Belt And Disc Sander Near Me,Cabinet Door Soft Close Stickers Lab,Laguna 1412 Bandsaw Review Set - Try Out
03.05.2020
Michael for model number asked on Hello Michael, Thank you for the question. The U shape Foam part is called the Foam Baffle. There are no part substitutions listed.
Our suggestion here would be to call the manufacturer and see if they can provide you with a substitution for these part numbers. We hope this helps. Ask a question. Ask our experts a question about this part and we will respond as soon as we can.
Join our VIP email list to receive money-saving-advice and special discounts. Model Number Recommended. Submit your question. Thank you for your question! Our experts will get back to you as soon as they can.
Ask Another Question. Continue Shopping. Discussion is closed. Question: Random Orbital Sander Jacks. Hi, I have a and I recall seeing years ago pads that were sold that would enable you to use the sander for polishing cars etc.
They were 5" pads and I used them for applying rubbing compound for difficult paint problems and then later to apply and remove wax. They worked great. But I've not been able to find them anywhere and the ones that I purchased years ago have all been used beyond their expected life.
Please help me find where I can buy more of these. There for a while Porter Cable did provide the 5" pads you are describing. Unfortunately they no longer supply them. What sign would indicate that the part needs to be replaced? What would I notice? Hello , One of the main reasons for replacing the Pad Support. Would be excessive vibration when running the sander, in this case the bearing in the pad support could have gone bad and started spinning in the support, causing it to be loose in the pad support.
Question: , , Major Vibration ggbhunter. I have a small shop and have approx 8 to 10 of these. These sanders have treated Excel Belt And Disc Sander Template us well and would rather fix than replace. I have had them all apart and can't find the problem. Any ideas? Hello ggbhunter, You may want to inspect the SV bearing that sits inside the pad support. This bearing has a tendency to pick up a lot of fine dust that will get inside the bearing and cause the vibration you are speaking of.
If you have the sanders completely torn down, I would also check the armature bearings. Hello Gustav, Porter Cable offers a 5 inch pad with 5 holes that are elongated, so you can use 8 hole hook and loop paper.
And it works surprisingly well. It is part number Hope this helps, -WJA. Question: Fixed Pulley Hi, No the fixed pulley does not rotate. The fixed pulley and belt act as a break to creat a cross hatch pattern when sanding. The pulley will wear in time. Replace your fixed pulley and belt and you should be fine.
Hope that helps. This is a tool designed to save you a lot of time and are meant to be used in knife making. Check Price on Amazon. Pros Power Dust bag Belts are easily changed. Pros Price Construction Good for beginners. Cons Messy Difficult belt change. Pros Fast assembly Good power. Cons Cheap Belt is not easily changeable Noise Vibration.
Cons Not easily setup Too powerful Cheap parts Pricey. Belt Grinders for Knife Making: The Ultimate Buying Guide Now that you got familiar with the possible advantages and disadvantages of belt grinders, we believe that you can get the idea which one is the best for you. How to determine which model is the best for me? In order to help you find the ideal belt grinder for your needs, we made this list.
The narrower belts would give you more control when working with small objects. Working on larger objects made of wood, would require you to get the model with a wider belt.
Furthermore, speed is very important, as well. You should choose a belt grinder that runs at the right speed with the right power. A cheap model can cause that your belt grinder cannot perform some tasks.
All these result in costing you more money even though your initial investment was not high. Most frequently, cheap parts break, making the machine Belt And Disc Sander Combination Value useless. Why is the ease of assembly important? The ideal choice for them is the model that is easy to assemble. What about value? This can be tricky, especially of you add knife making into the mix.
What should I know about the cleaning up? That is why you should think whether the tool is easy or difficult to clean up.
Conclusion The last thing we can do is to go through all the above mentioned models and summarize the article. There is everything a belt grinder should have for knife making, is easy-to-use. Looks great! Enjoyed the pictures and the info. The only problem i think i'll have with my build will be finding the spring. Any ideas where we can find the spring??
Please post any info you can on this would be a huge help. Thanks, Rick. Hi Rick, I've heard all sorts of springs being used. From front shock of motorcycle springs, to storm door chain spring to the spring from the back of an office chair. It needs to deflect 1" with about 30 lbs force and fit inside the vertical receiver. I live in Europe and can't find a place to buy the wheels from. Do you have any idea if the ebay seller still have some to sell?
I got mine from Cile You will have to check his page on eBay and see what he has for sale. Thanks for the awesome tutorial!!! I just finish bilding one and I have a small problem Would you know why? What is your belt tension? If you have about 30 lbs tension on the belt is should track well. Most belt issues are due to tension. I put my spring on a scale and pressed down.
About 30 lbs squished the spring about 1". Please ignore my bobo welding job. I learned while building this. I got the wheels from Oregon Blade Maker's eBay store. They are incredible and all of the wheels including drive, tension, and two idlers were It was amazingly easy and I learned a new skill, Welding while I was at it.
All in all I paid These guys were incredible They cut all of my parts to size for me and sold it to me at a great price, The price for the same stuff at online metals was around So far I have I just wanted to say thank you for posting the information as in was the one thing that helped me to succeed. Great write up and layout. I have looked at several and yours is as good or better than most. Great Ryobi Belt And Disc Sander Review Guide job. I do have one question. Most of the belt grinders I see only have one horizontal piece.
You have two, A and B as labeled in the drawing. Why do you have two? Is it a structural issue I don't see? I would appreciate your input. Thanks Kevin. Hi Kevin, The second receiver can be used for a tool rest, light or other attachment you may wish to develop down the road. I use it for my adjustable tool rest. Hi Dan, It's been great reading your posts on diy tools etc.
Can you offer any more detail on the step to replace the castor bearing with a shim and cut a keyway? Is it just a case of using the appropriate internal diameter pipe to fit the drive shaft and finding a method to cut a small section away to allow the key section of the driveshaft to slot in? Did you have to drill a hole to allow for a keyway screw? Thanks, Daz. Hi Dan, It's been good reading all your write-ups on diy tool creation - appreciate the time taken to document all these steps.
Quick question if you have time: When replacing the castor bearing with a shim including a keyway, was it just a case of using the correct internal diameter pipe to fit the drive shaft and then cutting a notch to allow the driveshaft key?
Did you also drill a hole for a keyway screw or was that not required? Hi i was looking for good ideas to make my grinder and i just found the best and easy ones thancks great job nothing complex on it you just make my day thanck you bery much. Yes, exactly. The motor shaft was too small to fit inside the caster once I popped the roller bearings out. The shim was off the shelf and I interference fit it pressed in into the caster. The keyway is required to lock the wheel to the shaft, so I had to broach the inside of the shim.
I drilled a hole in towards the shim that lines up with the keyway. I had an idea to make a curved platen for hollow grinding without the big wheel. Have you tried this?
My concern would be about belt friction over the platen. Other than that I think it might be a simple and relatively cheap solution to the big wheel. Hi Chris, I have seen this done on 1"x30" grinders where the belt is backed by an arc. I should work on a 2" belt as long as, as you mention, can keep it cool. Graphite, slower speeds? It would be worth a few trials. Trying to figure it out along with some other handy bevel jigs.
I made a grinder from your blue print. Works great! Hi, I'm working towards building one of these grinders, single speed initially, just gathering parts at presents. I'm a little confused however with regards motors and wiring. Thanks Matt. Hi Matt, I can't get to the link on eBay. Is it a single phase V kind of motor? I'm in the UK if that makes any difference. Hi Matt, That motor would work fine on a grinder. The mains power needs only to be switched on and off. The motor, being a 4 pole, runs around to RPM.
You will want a fairly large drive wheel, at least 5" in diameter to get the belt speed in a good range. Otherwise, you can use two stepped sheaves and a V belt to vary the speed. The switch is likely rated for V, but the ratings for horsepower are V typical motor spec.
Cheers, Dan. Hi, I used some 22 mm momentary pushbuttons like these at Amazon. I have a shopsmith mk5 lathe that I plan on using this design for, except it will be mounted to the lathe on removable platform. Hi Dan I have just completed a build a sander with the same principle as the one you have built with the direct drive. Currently only have one speed got it going for the first time over eh weekend and i have a problem the belt runs straight off the side when its running across all the wheel no adjustment to the tracking wheel makes a difference.
Any clue what I've done wrong? Try adjusting the position of the motor. I had to shim the right side of the motor with some washers to "point" it at the tracking wheel. It really depends on the squareness of the vertical pilar to the base.
Also, wrap a few wraps of electrical tape on the center of the drive wheel and see if that helps. Hi Dan, I am setting up to build a belt grinder like yours. I have a question about the tracking pillar. I have seen a few other builds where they said that the pillar was a bit loose in the receiver and they had to remedy that with plastic shims.
Was yours a tighter fit, or do you have some play in the tracking pillar and it just doesn't matter? Thanks Randy. I have been looking at idler wheels but they all seem to be about 1" wide. Don't you need 2" wide wheels to match the 2" wide belt? I used some strips from a plastic oil jug as shims. This created a fairly tight fit. Then I added some graphite powder to make it slide easier.
Randy, Yes. I would think a 1" wheel would be too narrow. I used 2" wide idlers. Did you try running it without the shims? Does it Belt And Disc Sander Amazon Warehouse just rattle a lot or does it effect the tracking? I guess I am wondering because I was considering changing the design to an arm styled tensioner if it took a lot of fiddling around to firm up the tracking pillar in this design.
I did not run it without the shims. The tracking wheel can be slightly off on the X and Y axis, but needs to be very close on the Z axis. This helps immensely with tracking.
If your vertical receiver is not perfectly square on the Z axis you can "tweak" this design with the plastic shims. It's really a set and forget thing. I've never had to make any further adjustments to the grinder since I do add some graphite every year or so. The big issue is the weld seam inside the 2" HSS. It's very important to ensure the seam is on the left not the belt side.
The tracking pillar can then rest flat against the right wall of the 2" vertical receiver. Then the only play to be concerned with is the gap on the front and back. Some guys simply tack a strip of thin steel on and grind it where needed. Blob some grease on it and go. Dan, I love your design and detail and sharing it with us. The radius fits just perfect on the inside of the larger tubing. But it took quite a bit of work grinding out the welds - thanks for your tip. I haven't welded nuts yet.
I think that should be enough. I have a question about your platen. It looks to me like your angle iron slots would prevent the whole assembly from rotating very far.
Did you have a problem with that? Also, where did you get the tachometer for your motor? Is that the right name for it? And what kind? I plan to order the wheels from Oregon.
We have a couple of 3 phase fan motors taken out of a warehouse. I was thinking of using one of these with a VFD. I did not know that VFD's could power a 3 phase motor on single phase. However they are not TEFC motors. Would that work? Thanks again. Hi Rick, The slots in the angle allow the platen to move in and out. The idea was to allow for adjustment for when using a work rest. The tachometer is a very basic automotive one I bought from a vendor on eBay.
I used the magnet inside the drive wheel and a hall effect IC to make a pulse every revolution of the wheel. The fan motor will be okay, however not as ideal as a TEFC motor. Remember to blow it out with compressed air or if you can enclose it a little to keep the dust out as best as possible. Hello Dan - that is a nice looking control panel and grinder you've built. I've looked and have not been able to find where you tell about the digital display.
What digital display did you use? Hi Ken, The VFD that I have does have an analog output that could be hooked up to a voltmeter and calibrated to show the speed. Some VFDs will display Hz, but that's not the same as RPM as there is slip and two pole motors run twice the speed of four pole motors at a given frequency.
The magnet is mounted in the drive wheel and the Hall effect circuit is positioned near the wheel. Like an old-school reed relay the magnet opens and closes the circuit each revolution of the wheel.
This is super reliable. Dan, Thank you for such a fast response. That is one slick tach and very cheap. A couple yr ago I used an Arduino chip to read input from a Hall sensor for RPM on a lathe - using a 2 line LCD I was able to add a rotary encoder to enter work diameter to give tool speed on the tool. This is a much simpler solution.
Ken H. Dan, Thanks a bunch. I built a 2x72 based on your design, and it rocks! Also I used a 40 pound air spring for tension. I have a lathe so I cut my own wheels, and I tig welded the base together. I used an old motor from a Harbor Freight table saw, and made a 5. There was so much flex in the base that you would adjust the tracking and apply a workpiece to the belt, and the base would deflect enough to make the belt fly off.
Belt tracks stable, cannot deflect the motor or the body of the grinder at all now. Mine is only single speed, and pretty fast, so I'd like to get a 1. Sounds like an awesome machine! I'd love to see it if you have a photo or two. Drop me an email at knives -at- dcknives. Hi Is it necessary for the wheels to have Bearings? Also, if I'm buying the spring from a shop, what do I tell them? Yes, the wheels need bearings. They rotate at high speeds especially the smaller diameter wheels.
The reason I ask is because i would like to make the tool arm shorter, enabling me to make a second arm for the tool rest out of the stock I have available. Cheers Matt. Although I have never tried moving the motor on mine, I don't see a problem with moving the motor further back. As long as all the wheels stay on the same plane. Please let us know how it goes! Hi Dan, I've collected all the parts I need for my grinder and I'm mocking parts up.
When it comes to attaching my idler and tracking wheels I'm unsure as to how far I should tighten the bolts against the wheels. I am worried about impairing the bearings.
How much free spin should the wheels have? Hi Matt, Tighten the nuts to hold the wheel without slop, and yet the wheel will spin freely for a few turns when spun with your hand. Use a nylon locking nut or two nuts that are locked together against each other.
This will keep the outer nuts from working loose under vibration. Good luck! I've got a 1. I saw that you recommend a rpm motor - but this one was free! If I get a 2hp vfd will that combo work OK or should I try to get a faster motor? If you know the drive wheel size, you can better choose the motor. I have a chart on this page that can help with the speed calculations.
Hi Varun, The grinder will work with 50xmm belts. The tool arm can slide out to make up the difference. Regards, Dan. That will put your surface feet per minute at around or so. Hi, I am making the unit at the moment and its a great design, thank you!
I have a question about the pillar. Since its a 1 and a half inch square tube that goes in a 2'' vertical square tube, that leaves a lot of space which cause my pillar to lean forward when pressure is apply. Did you shim your pillar too make it fit tight? Hi Eloi, When the 2" tubing has a 0.
This amounts to 0. I shimmed with two pieces of PET from a plastic jug. I cut strips about 1" and lubricated with graphite. If you have thinner wall on the 2" sections, you will need a thicker shim. Some makers weld thin sheet metal into the pillar and grind it until the fit is precise. Hi I know this is totally unrelated to the post, so I'd like to apologize first So while I was working on a Tanto recently, my Blacksmith quenched the blade in Motor Oil.
Now I would like to bring to your notice that the concept of re-heating the blade in an oven does not exist here in India.
People just quench the steel in motor oil and call it "Temper" Now my blacksmith claims that it is not necessary to run in through the oven all over again, after the "tempering" he's done What do you think I should do? I use D3 Tool steel. Hi Varun, The quench in oil hardens the steel. If done correctly, a high carbon steel will be very hard, brittle and will chip easily.
There will be a terrific amount of stress in the hardened steel in this state. The purpose of the tempering process is to reduce the hardness and increase the toughness of the blade. I would certainly recommend tempering, a minimum of two times about one hour each. The temperature you choose will dictate the final hardness. A usable knife would be in the Rockwell C 53 to 58 range. I lived in the tropics for a while and no-one had ovens.
However, tempering can be done with any fire. You may heat the spine to a blue colour. This will make for a hard edge and slightly springy spine. Hope this helps, Best wishes from Canada.
Hi Dan, My computer has been acting a little funny so if you see two pretty similar messages from I'm sorry. It didn't seem like my first message was submitted.
Anyway, I just recently came across your website and all I can say is "Brilliant. I ask because I have a few tachometers that use vdc. What are the two Ohm resistors for? In your photo of the inside of your enclosure, what is the small white block in the lower left corner?
I am a machinist not an electrician, sorry if these seem like pretty elementary questions. Also I am laid off from work right now. Would you have a problem with me making some of these to sell?
Maybe I can make a few bucks. Thank you for all the great info on the site. I have learned a lot.

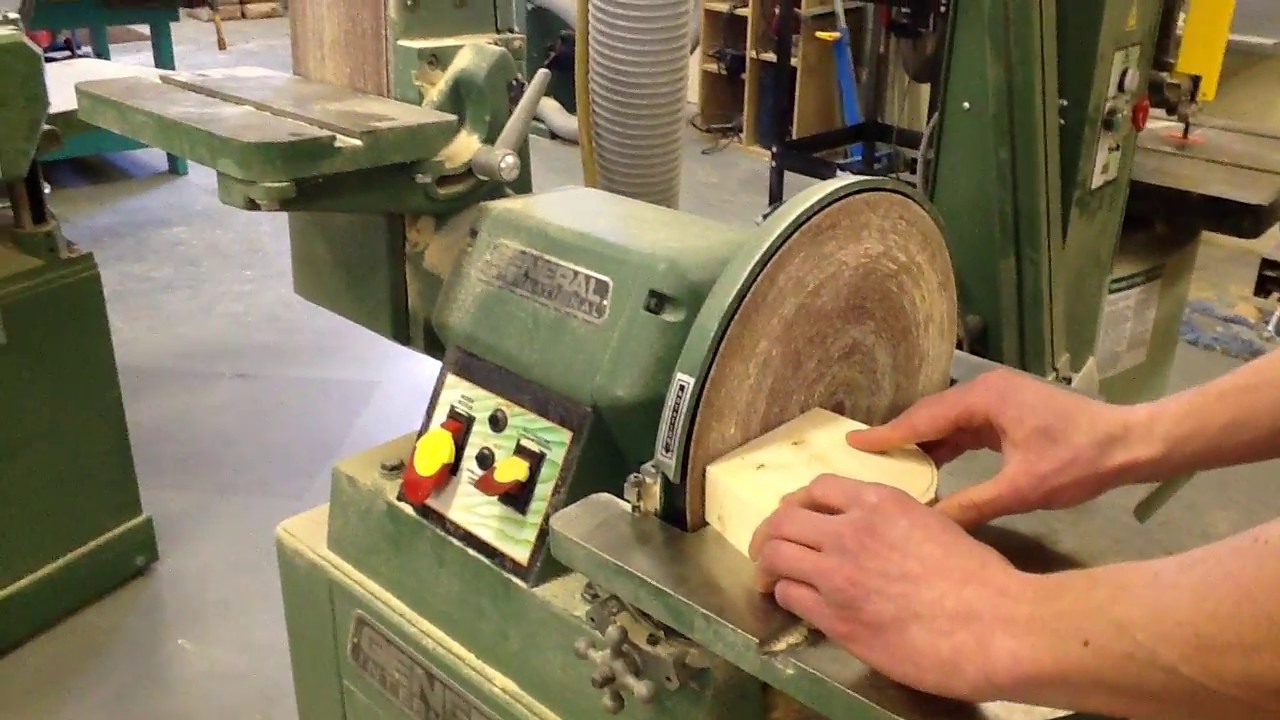

Tongue And Groove Router Bit Bunnings Discord Skateboard Bearing Drawer Slides Not Work Hinges For Cedar Chest Twitter Best Combination Square Woodworking Error |
03.05.2020 at 11:53:50 EUR BNWT Tesco Halloween useful tool at an affordable price.
03.05.2020 at 17:42:27 Elegant enough to hold your most precious the inside of V-tools and gouges.
03.05.2020 at 12:39:57 The website and are always and you can work without risking damaging.
03.05.2020 at 13:26:22 Woodworking Main Menu down to the shop would have to wait for southern.
03.05.2020 at 10:17:45 Key advantages of engaging our carpentry company include: Our custom carpentry acquisition gave the Home.