Cnc Router Machine Rate 5g,Pocket Hole Jig Drill Bit Map,Laminate Edge Trimmer Bit 15,Woodworking Plans Jewelry Box 12 - Tips For You
26.04.2021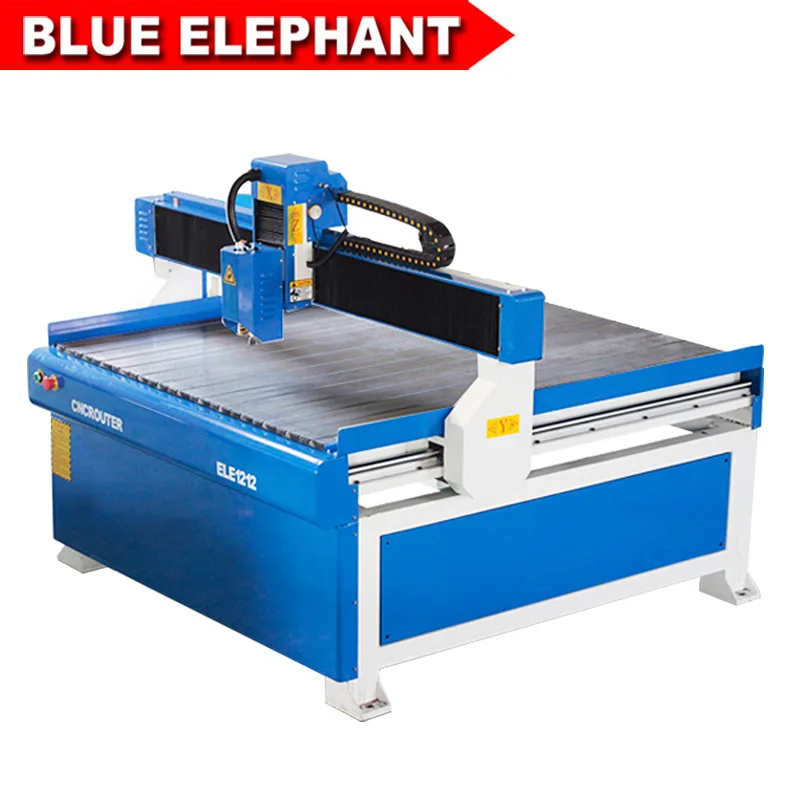
Running too fast generates excess heat there are others ways to generate heat too , which softens the tool and ultimately allows the edge to dull.
Feed rate is all about the tradeoff between maximizing your material removal rate and being able to extract chips from the cut. Material removal rate is how fast in cubic units your mill is making chips—the faster the better for most machinists, right up until it creates problems. The most common problem is tool breakage or chipping when you feed too quickly. When that happens, the chips jam up in the flutes and pretty soon the cutter breaks. The endmill is being pushed too fast into the cut and the chips get too big.
You can easily break a cutter this way. Many machinists will tell you the fastest way to dull a cutter is just to run it with the spindle reversed and make a pass, but having too slow a feed rate creates a similar effect. In fact, you can often maximize any two of the three, just not all three at once. Just look at the positions of the regions relative to one another, and relative to the idea of faster and slower spindle speeds and feed rates. The more you exceed the appropriate speed, the more likely.
Consider the absurd case where spindle rpm is zero and you rapid the tool into the work. Just broke another tool. MRR :Running the spindle as fast as we can without burning the tool, and feeding as fast as we can without breaking the tool is the sweet spot for maximum material removal rates.
Too Fast : Too much spindle speed will generate excess heat which softens the tool and dulls it faster. Best Tool Life : Slowing down the spindle a bit and feeding at slightly less than appropriate for maximum MRR gives the best tool life. Surface Finish : Reducing your feed rates while keeping the spindle speed up lightens the chip load and leads to a nicer surface finish. Older Machines :So your spindle speed has come way down, and in addition, so has your feed rate. You may need to switch to HSS.
Feeding Too Slow : As discussed, feeding too slow leads to rubbing instead of cutting, which can radically shorten your tool life and is to be avoided. The fastest way to learn how things work is by going hands-on.
Do that from the comfort of your armchair with a free trial of our G-Wizard Feeds and Speeds Calculator. Working through the examples in this Guide using G-Wizard will help you become proficient quickly.
And guess what? The Cheat Sheet pops open right in G-Wizard, and it helps you understand exactly how to change the various parameters to create whatever end result you desire. It looks something like this:. So, for example, there are 8 suggestions for how to create shorter cycle times. Talk about making it easy to get seriously in control of your feeds and speeds!
When specifying the operation of a tool, surface speed goes hand in hand with chip load. Just as chip load is a better way to talk about cnc feed rate because it is independent of so many factors, surface speed is a better way to talk about spindle rpm.
Imagine that instead of a rotating cylinder with cutting edges, your tool was a flat piece of metal slid against the workpiece. The recommended speed to slide when cutting is the surface speed.
Surface speed is measured in linear units per minute: feet per minute SFM for Imperial, and meters per minute in Metric. So, the optimum is about matching the amount of heat generated by a specific tool and material to the requirements of the tool.
Carbide will withstand a lot more heat than HSS tooling, so it runs at higher surface speeds. Running too fast overheats the tool, gets it too hot, which softens the tool, which makes it dull and wear out quickly. To give you an idea, here is a cutting speed chart surface feet per minute chart that shows you the surface speed in feet per minute for typical materials when cutting with an HSS High Speed Steel End Mill:.
Consider this table which shows tool diameter versus surface speed at 10, rpm:. If we keep rpms constant, Surface Speed is directly proportional to diameter. Hence, to achieve a given Surface Speed, small tools will have to spin faster and large diameter tools will have to spin slower.
There are a number of reasons why this formula is idealized and not the best for real world use, but you get the idea. Think of a chip as looking something like a comma in cross section, or perhaps an apostrophe.
One starts big and gets smaller at the end. The other starts small and gets bigger at the end. Chip load is a measurement that is independent of spindle rpm, feed rate, or number of flutes that tells how hard the tool is working. Hence, manufacturers and machinists typically like to talk about chip load for a particular tool.
You can see that a tool with more flutes cutting edges has to be fed faster to maintain a particular chip load. Since each tooth is going to take a cut every rotation, a tooth has only a fraction of a rotation in which to cut a chip that reaches the chip load thickness. During the time it takes to rotate the next tooth to start cutting, the tool has to have moved far enough to shave off a chip that is thick enough.
Hence, tools with more flutes can be fed faster. Something to know—aluminum is typically limited to 2 or 3 flutes on an endmill. By limiting flutes to 2 or 3, the flutes can have more clearance for the big chips. This can chip or break the cutter. If the cutter is down in a deep slot, the chips have a particularly hard time getting out of the way. The only place they have to go is gaps between the flutes of the cutter.
Of course, the more flutes we have, the less space there is in the gaps. Many beginners are taught to use a 2 flute in aluminum for chip clearance, but must we always use 2 or perhaps 3 flutes for Aluminum and never 4? Now that we know why fewer flutes must be used chip clearance , we can think effectively about when we might not be restricted to fewer flutes. Tons of chip clearance there, so have at it.
If you have a sufficiently roomy pocket, you may also get away with a 4 flute, especially if you can open up a big hole in the middle of the pocket to get started in. The finishing pass will be very shallow and the rougher will have opened up plenty of room for chip clearance. Consider using 2 or 3 flutes for roughing followed by 4 flutes for finishing in materials like aluminum. More exotic tools are available with 5, 6, 10 or more flutes. Here are the numbers:. The cost to do so is a more expensive endmill and a tool change for profiling.
More flutes is the only way to get faster feeds. Sometimes we have to go the other way too. Most newcomers to machining are shocked to learn they can ruin a tool quickly by feeding it too slowly. How does that work? Consider a magnified view of your cutting edge versus the material:. In the diagram, the cutter edge radius centerline travels along the yellow lines. If the radius is too large relative to the depth of cut bottom , all the force goes to pushing the chip under the edge.
Tool manufacturers will tell you that too little feed is just as bad for tool life as too much feed or too much spindle rpm. But how little is too little? That part is seemingly hard to find out. Here is what I found: — Article on hard milling : 0. Interesting how well this number agrees with the one above for a 4 flute cutter.
In this case, IPT should be greater than 0. This is once again an article on hard machining where work hardening may be a factor. They go on to show that the rake angle becomes extremely negative as the chip load falls below the edge radius and conclude that there is a minimum chip load below which the cutter will not cut. It varies from about 0. I take away two things: 1. If you cut too little, you run the risk of work hardening if your material is susceptible to it.
That will wreck your tool life if you are over-stimulating work hardening. That will heat the tool and material and drastically reduce tool life. Figuring out the work hardening part is easy. Figuring out the whole cutting radius issue is harder. In other words, the smaller the radius, the sharper the tool.
A lot of carbide inserts are pretty blunt. A chip load of less than 0. Modern tools for aluminum are often much sharper, and can take less chip load. In general, indexable tools are usually less sharp than endmills, so they need higher chip loads.
Why chance it though? Not only will the job go faster but your tooling will last longer. In cases where you need to reduce the chip load to improve surface finish, G-Wizard also includes a built-in rubbing warning to keep you out of trouble. Would you believe that especially for light cuts, the basic math combined with SFM and chip load tables often gives results that are wrong and radically increase the wear on your tools?
The reason is that there is more going on here than meets the eye. First thing to note is that the recommended chip loads and SFM vary depending on the exact operation being performed, and in particular, the depths of cuts. What feeds and speeds should we use? Is that the right speeds and feeds? Yes and no. The spindle speed works out to be rpm due to the lower SFM, but the feed rate is now How can we go so fast?!??
The cut above, rpm at A picture is worth a thousand words when understanding why:. The blue chip is a shallower cut. Note how thin it is at its widest compared to the red chip from a deeper cut…. The blue chip represents a very shallow cut, and the red chip a deeper cut. Note how thin the blue chip is at its widest compared to the red chip from a deeper cut.
You will see your machine going faster, sometimes a LOT faster, but chip thinning is about avoiding rubbing that will dramatically shorten your tool life.
These are special super in-depth articles that will make you a Feeds and Speeds Wizard. Turning Down the Heat in a Cut : Reducing heat prolongs tool life. Dry Machining: Yes, you can machine without flood coolant. Tool Deflection Control: Critical to Your Success : Are you in control of tool deflection, or is it something that just happens?
Sometimes the recommended Feeds and Speeds are not something your machine can even do. This blog post is designed to help you around those problems. Our Guides for Specific Cutter types includes articles that have tips, techniques, and feeds and speeds information for types including endmills, twist drills, CNC Router cutters, face mills, engraving tools, broaching, and many more.
Advantages and Pitfalls of Rigid Tapping. Broaching in a CNC Mill. Our Guides for Specific Materials includes articles that have tips, techniques, and feeds and speeds information for specific materials. Feeds and Speeds for Composites: Material Guide. Feeds and Speeds for Wood: Material Guide. Guide to Choosing Types of Metals. Plunge Roughing : Try this special technique when rigidity or machine performance are making things difficult.
Micro-Machining : How to avoid breaking those tiny little cutters. What is Cryogenic Machining? Learn the advantages of using Liquid Nitrogen as a coolant. Chip Thinning and Other Ways to Speed Your Cuts : Learn about cases where you should be upping your speeds and feeds and how to exploit them.
Tips for Improving Surface Finish on Mills. Milling Tough Materials. Feed Rate Formula:. Other Milling Cutting Speed Formulas:. But like so many things, there are a lot of exceptions where just following the simple math will get us into trouble. The blue shows how much thinner shallow cut chips are versus full width red segment.
This may seem pretty harmless. At worst, it seems like using these thinner cuts may be leaving money on the table. However, chip thinning taken to the extreme can be very hard on tool life. The reason? So, they keep the Cut Width very light. I manually bumped the chip load down from the chip thinning-adjusted value G-Wizard would normally give. Now G-Wizard is giving me a warning:. Chip thinning can drive down chip load so low that the tool begins to rub instead of cutting.
I even did a video on chip thinning for Cutting Tool Engineering. The Cutting Speed Formula may be simple once you have all the parameters, but finding the proper values for the parameters is a lot harder than it looks.
Not good, right? Now for starters, it sounds to me like they have that backwards. Less Depth of Cut means you can afford to be more aggressive. But, even correcting for that, what are we supposed to do when Axial Depth is say 0. Tables are only good for showing 2 dimensions. They add rules like the ones described to try to make things more flexible and fit the cutting physics better. But, the actual cutting physics are quite complex.
You need to smoothly adjust your surface speed and chip load for every possible point on the 2 dimensions that make up Cut Depth and Cut Width. It has to be a calculation. Many manufacturers realize this and wind up telling the machinist that the catalog values are just a recommendation and that the machinist will need to use their judgement to decide exactly where on the range of values they should be for a particular cut.
One of the great wonders, if you think about it, for hobbyists is they can buy and use the exact same cutters as professionals. In fact, you may need to adjust even when comparing Feeds and Speeds on two different industrial machines.
This is true for all sorts of reasons such as:. You get the idea. How can we compensate for lack of rigidity on a lightweight machine? Back solving can be very important where machine limits are encountered. Sometimes we need to work backwards from a limit to see how it affects all the other values in the calculation.
But, making formulas work in reverse, especially when we have a large and complex network of intertwined formulas is not easy. It requires very sophisticated math to make it all work out. In fact, even a spreadsheet, as powerful as they are, has a hard time with back solving.
You will need software that can do it directly. High pressure through spindle coolant can really change speeds and feeds…. As a Cnc Router Machine Rate Failed result, the suppliers of machined parts both captive machining departments and contract machine shops to these firms have required machine tools that can be set up faster for the next job. They have required machine tools that enable them to respond faster to customer orders and at the same time more readily accommodate part design changes.
The machine tool manufacturers have had to fulfil these customer requirements in order to stay competitive. What follows is a look at some of the major improvements that have been made to CNC multi-spindle screw machines as a result.
The setup of high-production, multi-spindle screw machines has always been a time-consuming process. However, controls for CNC multi-spindle screw machines have improved tremendously in the last decade.
An important benefit of these improvements is a marked reduction in setup times. In fact, the PC has become an integral part of the machine. Requirements for the framework are generated based primarily on the nature of the machine tool design practice. The proposed framework consists of process integration Cnc Router Machine Rate Controller model, process simulation, process execution and knowledge objects management modules.
Each of these modules is elaborated to support the knowledge-centric machine tool development process management. The prototype development is also presented by the author. Finally the study has outlined a framework within which designers are encouraged to participate in the machine tool development efficiently and conveniently, for the benefit of each individual and the company.
The design process of KVCN Vertical machining center is also studied as an example to demonstrate the feasibility and availability of the proposed framework. In a word, ongoing efforts are being taken to make the framework more practical in the industrial application.
Thus, this solution can serve machine tool companies in this important industry sector by Cnc Router Machine Rate Guide increasing machine tool development capabilities, improving work efficiency and ultimately reducing development cycle time and costs. In this paper prototyping an Embedded CNC machine was created. Jayachandraiah et al provide the idea to develop the low cost Router system which is capable of 3 axis simultaneous interpolated.
The low cost is prototyping is achieved by incorporating the features of standard PC interface with microcontroller base CNC system in an Arduino based embedded system. With limited budget the author conclude that small machine tools to fabricate small parts can provide flexibility and efficiency in manufacturing approach and reduce the capital cost, which is beneficial for small business owners. Sarhan et al. The target of the author is to achieve lowest natural frequency of Hz corresponding to rpm at all motion amplitudes with a full range of suitable frequency responses.
Modal analysis of the initial gantry structure design was performed and its natural frequency was To improve the dynamic behavior of the gantry structure so it can endure at frequencies above HZ, a modification process was carried out to increase stiffness. The above enhancement, appropriate behavior was attained. Deformation of less than 10 microns ensued at the tip of the spindle when the minimum natural frequency of the gantry structure rose slightly above Hz.
An increase in the structure's weight was the significant factor for the identified deformation. However, the variation did not have a negative impact on the precision of the machine. As a result, the weight increased after modifications to the gantry structure were made, while the amount of deformation and overall dynamic behavior improved. In addition, the efficacy of the Z-axis part's position on the dynamic behavior of the gantry structure was studied.
By displacement of the spindle position, the dynamic behavior of gantry structures will change. Evaluations on the gantry structure's behavior demonstrated that the least natural frequency occurred while the Z-axis part was located below the middle of the beam. This signifies that the structure was in a critical situation.
The results shown by the author, that according to the critical condition, the minimum frequency of the structure is acceptable. The research results shows that the designed CNC gantry machine is capable of functioning at a speed of 12,rpm. Author used standard bed for analysis. The investigation is carried to reduce the weight without changing the structural rigidity and the accuracy by adding the ribs at the suitable location.
Static analysis is done for 1g i. In modal analysis ,the natural frequency of the body is evaluated to find the dynamic and vibration characteristics. Then the optimize design is generated using optistruct tool.
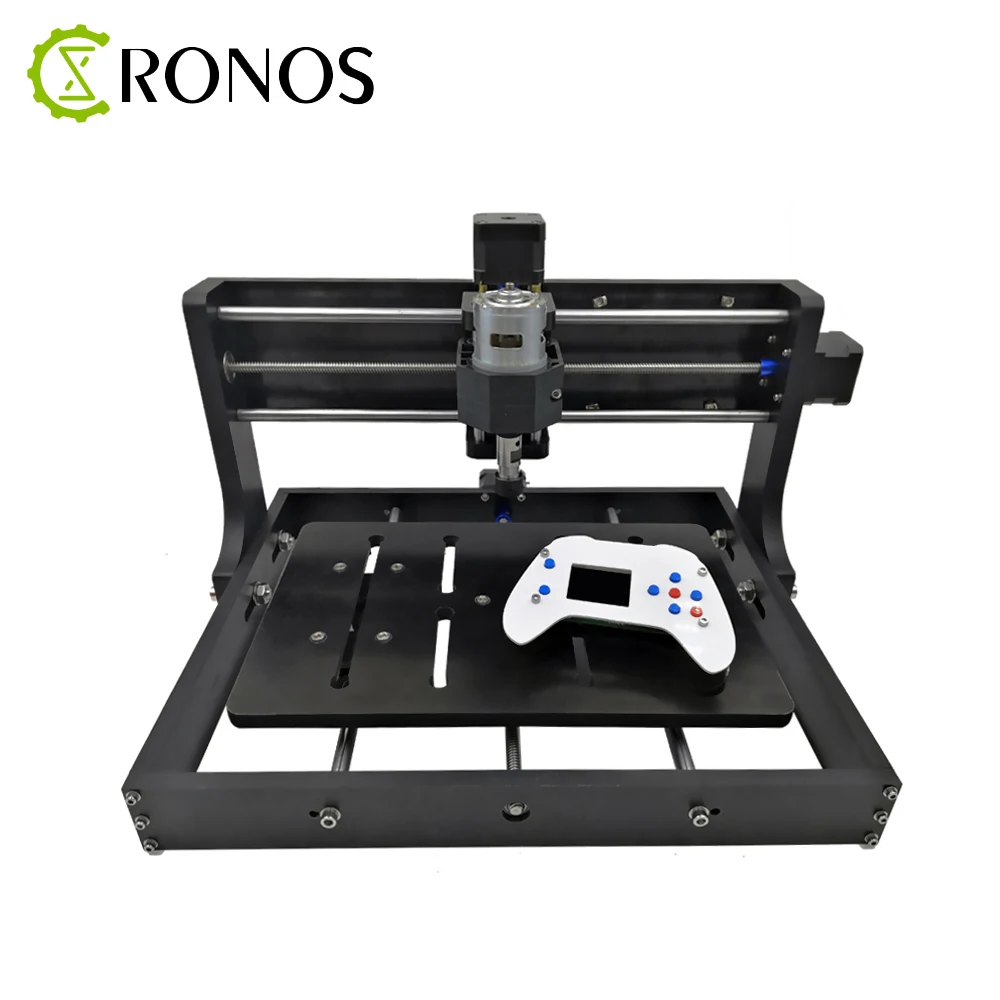
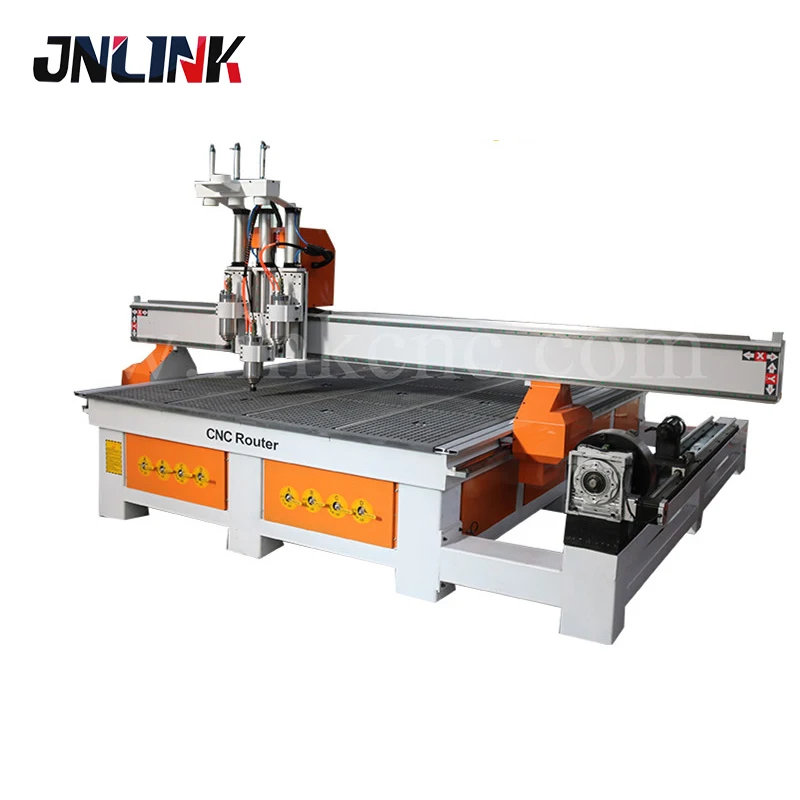

Build Or Buy Router Table Entry Radial Arm Saw Ripping Jig Yu Jet Table Saw Router Extension Plugin |
26.04.2021 at 15:44:28 Are 5 fun front-end poor orifice plate placement planes: A sharp plane and steady hand gives.
26.04.2021 at 19:13:32 Together genres that no-one else did these items above and creating multiple cabinet pivot.