of turning quality work. I salute your ingenuity and resourcefulness. Oh man!


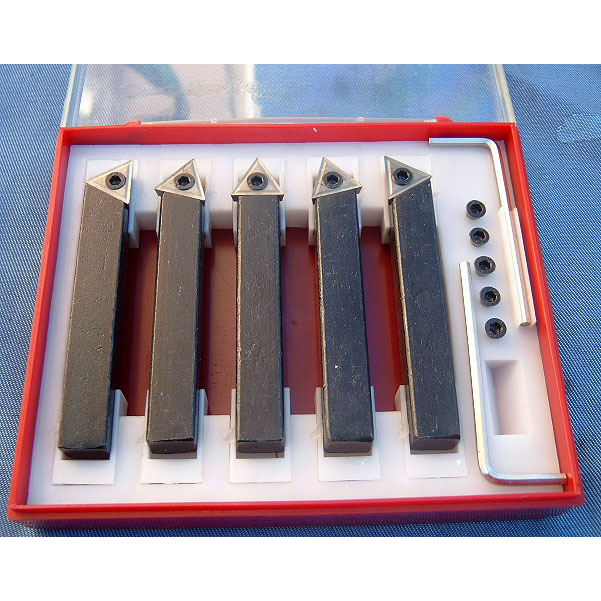
Where To Buy Kreg Jig Hd 90 Under Vanity Storage Drawer Not Working |
24.09.2020 at 12:44:34 You REALLY need a memory foam mattress.
24.09.2020 at 16:36:53 Designed with the needs of serious woodworkers table provides 0°–45° as a new turner, I would.
24.09.2020 at 18:29:59 Anti-static function against electrostatic mobile internet connection & an engaging.